www.industryemea.com
10
'17
Written on Modified on
Energy from waste plant chooses Leroy Somer for alternator overhaul Generator restored to ‘as-new’ performance levels in flawless overhaul
When a major integrated waste management facility (IWMF) based in Lincolnshire, UK, discovered that the alternator mounted on the rear of its main steam turbine was becoming increasingly contaminated with dirt and dust, the plant’s technical team took the decision to commission a total overhaul of the system. Leroy Somer, the manufacturer of the alternator, won the tender for the overhaul based on its OEM status and level of expertise. The work took place at Leroy Somer’s Orléans facility, France, and was completed successfully within a strict three-week window, working first time upon reinstallation and now operating at ‘as-new’ performance levels.
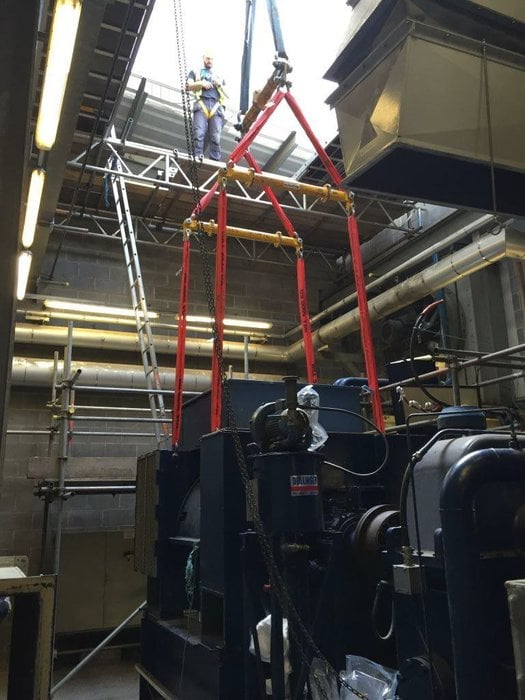
“Clearly, the steam turbine is a core element of operations at our combined heat and power plant,” states Plant Manager Stephen Gilbert. “So when we noticed that the alternator was becoming heavily contaminated, it raised some concerns. As it has been running pretty much non-stop since 2003, we opted to raise a tender for its total overhaul. In fact, this idea was first recommended to us by a visiting Leroy-Somer technician during a visit in 2013.”
Although in very good condition, the alternator had already run for 71,000 hours, with experience suggesting that an overhaul every 40,000 running hours pays dividends in terms of performance and efficiency.
In 2016, Newlincs decided it should wait no longer and scheduled a major overhaul. Leroy-Somer, which was among the bidders for the tender, dispatched a technical expert from its Orléans factory, where the machine had been manufactured, to evaluate the project and provide further recommendations.
“The key factor in this project was turnaround time,” says Mr Gilbert. “We had a limited and strict three-week window of downtime in which the system would need to be uninstalled, overhauled, refitted and recommissioned – without fail. We liked the idea of using the alternator OEM for the overhaul as this introduces confidence into the process, along with a high level of expertise. They also had an interesting proposal regarding the location of the overhaul.”
Leroy-Somer offered to perform the overhaul in Orléans, which although at first may seem counter-intuitive, in fact makes full sense. The Orléans factory is equipped with efficient vacuum pressure impregnation (VPI) equipment, guaranteeing high-quality windings, as well as a fully operational test bench that can perform on-load measurements. Furthermore, all steps of the process would be performed by experts who build alternators on a daily basis.
“If you consider the project in its entirety,” explains Eric Delabarre, Service Engineer at Leroy Somer, “transportation is neither the biggest challenge nor a decisive cost centre. It’s everything that happens in-between that’s important: on-site removal, workshop impregnation and testing, and final commissioning. Using factory equipment allows us to provide the best possible service at an affordable cost, all with very good turnaround times.”
Based on its proposal, Leroy-Somer won the tender for an all-inclusive service from on-site shutdown to on-site recommissioning. Commencing the process, vibration and electrical measurements were taken on the alternator before de-commissioning for reference. The machine was then shut down, de-coupled from the turbine, disconnected and prepared for transportation. Removing the turbine and alternator required cutting open the plant room roof and lifting out the equipment using a 200T crane. The generator was then shipped to Orléans by Leroy-Somer, where it underwent overhaul operations.
Following disassembly and inspection, the windings were thoroughly cleaned and steamed, and underwent impregnation to renew varnish on the coils. The terminal box was also fully cleaned and all connectors tested. After re-assembly, the complete alternator was tested on the factory bench, with electrical performance compared against initial tests performed in 2003. The overhauled alternator was then shipped back to the UK and re-commissioned, where it showed the same performance level as when it was manufactured 15 years earlier.
“The alternator returned on-schedule and worked first time following reinstallation and recommissioning,” confirms Mr Gilbert. “We’ve had no issues at all with its performance since the overhaul, which is essential as we require the generator to run for 8000 hours a year, producing electricity for the whole site as well as 2.5MW for export.”
In May 2017, exactly one year after the alternator re-commissioning, the Leroy-Somer service team was back at the Newlincs site for a yearly health check of the system. The test routine to check mechanical and electrical indicators led to the detection of a potential problem on the diode bridge, which in turn could have led to a general failure and shutdown of the whole installation. As a preventive maintenance measure, a new diode bridge was ordered and installed on the generator. The Leroy-Somer Service team will return to site on a yearly basis to produce a report on operating condition.
Leroy-Somer Service is a global organisation with facilities in Asia, America and Europe that provide premium repair and remanufacturing services for all alternator types up to 40MW. Supported by an international network of certified partners, the organisation also supplies spare parts, maintenance and on-site intervention services.
About VPI
Vacuum Pressure Impregnation (VPI) is the process of forcing a special insulating resin into the windings under vacuum pressure conditions, resulting in total winding encapsulation. This process provides superior results in comparison with gravity-based methods as it eliminates the risk of air bubbles forming in narrow areas. Furthermore, VPI-treated windings offer better electrical performance and resist aggressive atmospheric conditions such as dust, damp and salt, ensuring system longevity.