www.industryemea.com
06
'09
Written on Modified on
MEPLE selects CIAT to cool its process water
The installation supplied by CIAT for the Meple (IKO Group) waterproofing systems production plant provides temperatures adjustable from 18 to 28 °C. This allows the plant to reduce discards, increase its productivity and gain in production flexibility.
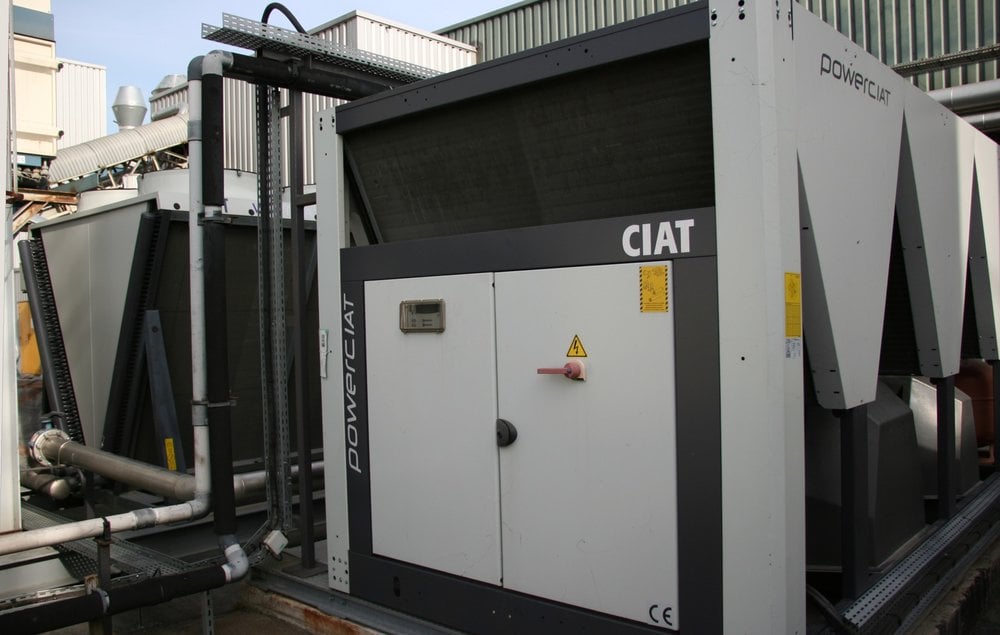
Meple SA is a company in the Canadian family-owned IKO Group, and specializes in the design, production and distribution of waterproofing systems for flat roofs and roofing. The French plant at Tourville la Rivière is one of the most flexible European industrial sites in the sector for the manufacture of waterproofing products. This extensively-automated production unit is ISO 9001 (version 2000) certified by BVQI for its quality assurance system.
To cool bituminous products after coating, constant cold water is required. The previous installation, obsolescent, raised concerns about Legionella in the cooling tower, which was maintained at 28 °C, too high a temperature. To increase productivity and have the capacity to launch the manufacture of new products using new materials such as polyurethane films, Meple wanted to have water available at temperatures adjustable from 18 to 28 °C, while eliminating the cooling tower.
The CIAT Group was selected by Meple to supply the equipment needed for this new installation. “We appreciated CIAT’s capacity to advise us on the solution to be implemented. They had a full product range and complete technical mastery of the subject. Of course, the proximity of their Normandy branch was also an assurance of rapid response if necessary”, considers Mr Andrejewski, the site manager.
The solution installed by CIAT consists of three subsystems. The 900 kW POWERCIAT LX chilled water production unit handles cooling when the outside temperature exceeds 12 °C. It has a wide operating range, from -15 or -8 °C to 41 or 50 °C, depending on the refrigerant used. It has outstanding energy efficiency, thanks to the use of high-efficiency refrigerants (R134a or R407C), optimized heat exchangers with low refrigerant volumes, high-performance compressors, continuous capacity control and the three-stage oil separator. Then comes a heat exchanger, providing physical separation between the process circuit (loaded water and variable flow rate) and the primary cooling circuit. Finally, a VEXTRA model ‘Free Cooling’ air-cooled module takes over from the refrigeration unit when the outside temperatures are below 12 °C. In this case there is no need to run the compressors when outside cold air can be used. VEXTRA supplies these residual needs economically, without calling on the refrigeration system, just employing fans to draw in outside cold air as a heat sink. VEXTRA is fitted with an AEROConnect monitoring module, in constant communication with the Connect controller of the refrigeration unit. AEROConnect controls the motor-driven fans of the Free Cooling module according to needs and climatic conditions so that priority is always given to production in Free Cooling mode. Between 30% and 65% of the rated capacity of the system is provided in this way. Under these conditions energy efficiency reaches an EER of 26 (delivered cooling capacity divided by input electrical power). In the Meple installation, the air-cooled unit consumes 34 kW while the refrigeration unit consumes 184 kW.
“The energy consumption of the installation is well managed with the VEXTRA system, it’s a very important point. Moreover, the complete control of the cooled water temperature has made a substantial contribution to reducing production discards. We have also achieved major gains in production flexibility. It is evident that CIAT will be a solution examined closely for future needs” concludes Mr Andrejewski.
To cool bituminous products after coating, constant cold water is required. The previous installation, obsolescent, raised concerns about Legionella in the cooling tower, which was maintained at 28 °C, too high a temperature. To increase productivity and have the capacity to launch the manufacture of new products using new materials such as polyurethane films, Meple wanted to have water available at temperatures adjustable from 18 to 28 °C, while eliminating the cooling tower.
The CIAT Group was selected by Meple to supply the equipment needed for this new installation. “We appreciated CIAT’s capacity to advise us on the solution to be implemented. They had a full product range and complete technical mastery of the subject. Of course, the proximity of their Normandy branch was also an assurance of rapid response if necessary”, considers Mr Andrejewski, the site manager.
The solution installed by CIAT consists of three subsystems. The 900 kW POWERCIAT LX chilled water production unit handles cooling when the outside temperature exceeds 12 °C. It has a wide operating range, from -15 or -8 °C to 41 or 50 °C, depending on the refrigerant used. It has outstanding energy efficiency, thanks to the use of high-efficiency refrigerants (R134a or R407C), optimized heat exchangers with low refrigerant volumes, high-performance compressors, continuous capacity control and the three-stage oil separator. Then comes a heat exchanger, providing physical separation between the process circuit (loaded water and variable flow rate) and the primary cooling circuit. Finally, a VEXTRA model ‘Free Cooling’ air-cooled module takes over from the refrigeration unit when the outside temperatures are below 12 °C. In this case there is no need to run the compressors when outside cold air can be used. VEXTRA supplies these residual needs economically, without calling on the refrigeration system, just employing fans to draw in outside cold air as a heat sink. VEXTRA is fitted with an AEROConnect monitoring module, in constant communication with the Connect controller of the refrigeration unit. AEROConnect controls the motor-driven fans of the Free Cooling module according to needs and climatic conditions so that priority is always given to production in Free Cooling mode. Between 30% and 65% of the rated capacity of the system is provided in this way. Under these conditions energy efficiency reaches an EER of 26 (delivered cooling capacity divided by input electrical power). In the Meple installation, the air-cooled unit consumes 34 kW while the refrigeration unit consumes 184 kW.
“The energy consumption of the installation is well managed with the VEXTRA system, it’s a very important point. Moreover, the complete control of the cooled water temperature has made a substantial contribution to reducing production discards. We have also achieved major gains in production flexibility. It is evident that CIAT will be a solution examined closely for future needs” concludes Mr Andrejewski.