www.industryemea.com
05
'10
Written on Modified on
HYPERTURN 95/110 – opening up a new dimension in highly productive, complete machining
Two models have been added to the successful HYPERTURN series, the HYPERTURN 95 and 110, expanding our product range in complex, complete machining with high levels of productivity. The machine is a modular sytem giving our customers a choice of two bed lengths, two spindle sizes, with a milling spindle and a B-axis or with two turrets. A new state-of-the-art control and drive technology make for greater user-friendliness and increased productivity.
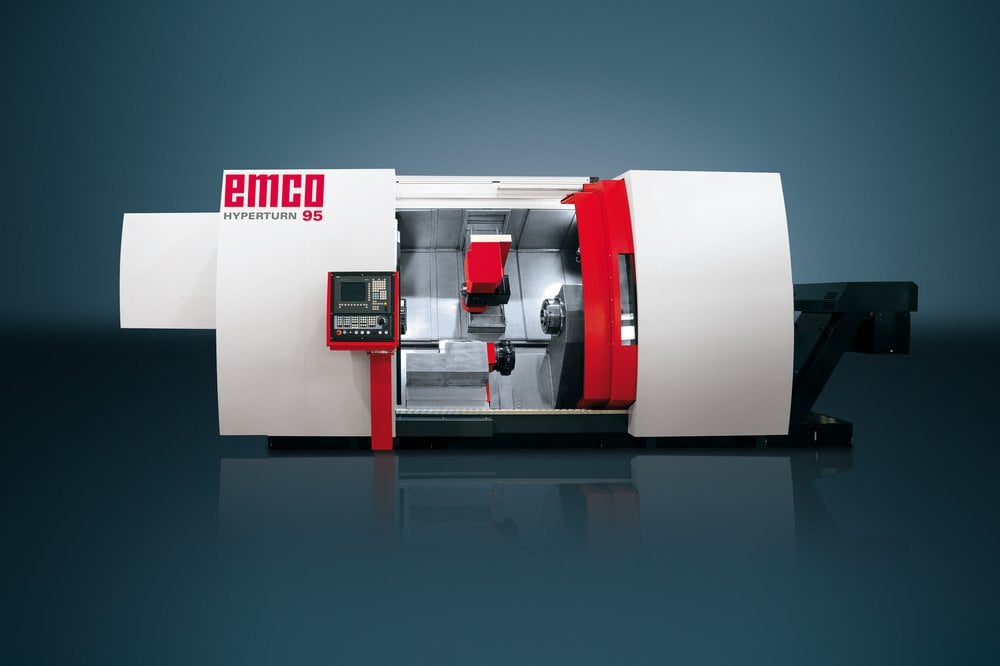
The HYPERTURN series was designed to achieve further increases in productivity in mass production. Thanks to its many different designs, the HYPERTURN 95/110 can manage any machining task, whether it be rod, shaft, flange or cubic parts.
This machine is especially of interest for the automotive and energy industry, as well as aviation,
Complex and time-consuming milling, drilling, and even gear-cutting operations can be carried out in a single work process. No reclamping or interim storage is required. The workpiece precision is vastly improved. HYPERTURN can also drastically reduce total process times, set up and labor costs, and space requirements.
The EMCO typical modular structure and comprehensive range of components, make it possible to adapt the HYPERTURN 95/110 to customer requirements. In addition, the B axis-option (PowerMill) further increases production efficiency. In this version, the machine is equipped with a high-performance milling spindle with a hollow-shaft motor. It features standard a 40-piece tool storage magazine (80-piece available as an option) with Capto-C5 or HSK-A63 holders. This provides for a wide range of milling options which makes it especially suitable, for the complete machining of complex parts with a high milling content.
E[M]COLOGY stands for optimized utilization of all the resources in the machine cycle. The Hyperturn 95/110 is designed for optimized energy efficiency in all the relevant areas:
- Use of a drive system with regenerative capacity
- Hydraulics in periodic duty
- Energy-efficient motors for the coolant system and chip disposal
- Low-friction roller guides
- Structure and weight-optimized slide modules
- Automatic switch-off after a defined idle time
Expanding the HYPERTURN series with the optional new EMCO CPS Pilot can increase effectiveness even further during cutting. Customers can plan, program, simulate and optimize production runs on their PCs using a 3D model with this software. Multiple positive effects can be achieved through the perfect interaction between the HYPERTURN 95/110 and the new EMCO CPS Pilot – resulting in further cost and time savings.
