www.industryemea.com
15
'19
Written on Modified on
Okuma Makes Way for Digitalisation and Automation
EMO HANNOVER 2019.
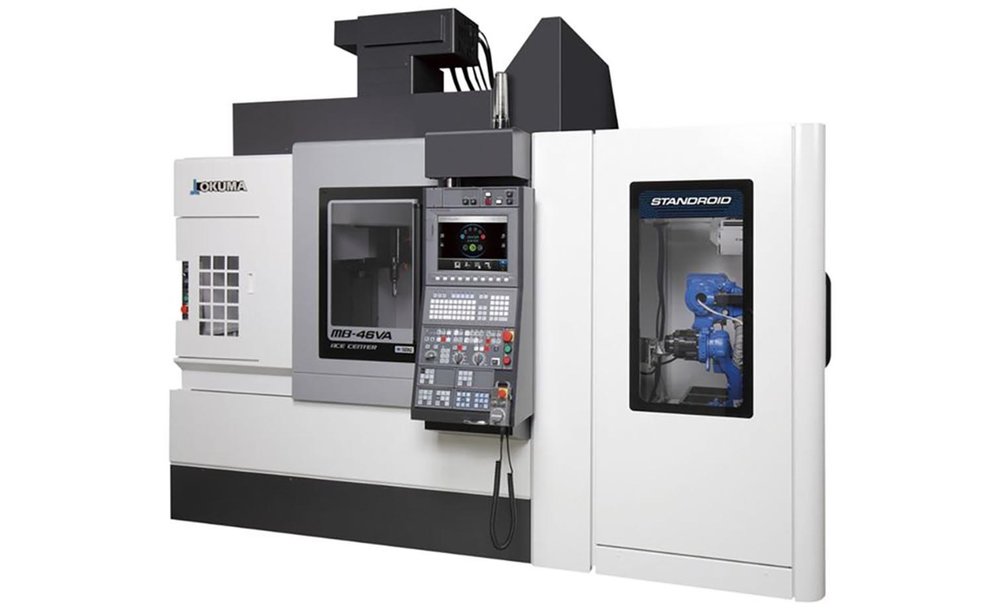
Smart Factory know-how expanded
With a third IoT-based “Dream Site” factory put into service, Okuma further expands its Smart Factory know-how. The Okuma concept for IoT relies on the latest technological developments and combines big data, artificial intelligence and intelligent production processes. This is true for the controls, Smart Factory technologies and automation solutions. Okuma presents all these new developments at this year’s EMO Hannover.
Digitalisation from the start
For Okuma, digitalisation starts long before the actual machining takes place. The Okuma technology 3D Virtual Monitor, allows manufacturers to simulate and test the entire machining process in advance. For a highly accurate simulation of the machine, 3D Virtual Monitor relies directly on the construction data. This avoids, programming errors and setup times are significantly shortened. Additional benefits are safe parting-off operations and reliable handovers of the workpiece.
Comprehensive connectivity made easy
The Okuma software Connect Plan offers valuable real-time updates of all machines in the manufacturing process regardless of where they are located. This real-time information can be used to analyse and optimise the utilisation of the entire plant. Even machine tools by third-party providers can be integrated into this system.
For traceability, Connect Plan connects each individual identifier with the manufacturing data and the measuring results of every machine involved. If problems occur, they can easily be identified and solved allowing the production to continue with higher quality and more safety than before.
The process data can also be used for Predictive Maintenance in order to plan and predict maintenance intervals. In the EMO booth, Okuma will connect all machine tools via Connect Plan, so that visitors can experience first-hand the potentials of data-driven plant optimisation.
Intelligent control enables digitalisation
The cornerstone of digitalisation is Okuma's intelligent control, which Okuma develops and manufactures itself as the industry’s only single-source supplier. The advanced OSP-P300A control is perfectly tailored to the CNC machines and a shared database ensures a boost in efficiency.
Data that is input in one area of the control can be shared automatically. This enables users to avoid unnecessary inputs and set-up times are shortened. Thanks to the open Windows architecture of the control, all Okuma machines can be easily integrated into existing manufacturing environments.
The key to fully automated manufacturing
Complex factory automation relies on state-of-the-art robotics. But automation is gaining importance also for small and medium-sized enterprises. Okuma offers efficient automation solutions for various needs. At this year’s EMO Hannover, two new automation technologies will be presented that are superior to conventional robots in many ways.
ARMROID is a robotic arm integrated into the machine tool. This opens entirely new possibilities for the machining process and makes automation available to small enterprises. Okuma continues this path with STANDROID offering a robotic arm integrated into its own separate cell. With these solutions, Okuma makes automation accessible for businesses of various sizes.
www.okuma.com