www.industryemea.com
25
'19
Written on Modified on
Autonomous gripping
Industrial gripping is about to undergo a fundamental upheaval. Whereas until now the pickup and depositing positions of workpieces, their geometry and the relevant gripping parameters always needed to be defined manually, in future gripping systems will handle the widest variety of gripping tasks of their own accord.
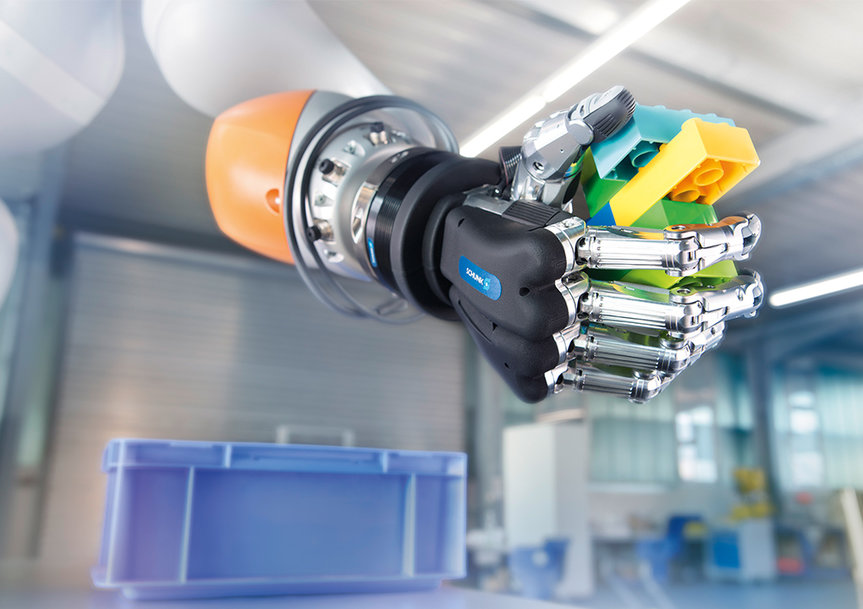
Gripping system specialists at SCHUNK are demonstrating the first solutions. Plug & Work will be a key feature in the smart factories of tomorrow. What has already been realized successfully with the mechanics, will in future to be made possible for gripper process control. Logically from a gripping point of view, the specialists at the SCHUNK Smart Labs are developing approaches as to how robots and other handling systems can carry out gripping tasks autonomously or semi-autonomously.
Instead of individually defining positions, speeds, and gripping forces step-by-step, intelligent gripping systems will in future detect their target objects via cameras and perform gripping planning of their own accord. Based on data records and algorithms, gripping systems are to be capable of detecting principles and deriving corresponding reactions. In addition, SCHUNK R&D is working on algorithms for classifying different geometries and arrangements and developing optimum gripping strategies. The vision is a learning component assembly based on a 3-layer architecture comprising motion controller, grasp controller and services. The plan is that, despite having a complex internal structure, the assembly will enable the greatest possible user friendliness on the outside.
Grippers perform gripping and lane planning
SCHUNK has shown how this can be successful based on various pilot applications from its technology factory. In a Smart Gripping application, for example, different components are distinguished by the gripper alone. Like a groping hand, the gripper will sense the geometry and composition of parts in order to grasp and categorize them. In a second application, parts arranged at random are identified via a camera, gripped autonomously out of a transport crate and guided into a machining process.
The system relays information gleaned on the part to subsequent stations so that, for example, an intelligent clamping force block is capable of coordinating its stroke and gripping force automatically to the next part. In future, according to SCHUNK, grippers will not only grip but also handle all gripping planning in interaction with 2D and 3D cameras, as well as communication with upstream and downstream components.
Learned empirical data as the basis
In another use case that makes use of machine learning approaches for workpiece and gripping process classification, interlocking building blocks are randomly combined and presented to a lightweight robot in a random arrangement on a work surface.
The robot's task is to pick up and transport the blocks away. After just a few training attempts, the system can classify how to handle the range of workpieces and the resultant combination options. The gripper knows how to pick up and transport the workpiece for handling optimally based on empirical values it has learned. In doing so the camera that captures the scenario interacts directly with the gripper and guides the robot to its destination. After a just a few repetitions the system is capable of classifying future combinations and arrangements of its own accord and acting autonomously.
www.schunk.com