Technical details / machine design of the HYPERTURN 95/110:
FEM-optimized machine construction for more precise results:
The machine base forms the core of the machine. The compact, rigid construction in the monoblock design absorbs vibrations which may arise during machining, facilitating precision work on the workpiece. There are two base lengths available: the 1700 with a maximum turning length of 1300mm and the 2300 with a turning length of 1900mm. This means that there is nothing else standing in the way of cost-efficient, collision-free machining of a wide range of flange and shaft parts.
Main and counter spindle: for complete machining
The HYPERTURN 95/110 has two spindle solutions, depending on the range of parts which the customer manufactures. The HYPERTURN 95 is designed with two water-cooled spindle motors with an output of 33 kW and a top speed of 3500 rpm. High dynamics and optimum torque curves guarantee great cost-efficiency in the machining of shafts and the cutting of compact flange workpieces. With a two-step gearbox and an A2-11 spindle nose, the HYPERTURN 110 offers optimum requirements for the heavy roughing of large flange and shaft parts. A maximum torque of 2480 Nm permits large infeed depths in the case of large feedrates without restriction. A spindle with an A2-11 chuck nose is also used on the counter spindle. The maximum output is 42 kW, and its boasts a torque in excess of 1000 Nm.
Guide systems and drive technology: for greater stability and precision
All guide levels are implemented with largely dimensioned, preclamped linear guides. Rolling bodies instead of balls also increase stability and damping. At the same time, they are less sensitive if the machine crashes. Minimal need for lubricant also increases the useful life of the cooling emulsion in the machine considerably. Thanks to the unique sealing system on the guide shoe, the system is suitable for use in extremely dirty environments. Spring steel cover strips are also clipped onto the guide rails to create a closed sealing surface.
C-axis: for accurate contour milling and milling-turning work
The implementation of the C-axis is dependent on the spindle variant. In the case of the motor spindle, the integrated synchronous motor positions the C-axis appropriately with high precision and a high degree of rigidity. A considerable holding or turning torque of 800 Nm can be achieved here. In the case of an A2-11 size spindle, the positioning of the C-axis is implemented via an additional, swing-in drive. The spindle and workpiece are held or brought into position at up to 2000 Nm. The resolution of the circular axis is 0.001°. This makes it simple to create complex contours on the perimeter or also on the face. The software for programming these movements (cylinder interpolation or transmit) is contained in the scope of delivery.
Y-axis with a large stroke
The Y-axis has been integrated into the machine construction for optimum stability. The direct admission of force creates enormous stability and forms the basis for long tool lives and cost-efficient production. This means that complex milling operations can be performed with a large traversing range of +/- 120mm.
B-axis with a "PowerMill" spindle for maximum flexibility
The "PowerMill" B-axis version includes a high-performance milling spindle with a 40 or 80-tool magazine. The milling spindle is a water-cooled motor spindle with a 22 kW drive output and a maximum speed of 7000 rpm. Either CAPTO® C5 or HSK-A63 tools can be used, depending on the design. Used in conjunction with the 12-piece tool revolver below, complex rotary milling parts can be manufactured with a high degree of precision.
Tailstock for the complete machining of shafts
The tailstock version of the HYPERTURN is particularly suitable for machining shaft parts in large series, as well as for manufacturing particularly complex workpieces in small series. The tailstock is completely NC controlled and can be positioned using a circulating ball spindle. This also enables interpolation with other axes, reducing the machining time.
Tool turret with a VDI quick-change system
The simplest design of the HYPERTURN 95/110 contains two turrets each can take twelve VDI40 tool holders, and all the stations can be powered. Fitted with a VDI quick-change system and an EMCO alignment plate, there is no need for the time-consuming task of aligning the axially set tools. Short tool change times accelerate the processes. All the tool holders are fitted with an internal coolant supply, increasing tool life and improving chip removal.
The simplest design of the HYPERTURN 95/110 contains two turrets each can take twelve VDI40 tool holders, and all the stations can be powered. Fitted with a VDI quick-change system and an EMCO alignment plate, there is no need for the time-consuming task of aligning the axially set tools. Short tool change times accelerate the processes. All the tool holders are fitted with an internal coolant supply, increasing tool life and improving chip removal.
