www.industryemea.com
29
'19
Written on Modified on
Reduced set-up time and increased productivity with ArcWorld
After exploring the options of robotics welding systems Sparta Ltd, one of UK's leading sub-contract engineering companies, settled for the compact and self-contained ArcWorld CS robot cell from YASKAWA.
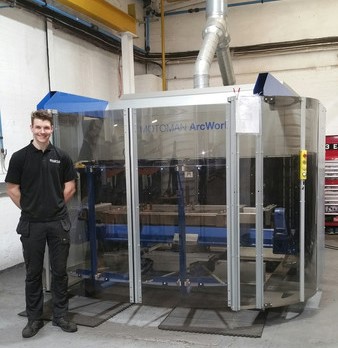
Exploring the options
Due to the increasing workload on their welding department Sparta decided to explore the benefits of robotic welding systems and how these could help them moving forward. Following extensive research into what robotic systems were available and how these could best match their needs, it was clear to Sparta that the most suitable offering was the Motoman ArcWorld CS. Based on the Motoman MA series, this 6-axis robot is designed specifically to meet the exacting demands of welding applications.
With its superior wire feed system, internally routed cables and working envelopes ranging from 1,440mm to 2,010mm, the MA-Series robot significantly improves welding quality.
Sparta felt that the ArcWorld CS provided them with the distinct advantage of a very compact, self-contained system which would best meet their welding requirements.
- It was like buying any machine tool, you pick the size of machine you need, the location to place it and away you go, Steve Davenport, Managing Director commented.
Reaping the benefits
This was the first of two Motoman robot welding cells subsequently delivered to Sparta and they are now reaping the benefits.
- The first machine had a pair of dowelled tables added to it to allow for quick set-up and changes of jigs which has now reduced set-up time to as little as 30 minutes, floor-to-floor time. Production is now on average over 300% quicker than conventional (manual) welding, Steve added.
Investing in the second Motoman machine was an easier decision as a result of Sparta realising the benefits of the first installation.
Steve confirmed:
- So much production work has been absorbed into the initial Motoman system that the second purchase is giving us a production capacity equivalent to 6 welders. This is all with the ability to never miss a weld, produce the same quality of weld at the end of the shift, as at the start, also the reduced spatter meant improved capacity for fettling. We are delighted with our decision to invest in robotic welding and we are looking forward to purchasing another Yaskawa Motoman unit later this year.
The ArcWorld robotic welding systems from Yaskawa are pre-engineered, pre-assembled and shipped ready to weld, delivering the most flexible and cost-effective options to integrate robotics into welding processes. ArcWorlds can be configured with multiple robots, a heavy-duty positioner or servo-controlled external axes for coordinated motion control.
www.yaskawa.co.uk