www.industryemea.com
24
'10
Written on Modified on
SECHE ENVIRONNEMENT Group chooses PcVue
The SECHE Group and its subsidiary TREDI have chosen ARC Informatique’s PcVue to set the future standard for its plants, including household and industrial waste incineration plants, and biogas power plants. Since its first deployment in 2005, it can now be found in 16 plants and workshops, representing more than 500,000 variables being processed, applied and logged by PcVue.
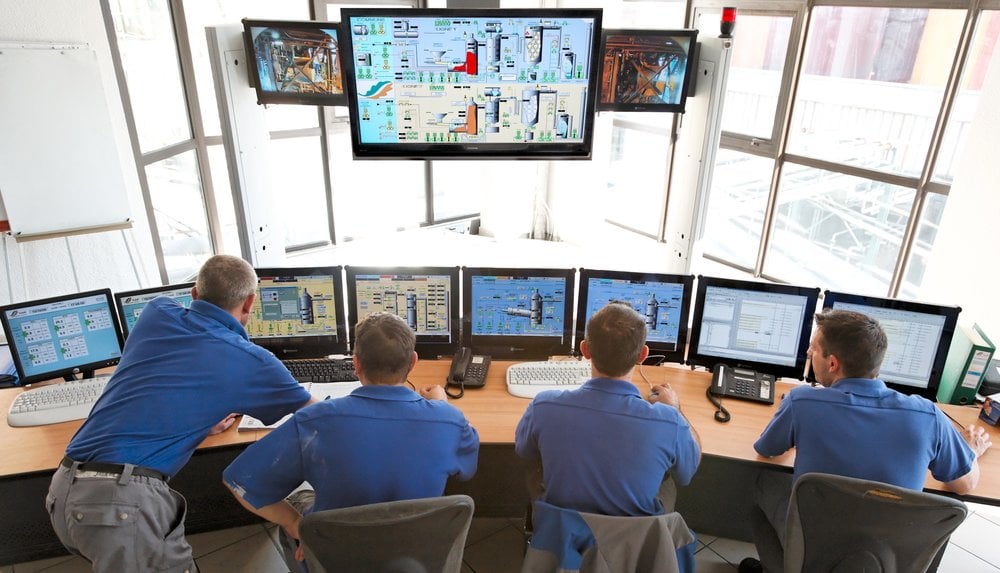
Séché Environnement is one of the biggest players in France and the top specialist in the processing and storage of all kinds of waste (except radioactive waste), whether originating in industry or from local authorities. The Group has more than 20 processing sites in France. Its original position, downstream from collection activities, puts it at the very heart of the most technically demanding industry. TREDI is a subsidiary specialising in hazardous industrial waste. The range of materials processed is immense, covering any waste which cannot be treated like household refuse.
A team of control engineers has been working since 2003 to develop a library of generic objects specific to each of the group’s activities, and to introduce suitable ergonomics and control elements. The Group has decided that it will oversee development of the chosen control system in order to ensure as far as possible that it can be standardised and rolled out efficiently, quickly and consistently across its other plants. So the control applications can easily be grouped together in one single physical location: for some tasks, logging and reporting are already centralised.
The PcVue solution was first installed at the industrial site in SALAISE SUR SANNE (France, Isère) in 2005. This is SECHE Group’s largest heat processing and energy recovery centre: it processes around 250,000 tonnes per year made up of hazardous waste (HW), non-hazardous industrial waste (NHIW), household waste and infectious clinical waste. This first deployment involved the water treatment unit. The priority was to define object standards and a whole special library was developed for PcVue and the logic controllers. The decision was taken to adopt OFS-based communications.
“At the time, we looked at what was available on the market, and the real advantage with PcVue is that it’s a complete solution, with no need to be constantly buying new modules. Since we were already looking to plan long-term for the product, this was a determining factor,” said Mr Therrien, SECHE Group’s Industrial IT Manager.
PcVue was then progressively introduced into units 1, 2 and 3 at the Salaise site. We started with a complete revamp of Salaise Unit 1, with its two rotary furnaces: Here, PcVue supervises all process functions and common tasks, meaning about 30,000 variables are being monitored. Then, with the partial revamping of Salaise 2 following the installation of a new waste injection system, allowing it to operate in sealed mode; this revamp followed the signing of the waste treatment contract which resulted from the illegal dumping of the PROBO KOALA cargo in Ivory Coast. And finally Salaise 3, where the replacement of the control system is currently under way. Rockwell process logic PLCs are to be replaced by Telemecanique PLCs under Unity and PcVue (two input/output servers and 5 client stations).