Generous work area for optimum ergonomics
The work area provides the highest level of ergonomics, meaning excellent accessibility to the individual components. Generous amounts of free space ensure optimal chip flow, even when machining complex materials. All guides are covered in stainless steel sheets to prevent damage.
New design of machine housing
The machine housing on the HYPERTURN 95/110 offers comprehensive protection against the discharge of chips and coolant. A large safety glass window in the door provides a clear view of the work area while built-in buttons make the machine easier to operate.
State-of-the-art Siemens Sinumerik 840 D-sl controller
This high-performance turning and milling center is controlled via the Sinumerik 840D-sl with a state-of-the-art "OPERATE®" user interface. Through the continuous further development of the user interface, countless improvements have now been incorporated making the machine considerably easier to operate and program. Some of them are listed here: USB port for data transmission, clear and intuitive controls, animated input aids, extensive technology cycles, high-performance 3D simulation, Ethernet as standard, etc. It also features the latest generation of SINAMICS® drive and servo control from Siemens. Greater dynamics with high energy efficiency, increased stability, reduced installation dimensions, etc.
The sliding control unit which is attached to the underside of the machine makes for outstanding ergonomics. The perfectly inclined 15" TFT screen contains brilliantly sharp information at the very point where the operator controls the machine.
This high-performance turning and milling center is controlled via the Sinumerik 840D-sl with a state-of-the-art "OPERATE®" user interface. Through the continuous further development of the user interface, countless improvements have now been incorporated making the machine considerably easier to operate and program. Some of them are listed here: USB port for data transmission, clear and intuitive controls, animated input aids, extensive technology cycles, high-performance 3D simulation, Ethernet as standard, etc. It also features the latest generation of SINAMICS® drive and servo control from Siemens. Greater dynamics with high energy efficiency, increased stability, reduced installation dimensions, etc.
The sliding control unit which is attached to the underside of the machine makes for outstanding ergonomics. The perfectly inclined 15" TFT screen contains brilliantly sharp information at the very point where the operator controls the machine.
Key technical data:
HYPERTURN 95
Max. bar capacity [mm] : Diameter 95 Diameter 110
Max. speed [rpm]
Main spindle : 3500
Counter spindle : 3500
Driven tools : 3000
Milling spindle : 7000
Max. drive power [kW]
Main spindle / Counter spindle: 33 / 33
Driven tools: 10,5
Milling spindle: 22
Max. turning length [mm]: 1300 (1900)
Rapid traverse speed [m/min]: 30
Number of tool adapters: 2 x 12 VDI40
Number of positions driven to on the revolver: 2 x 12
Number of tools in the magazine: 40 (80)
HYPERTURN 95
Max. bar capacity [mm] : Diameter 95 Diameter 110
Max. speed [rpm]
Main spindle : 3500
Counter spindle : 3500
Driven tools : 3000
Milling spindle : 7000
Max. drive power [kW]
Main spindle / Counter spindle: 33 / 33
Driven tools: 10,5
Milling spindle: 22
Max. turning length [mm]: 1300 (1900)
Rapid traverse speed [m/min]: 30
Number of tool adapters: 2 x 12 VDI40
Number of positions driven to on the revolver: 2 x 12
Number of tools in the magazine: 40 (80)
HYPERTURN 110
Max. bar capacity [mm] : Diameter 110
Max. bar capacity [mm] : Diameter 110
Max. speed [rpm]
Main spindle: 2500
Counter spindle: 2500
Driven tools: 3000
Milling spindle: 7000
Main spindle: 2500
Counter spindle: 2500
Driven tools: 3000
Milling spindle: 7000
Max. drive power [kW]
Main spindle / Counter spindle: 52 / 42
Driven tools: 10,5
Milling spindle: 22
Max. turning length [mm]: 1300 (1900)
Rapid traverse speed [m/min]: 30
Number of tool adapters: 2 x 12 VDI40
Number of positions driven to on the revolver: 2 x 12
Number of tools in the magazine: 40 (80)
Main spindle / Counter spindle: 52 / 42
Driven tools: 10,5
Milling spindle: 22
Max. turning length [mm]: 1300 (1900)
Rapid traverse speed [m/min]: 30
Number of tool adapters: 2 x 12 VDI40
Number of positions driven to on the revolver: 2 x 12
Number of tools in the magazine: 40 (80)