www.industryemea.com
20
'20
Written on Modified on
Tailor-made solutions made of aluminium
Interview by Stefan Holtkoetter, Corporate Communications at KTR.
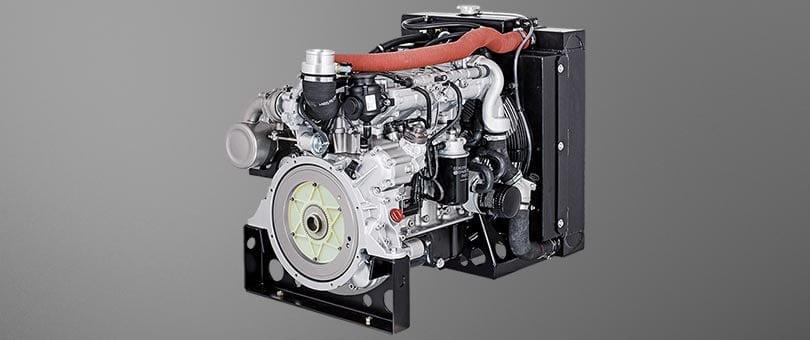
At the end of the 2000s KTR extended their cooler portfolio with multiple circuit coolers, commonly used in mobile machine applications; the new product series from KTR is called „MMC combi coolers“. In October 2018 the company reached its latest milestone by opening their new dedicated cooler manufacturing plant in China. We have discussed the new plant and KTR’s tailormade coolers with Product Manager Joachim Grunwald.
Mr. Grunwald, when did you start at KTR and what is your job?
I started working for KTR in the development and sale of oil-air coolers in November 2007. Since 2011 I have been the Product Manager for the MMC combi coolers. Before I have been working in the same position with one of the biggest manufacturers of heat exchangers for more than 13 years.
How did it come about that KTR coolers were included in the portfolio?
Since the 1970s KTR has been manufacturing accessories for the hydraulics industry. The subject of cooling has always been latently present. Finally the company started to look into the subject of leakage oil cooling of hydraulic pumps. In the late 1990s KTR added the first oil-water cooler for stationary hydraulics to their portfolio; in the mid 2000s oil-air coolers were added. Due to my experiences in the field of cooling mobile machines, we extended the portfolio by the MMC combined coolers. We have two separate sections now: My co-worker Christoph Bettmer in the Core Business Hydraulics Team is in charge of the oil-water and oil-air coolers, while I am assigned to the Engineered Business Unit with the MMC series.
What does the combination of letters MMC mean?
The acronym stands for „Multi Medium Cooler“ meaning that various media such as oil, water, fuel or air can be cooled in a cooling housing.
In which cases is a combined cooler by KTR used?
For example, consider a construction machine. It is usually directly driven by an I. C.-engine. These power packs are very sophisticated so that a cooler must be taken on board to temper the cooling water. Meanwhile many engines are charged so that charge air cooling is required, too. And if the engine drives a hydraulic unit additionally, the oil might have to be cooled as well. A combined cooler with one fan drive only, thus making up a compact solution, is most suitable for this application. This may sound simple, but it means close coordination between customer and engineering.
In what way?
Each of our MMC coolers is a customized design, developed for a special application and a special machine. Here the customer specifies the parameters: How much mounting space is available, how the fan drive is to be implemented, what cooling capacity is required, what weight the cooler may have, etc. Every application needs to be considered differently and individually. That is why project development of a combined cooler is quite a sophisticated issue.
And how do you achieve a result?
When dimensioning the cooler components we make use, among others, of the simulation software „KULI“ which allows to calculate possible solutions. Apart from that we use our in-house simulation tools we developed along with our IT specialists. Anyway, just as important is the know-how of the design engineers in charge. Finally it is our job to provide a defined cooling capacity for a defined mounting space. In this case we apply various solutions such as shape of laminas, dimensions, fan, drive, etc.
The customer cannot just select an MMC from the catalogue?
I am afraid not. In fact we have to consider the different requirements and specifications of every customer inquiry and sort out step by step. The result is always different. This is similar to a car where a different solution is realized for each model. That is why there is no catalogue of our MMC coolers showing tables and details of dimensions, types and performance data. We are currently updating the catalogue about our standard coolers, the OAC and OPC series. We take the opportunity to introduce our performance range on a few pages.
Could you please outline a current example of application?
I will do so with pleasure. The engine manufacturer Hatz supplies the new H series as an open power unit ready for mounting. Our dual-circuit cooler is used for cooling charge air and engine coolant. Apart from sufficient cooling capacity with each application, dimensions and weight were decisive factors with the project development.
Specifically in mobile applications the mounting space is quite limited – that is where every centimetre counts. Weight is a key issue as well. That is why the cooler has a high power density and the OPU’s box dimensions could be limited to 699x935x807 mm. A separate oil cooler having the dimensions of 150x150x70 mm is fitted laterally on the engine cooling the engine oil via the engine coolant. By the way, we will exhibit the engine at the forthcoming Intermat in Paris.
You mentioned further applications for your MMC coolers. What can you tell us about this subject?
As an example, from my point of view agricultural machines are similar to construction machines. This field also includes diesel engines with or without turbo loaders, hydraulic circuits and gearboxes, all of those being components which might require a multiple-circuit cooling system. Anyway, we also address manufacturers of diesel generators and compressors who have similar requirements.
Would you please tell us something about the new cooler plant of KTR in China?
The new production hall has 9,000 m² dedicated to cooler manufacturing and is in Jiaxing, approximately 100 km southwest of Shanghai. We commissioned the new plant in October 2018 and since June 2019 we have been manufacturing coolers at production levels. In the long-term around 200 tons of aluminium can be processed in the production of coolers each month at the facility.
The company has invested significantly in a state-of-the-art production facility; the result is that we are able to manufacture even small production runs on a highly automated and constantly high-quality level. I do also want to mention that with the new cooler plant we fully comply with the strict environmental regulations of the Chinese government, for example regarding wastewater and air pollution.
www.ktr.com