www.industryemea.com
22
'12
Written on Modified on
Change your drive systems!
The water treatment and distribution company, SEMEA, has achieved a return on its investment over 14 months by replacing a pumping installation with a solution developed by LEROY-SOMER and FLOWSERVE. Characterized by low rate variations, this application, initially at fixed speed, had little potential to achieve energy savings. As such, it is a good example that in many cases, changing a drive mechanism can yield economic benefits.
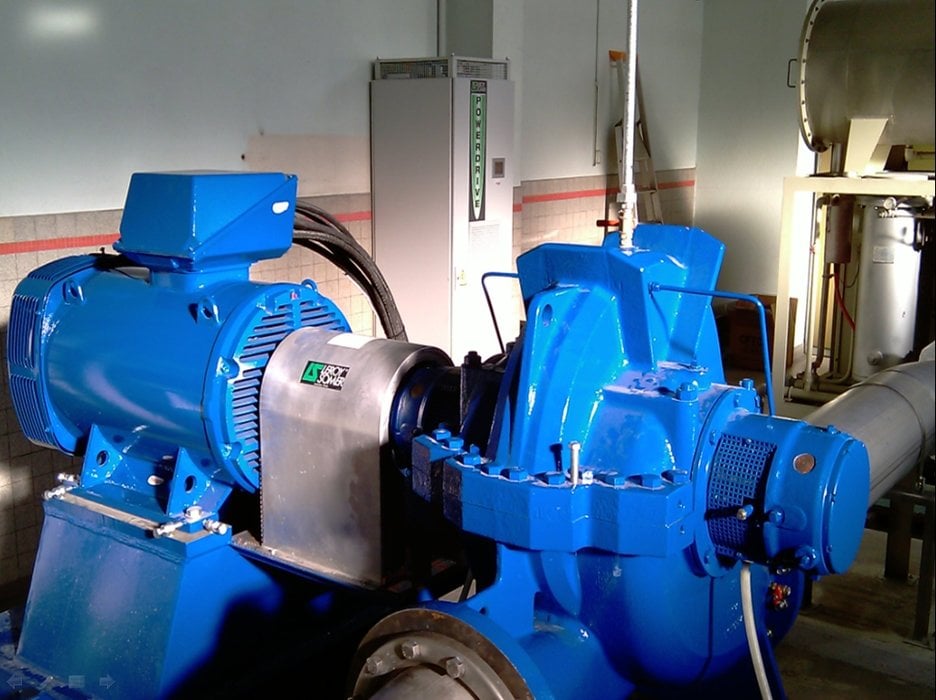
SEMEA employs 45 people and manages the treatment and the distribution of water over the greater Angouleme conurbation (16 municipalities - 110.000 inhabitants). The company wanted to replace a system made up of two motors and a pump which was used for supplying the water tower at Ruelle on Touvre (4000 m3). For that purpose it turned to Leroy-Somer and to pump manufacturer FLOWSERVE who suggested looking into an energy-efficient solution.
Didier HEISSAT, Sales Manager for FLOWSERVE in Nantes explains “With LEROY-SOMER we first carried out an analysis. We wanted to make sure that we could optimize the hydraulic result according to the pump characteristic. Each hydraulic installation works differently depending on the unit composed of the pump, the valves, and the pressure losses in the pipes. To be able to improve the energy efficiency, you need a pump characteristic curve which is not too flat. For SEMEA, we had a real potential, even if, at the beginning, it did not appear very high. According to these results, we decided to integrate a new and more efficient pump. We selected a 300LNN600 model which is part of our eco design approach and uses split case technology. It has a capacity of 500 to 1100 m3/h. We also defined the best motor speed according to the pump capacity and the network”.
“For its part, LEROY-SOMER replaced the two motors by a single permanent magnet synchronous motor PLSRPM 315 with a power rating of 350 KW and 1500 rpm speed. We also decided to control it with an inverter POWERDRIVE MDS 470T to best manage the variable flow rates, even if, in the case of SEMEA, flow rate is most often stable. This configuration is the result of the analyses and simulations we carried out. In parallel, complete tests were carried out with FLOWSERVE to define the best pump efficiency point”, explains Pierre-Emmanuel Sarre, President of the Drive Systems Division.
With the results presented, SEMEA chose this drive mechanism solution: “We could have simply replaced components reaching the end of their life cycle. For environmental and economic reasons, we preferred to consider a more optimized solution, even if it involved more time to establish the best option. Power consumption is reduced by 10% per cubic metre transferred. Moreover the pump provides a higher water flow of 15%, which enables us to better benefit from the 8 hour “night rate”. We gain 2 hours with the “daytime rate”. On the whole, the overall cost related to variable speed will be amortised in 14 months. I consider it a success and it leads us to consider the same approach for other machines in the company”, notes Michel LABET, Production Manager at SEMEA.
