www.industryemea.com
15
'19
Written on Modified on
WBH10C, WBH10 and WBH20 CBN cutting tool materials
Walter is tackling a heated issue with its new CBN cutting tool materials, WBH10C, WBH10 and WBH20: Hard machining.
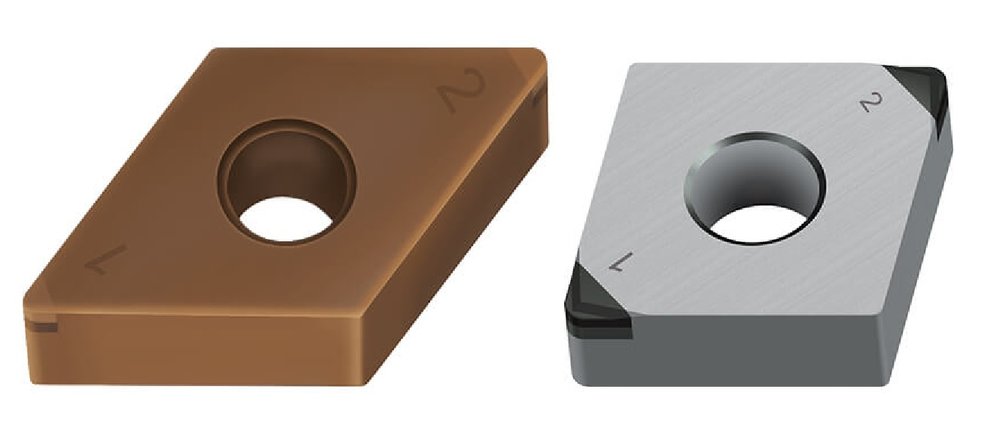
The distinguishing features of these cutting tool materials, which have been developed specifically for turning hardened steels (ISO H), are surface quality, long tool life and process reliability.
Cutting edges with the new MW wiper geometry improve the quality of machined surfaces. This is because the "M" chip formation guarantees controlled chip removal during hard/soft machining. With fine surface structure, excellent coating adhesion, high thermal stability and resistance to oxidisation, the TiAlSiN coating technology ensures up to 100 per cent longer tool life.
State-of-the-art engineering and a homogeneous production quality ensure a high level of process reliability. Walter is bringing out the CBN grades in three variants: WBH10C is wear-resistant at high vc, ensuring maximum productivity. WBH10 is the uncoated, more efficient alternative. WBH20 was developed to enable components to be manufactured efficiently and with low wear with a continuous or slightly interrupted cut.
The focus throughout is on users with hard ISO H materials up to 65 HRC, primarily those from the automotive industry. A fourth grade, the WBS10, completes the Walter CBN range in the aerospace field. Among other things, it is used for finishing Inconel 718 DA with vc up to 250 m/min.
www.walter-tools.com