MOOG® Radically Improves Durability and Performance through Revolutionary Hybrid Core Technology
The steering and suspension components in modern cars are significantly better than those in the year 1919: the engineering, material selection, manufacturing methods, build accuracy and part quality have all changed substantially. Innovation after innovation has spurred on a century of incredible automotive design, production and maintenance. The change is, for the most part, incremental and slow, but occasionally a company invests in ideas that truly demonstrate the scale of the industry’s progress.
MOOG®, a brand whose origins trace back to the iconic Ford Model T, has developed a new Hybrid Core bearing technology. Through the use of carbon fibre reinforcement, Hybrid Core Technology significantly increases the bearing durability of MOOG’s control arms, ball joints, tie rod ends and axial rods. Durability and safety are further improved through the use of induction hardening on the components’ studs. Induction hardening is a heat treatment process that provides a fivefold increase to a part’s surface hardness and can double the strength of studs.
The new design also reduces the gradual increase in radial deflection that components can experience during their service-life, commonly and more simply known as ‘play’. Reducing this abnormal increase in deflection means that the precise steering feel and controlled suspension movement is maintained throughout the use of the component.
“The history of innovation is what sets MOOG apart,” explained Massi Milani, executive director, marketing, EMEA aftermarket, Tenneco/Federal-Mogul Motorparts EMEA. “We understand the importance of steering and suspension components in the safety and comfort of a vehicle – two of the most significant and reassuring factors for drivers. That is why we developed Hybrid Core Technology and continue to invest in technologies and processes that provide our customers with advanced and reliable parts.”
Hybrid Core Technology is being introduced on a majority of MOOG’s parts, alongside other product innovations that improve durability and comfort: zinc coating and a new variety of synthetic grease. MOOG’s ball joints and link stabilisers now feature a zinc coating, making them exceptionally corrosion resistant and further improving durability. Simultaneously, a zinc-flake coating is now applied to all MOOG’s accessories, helping to increase resistance to corrosive road conditions. Additionally, the engineers at MOOG have selected a new synthetic grease that enables extremely smooth actuation while also providing workshops with increased ease of installation.
“If reliable parts are fitted to a customer’s vehicle, it is beneficial for the technician’s reputation and provides the customer with a level of reassurance, especially considering the three-year guarantee on all MOOG parts,” continued Milani. “Workshop personnel can also benefit from the recent launch of Garage Gurus, a technical training and support platform that has been designed to keep techs informed and at the top of their game.”
While the brand’s products have been available in Europe since 2001, it has recently announced the opening of a factory in Barcelona, Spain that will produce a majority of MOOG’s parts. All these components will feature the new technologies, intended to set it apart as a steering and suspension brand with an emphasis on quality and design. The new factory will also result in improved part availability throughout Europe.
The history of MOOG is not just restricted to the road: the brand’s parts have also found their way to the racetrack. MOOG has been involved with NASCAR® for over 50 years, starting all the way back in 1966. In 2017 however, MOOG also started sponsoring the NASCAR Whelen Euro SeriesTM by providing competition cars with steering and suspension components.
“While the road can be tough – especially in the UK winter – nothing comes close to the conditions our parts experience on the racetrack,” concluded Milani. “Our involvement with NASCAR is a testament to the engineering design and manufacture of MOOG products. For me, the real significance is that our components are being showcased to the world – you need to have a lot of confidence in your parts to exhibit them wheel-to-wheel at 150 miles per hour.”
If you would like to learn more about our MOOG products, visit www.MOOGparts.eu .