Optimizing power consumption is a priority for LEROY-SOMER. Pierre-Emmanuel Sarre explains: “The economic and environmental stakes are significant: standards compliance, reducing CO2, and of course energy optimisation. Over ten years, 95% of the total cost of a drive system is made up by its power consumption. The purchase price and maintenance cost account for only 2 and 3% respectively. Each case is particular and the potential for cost reduction is never the same. Our role is to help our customers to evaluate the possibility of return on investment. We have, in this area, a real know-how and we rely on unique software tools”.
“Our commitment in this approach is strong and in particular we created a "drive systems energy optimisation expert” mark for our Service Centre partners. They implement on site a series of measurements, undertake proposals, implement them and ensure their sustainability. We also advise on available investment aids within the energy saving program”, concludes Pierre-Emmanuel Sarre.
This service is based on the technical solutions of LEROY-SOMER, namely motors and geared motors at fixed speed and high-efficiency, as well as variable speed such as the Powerdrive which manages power ratings up to 2800 KW. This range is unique among other things by its easy programming.
“The use of variable speed makes it possible to adapt the speed of motors to the real needs of the application. It turns out most often to be the main source of reduction of energy costs as soon as the application requires flow variations”, explains Pierre-Emmanuel Sarre.
“These are the easiest cases to deal with. We cannot always count on variable speed, because it should be known that the inverter increases consumption by 3%. Nevertheless, amongst all the installations in use, I would say that in about one case in two, the changing of the drive system can provide economic benefits”, explains Didier HEISSAT.
The equipment installed by LEROY-SOMER is part of the Dyneo® range, which combines permanent magnet motor technologies with those of variable speed. These solutions, in compliance with the evolutions of the standards on “IE” efficiency requirements, reach a very high efficiency level, above IE3 and unequalled over the whole speed range. They allow extremely short returns on investment. Very compact, the Dyneo® solutions are integrated easily in all systems with motor speeds up to 5500 rpm.
Synchronous technology with permanent magnets offers advantages in terms of efficiency. Contrary to the AC induction motor rotor, the magnetic flux of the Dyneo® motor is not induced by the stator, but is directly created from a series of permanent magnets inserted on the rotor. In the case of the asynchronous motor, the number of revolutions of the rotor is lower than the frequency of the stator. With the permanent magnet motor, the magnetic flux remains synchronous with the frequency induced by the stator. Whilst the asynchronous motor rotor losses represent nearly one the third of the total losses, the rotor losses of the of the Dyneo® rotor are negligible.
“LEROY-SOMER has been developing permanent magnet motor technology for many years. Because of this we can offer today a wide range of solutions from 0.75 KW to 600 KW with motor speed from 375 to 5500 rpm”, concludes Pierre-Emmanuel Sarre.
Didier HEISSAT, Sales Manager for FLOWSERVE in Nantes explains “With LEROY-SOMER we first carried out an analysis. We wanted to make sure that we could optimize the hydraulic result according to the pump characteristic. Each hydraulic installation works differently depending on the unit composed of the pump, the valves, and the pressure losses in the pipes. To be able to improve the energy efficiency, you need a pump characteristic curve which is not too flat. For SEMEA, we had a real potential, even if, at the beginning, it did not appear very high. According to these results, we decided to integrate a new and more efficient pump. We selected a 300LNN600 model which is part of our eco design approach and uses split case technology. It has a capacity of 500 to 1100 m3/h. We also defined the best motor speed according to the pump capacity and the network”.
“For its part, LEROY-SOMER replaced the two motors by a single permanent magnet synchronous motor PLSRPM 315 with a power rating of 350 KW and 1500 rpm speed. We also decided to control it with an inverter POWERDRIVE MDS 470T to best manage the variable flow rates, even if, in the case of SEMEA, flow rate is most often stable. This configuration is the result of the analyses and simulations we carried out. In parallel, complete tests were carried out with FLOWSERVE to define the best pump efficiency point”, explains Pierre-Emmanuel Sarre, President of the Drive Systems Division.
With the results presented, SEMEA chose this drive mechanism solution: “We could have simply replaced components reaching the end of their life cycle. For environmental and economic reasons, we preferred to consider a more optimized solution, even if it involved more time to establish the best option. Power consumption is reduced by 10% per cubic metre transferred. Moreover the pump provides a higher water flow of 15%, which enables us to better benefit from the 8 hour “night rate”. We gain 2 hours with the “daytime rate”. On the whole, the overall cost related to variable speed will be amortised in 14 months. I consider it a success and it leads us to consider the same approach for other machines in the company”, notes Michel LABET, Production Manager at SEMEA.
Optimizing power consumption is a priority for LEROY-SOMER. Pierre-Emmanuel Sarre explains: “The economic and environmental stakes are significant: standards compliance, reducing CO2, and of course energy optimisation. Over ten years, 95% of the total cost of a drive system is made up by its power consumption. The purchase price and maintenance cost account for only 2 and 3% respectively. Each case is particular and the potential for cost reduction is never the same. Our role is to help our customers to evaluate the possibility of return on investment. We have, in this area, a real know-how and we rely on unique software tools”.