Mr Therrien adds: “Among the other advantages of PcVue compared with other solutions on the market, we are particularly happy with the object-oriented database organisation. When objects are created, they can very easily find the items, the PLCs to control. In the past, to manage a monitoring variable, you had to name it and set up assignment tables; now we don’t even have work with addresses or variables in the PLC. Exchange tables are created automatically via OPC. Graphical functions are also of great value and easy to implement. It is very easy to switch between “runtime” and development mode. We can then change or add functions to a working plant. Finally, I’d also say that we have experienced a high level of service from PcVue teams and the hotline. »
PcVue is also widely used by the SECHE Group to monitor power plants generating power from the biogas coming from the household waste storage centres. Their drainage and pumping networks collect the biogas generated by the decomposition of the waste, which largely consists of methane. The biogas is then injected into turbines to produce electrical energy.
PcVue has been installed at the DRIMM storage centre near to Toulouse (France, Haute-Garonne) and, more recently the Changé plant just outside Laval (France, Mayenne): A boiler takes the combustion gases from the turbine to produce steam. In Changé, this steam is used to dry fodder from farming operations. PcVue is also installed at the SVO site in Vienne, and the Opale site in Nord Pas de Calais (France).
Key:
-SECHE_1.jpeg : Salaise plant
-SECHE_2.jpeg : Salaise control centre with PcVue block diagrams
-SECHE_3.jpeg : Salaise control centre with PcVue block diagrams:
-SECHE_4.jpeg : PcVue block diagram for biogas power generation plant control
A team of control engineers has been working since 2003 to develop a library of generic objects specific to each of the group’s activities, and to introduce suitable ergonomics and control elements. The Group has decided that it will oversee development of the chosen control system in order to ensure as far as possible that it can be standardised and rolled out efficiently, quickly and consistently across its other plants. So the control applications can easily be grouped together in one single physical location: for some tasks, logging and reporting are already centralised.
The PcVue solution was first installed at the industrial site in SALAISE SUR SANNE (France, Isère) in 2005. This is SECHE Group’s largest heat processing and energy recovery centre: it processes around 250,000 tonnes per year made up of hazardous waste (HW), non-hazardous industrial waste (NHIW), household waste and infectious clinical waste. This first deployment involved the water treatment unit. The priority was to define object standards and a whole special library was developed for PcVue and the logic controllers. The decision was taken to adopt OFS-based communications.
“At the time, we looked at what was available on the market, and the real advantage with PcVue is that it’s a complete solution, with no need to be constantly buying new modules. Since we were already looking to plan long-term for the product, this was a determining factor,” said Mr Therrien, SECHE Group’s Industrial IT Manager.
PcVue was then progressively introduced into units 1, 2 and 3 at the Salaise site. We started with a complete revamp of Salaise Unit 1, with its two rotary furnaces: Here, PcVue supervises all process functions and common tasks, meaning about 30,000 variables are being monitored. Then, with the partial revamping of Salaise 2 following the installation of a new waste injection system, allowing it to operate in sealed mode; this revamp followed the signing of the waste treatment contract which resulted from the illegal dumping of the PROBO KOALA cargo in Ivory Coast. And finally Salaise 3, where the replacement of the control system is currently under way. Rockwell process logic PLCs are to be replaced by Telemecanique PLCs under Unity and PcVue (two input/output servers and 5 client stations).
Mr Therrien adds: “Among the other advantages of PcVue compared with other solutions on the market, we are particularly happy with the object-oriented database organisation. When objects are created, they can very easily find the items, the PLCs to control. In the past, to manage a monitoring variable, you had to name it and set up assignment tables; now we don’t even have work with addresses or variables in the PLC. Exchange tables are created automatically via OPC. Graphical functions are also of great value and easy to implement. It is very easy to switch between “runtime” and development mode. We can then change or add functions to a working plant. Finally, I’d also say that we have experienced a high level of service from PcVue teams and the hotline. »
PcVue is also widely used by the SECHE Group to monitor power plants generating power from the biogas coming from the household waste storage centres. Their drainage and pumping networks collect the biogas generated by the decomposition of the waste, which largely consists of methane. The biogas is then injected into turbines to produce electrical energy.
PcVue has been installed at the DRIMM storage centre near to Toulouse (France, Haute-Garonne) and, more recently the Changé plant just outside Laval (France, Mayenne): A boiler takes the combustion gases from the turbine to produce steam. In Changé, this steam is used to dry fodder from farming operations. PcVue is also installed at the SVO site in Vienne, and the Opale site in Nord Pas de Calais (France).
Key:
-SECHE_1.jpeg : Salaise plant
-SECHE_2.jpeg : Salaise control centre with PcVue block diagrams
-SECHE_3.jpeg : Salaise control centre with PcVue block diagrams:
-SECHE_4.jpeg : PcVue block diagram for biogas power generation plant control