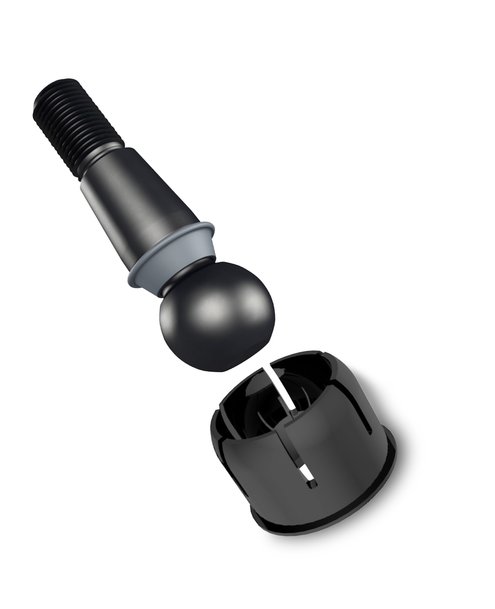
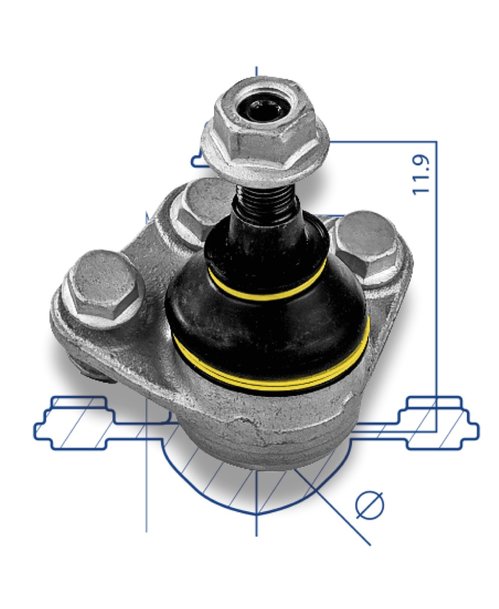
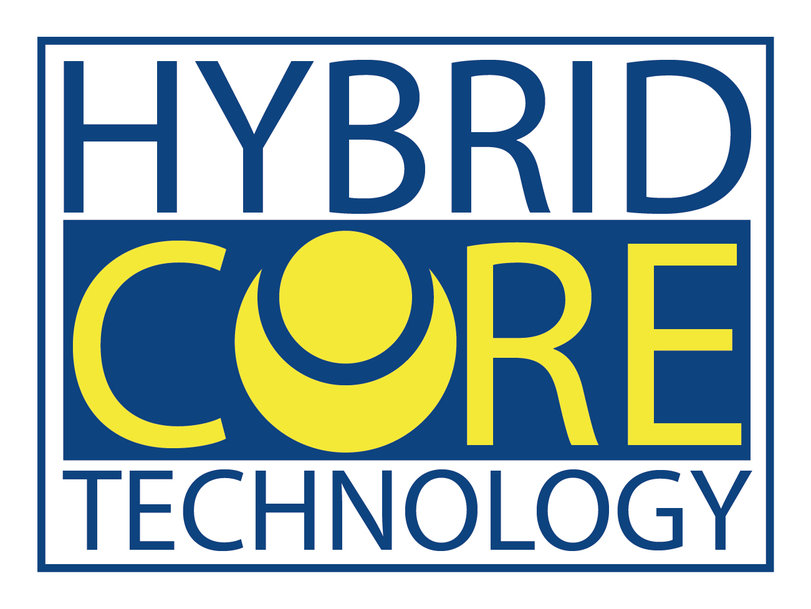
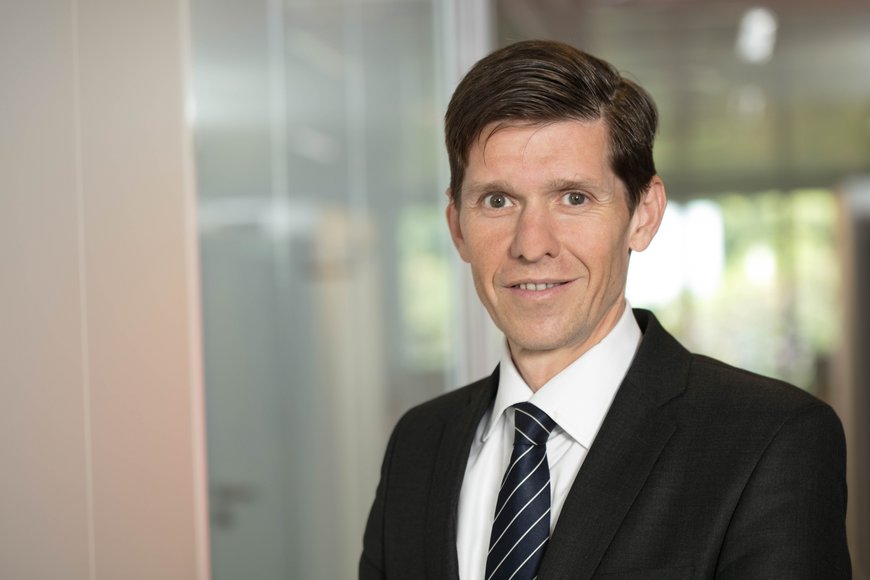