“Our commitment in this approach is strong and in particular we created a "drive systems energy optimisation expert” mark for our Service Centre partners. They implement on site a series of measurements, undertake proposals, implement them and ensure their sustainability. We also advise on available investment aids within the energy saving program”, concludes Pierre-Emmanuel Sarre.
This service is based on the technical solutions of LEROY-SOMER, namely motors and geared motors at fixed speed and high-efficiency, as well as variable speed such as the Powerdrive which manages power ratings up to 2800 KW. This range is unique among other things by its easy programming.
“The use of variable speed makes it possible to adapt the speed of motors to the real needs of the application. It turns out most often to be the main source of reduction of energy costs as soon as the application requires flow variations”, explains Pierre-Emmanuel Sarre.
“These are the easiest cases to deal with. We cannot always count on variable speed, because it should be known that the inverter increases consumption by 3%. Nevertheless, amongst all the installations in use, I would say that in about one case in two, the changing of the drive system can provide economic benefits”, explains Didier HEISSAT.
The equipment installed by LEROY-SOMER is part of the Dyneo® range, which combines permanent magnet motor technologies with those of variable speed. These solutions, in compliance with the evolutions of the standards on “IE” efficiency requirements, reach a very high efficiency level, above IE3 and unequalled over the whole speed range. They allow extremely short returns on investment. Very compact, the Dyneo® solutions are integrated easily in all systems with motor speeds up to 5500 rpm.
Synchronous technology with permanent magnets offers advantages in terms of efficiency. Contrary to the AC induction motor rotor, the magnetic flux of the Dyneo® motor is not induced by the stator, but is directly created from a series of permanent magnets inserted on the rotor. In the case of the asynchronous motor, the number of revolutions of the rotor is lower than the frequency of the stator. With the permanent magnet motor, the magnetic flux remains synchronous with the frequency induced by the stator. Whilst the asynchronous motor rotor losses represent nearly one the third of the total losses, the rotor losses of the of the Dyneo® rotor are negligible.
“LEROY-SOMER has been developing permanent magnet motor technology for many years. Because of this we can offer today a wide range of solutions from 0.75 KW to 600 KW with motor speed from 375 to 5500 rpm”, concludes Pierre-Emmanuel Sarre.
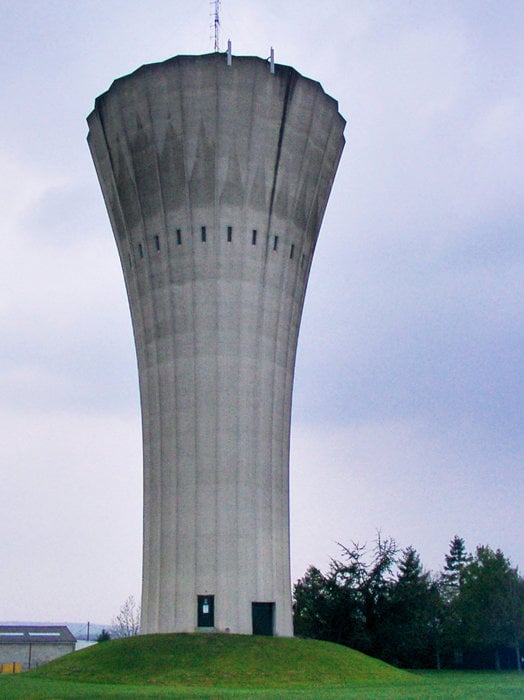
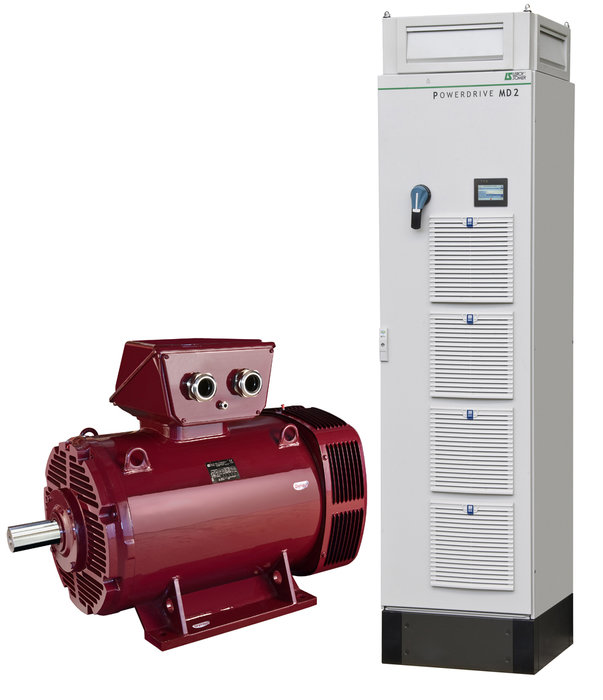