www.industryemea.com
25
'19
Written on Modified on
Advanced solutions for eliminating residual stresses in the manufacture of metal sheets
The technology centre IK4-IDEKO has taken part in the RELASHET project, which focuses on the control of stresses that are generated during the manufacturing processes of metal alloys.
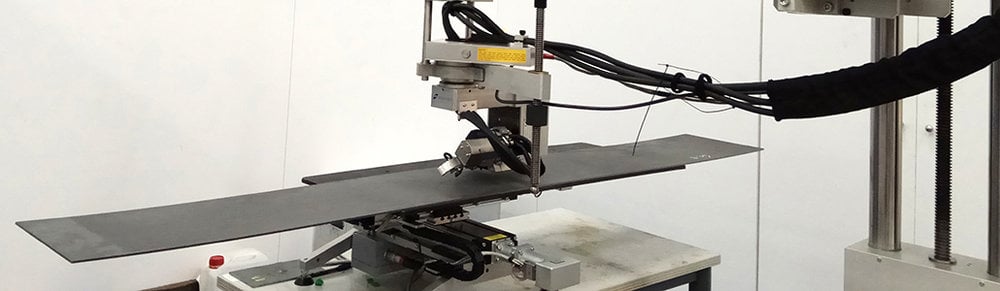
Economically strategic industrial sectors such as the automotive, aeronautics and power generation industries are addressing the challenge of obtaining lighter materials to reduce costs and increase efficiency. To achieve this, currently work is being carried out on the development of new metal sheet alloys with improved properties that reduce the weight of the structures.
However, during the manufacturing process of these new metal alloys internal stresses are generated that cause defects in the final parts and prevent the manufacturers meeting the requested requirements.
With the aim of responding to this problem, the IK4-IDEKO technology centre has taken part in the RELASHET project. This initiative is aimed at improving the operation of current sheet processing lines through the introduction of innovative systems that eliminate residual stresses generated during the manufacturing process of the materials.
The project, led by the research body Koniker, has had the support of the Basque Government through the Elkartek programme and seeks to strengthen the competitiveness of companies through the transfer of advanced technologies to industry.
"All metal alloys in the form of sheet are obtained from ingots, billets or continuous casting processes and subsequent hot and cold rolling. However, both in the rolling process and during the rolling into coils, stresses are generated inside the sheet which give rise to defects in form", said the person responsible for the research at the IK4-IDEKO technology centre, Sonia Moralejo.
The release of these internal stresses prevents part manufacturers satisfying the required tolerance ranges, in a context in which greater precision in assembled components and improved final flatness qualities of the sheets are being demanded.
"The tolerances required by sheet forming companies are increasingly demanding and the steel producers are not capable of satisfying these demands. This is especially critical in the new material alloys that have high strength and stress relief is more difficult due to the high influence of spring-back, the elastic recovery phenomenon that appears after removing a workpiece from the die", added the expert.
The RELASHET project, completed in December 2018, analysed the residual stress phenomenon, proposed new methods for its elimination transferable to the market and analysed their viability for introduction into real sheet processing lines.
Those responsible for the project have developed various sheet stress relief processes on hot rolled steels. "These processes have been analysed experimentally and by means of numerical simulation, which allows a scientific-technological comparison to be made of the various solutions and thus study the possibilities for implementing them in industry", added Sonia Moralejo.
Specifically, X-ray diffraction analysis has been carried out on sheets subjected to temper milling, shotblasting and thermal levelling, both on the surface and in depth. The study results show that compressive stresses are obtained during shotblasting and tensile stresses during temper milling, while for levelling the stresses are around zero.
"The proposed approach in this project has advantages such as extreme flatness quality and stress relief after forming operations, such as laser cutting; preventing more costly levelling processes, such as the stretch leveller or the tension leveller; reducing rejection of material that is not considered suitable for the demanded flatness tolerances and improving the properties of the materials", concluded researcher Sonia Moralejo.
In this initiative, IK4-IDEKO has been able to apply its skills to the elimination of residual stresses and deepen its knowledge on the influence of this initial stress state on the geometrical distortion of the sheet during the cutting process.
www.ideko.com