www.industryemea.com
05
'20
Written on Modified on
3D printing is making headway in industry
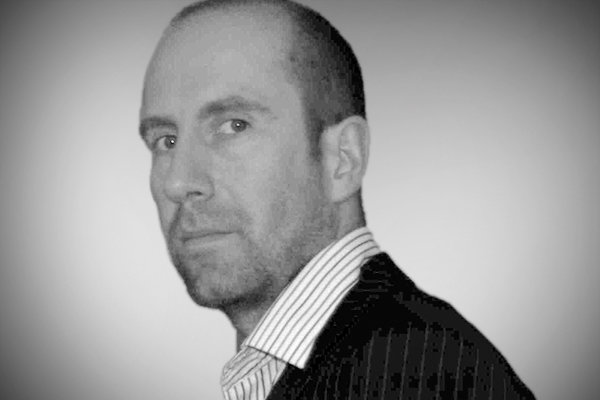
The first patent for the manufacture of 3D objects by adding successive layers was filed as early as July 16, 1984. It was a French patent. The second patent was filed on August 8, 1984. By the inventor who would soon become one of the co-founders of 3D Systems. This American company has now become the world leader. So, what happened? How come that history will tell that the French patent got forgotten?
Two things have worked in the American company’s favour. In the 80s, on the other side of Atlantic, no-one was ashamed to talk about money or raising funds to start a company (aka capitalism!). (For those who remember, creating a company in France was a real challenge at the time, a task that was both unproductive and very time-consuming). And then most importantly ("last but not least," as Charles Hull the originator of 3D Systems' patent would say), to ensure the continued protection of his patent, he made sure the maintenance fees were paid regularly. In France, someone probably found way to save a bit of money by quietly removing patent protection out of the list of "minor expenses". Fast forward... Very soon after, new patents arrived, consolidating the initial work done by 3D Systems. Fast forward again... The first 3D printers were released in the late 1980s. The company was launched. Skip to the next chapter... The 3D revolution has taken off. By adding successive layers, the technique of “additive" manufacturing was able to develop further.
10 years ago, only a few, very expensive 3D printers were capable of sufficient precision to produce industrial quality parts. At that time, they were mostly for making prototypes. Sometimes small quantities of parts were produced, but only in very small series. As well as dimensional accuracy, the 3D printers also lacked speed. Today, mastery of the technology enables very thin layers (a few tenths of a millimetre) to be produced, and the reduction in production times makes it possible to achieve industrial-level speeds.
It must be said too, that about ten years ago, the mixtures of "glues" and powders used to amalgamate the successive layers were only just beginning to diversify; now the catalogues of machine manufacturers are filled with different types of polymers and various metal powders. It should be noted in passing that we are seeing a growing number of scientific publications about 3D printing of animal and human skin to accelerate the healing of wounds. And another very important trend: it is becoming possible to build large objects (a vehicle capable of carrying a load of 250 kg, for example).
Over the past several years, all branches of industry have taken an interest in 3D printing. Mechanical engineering industries, of course, but others as well. As a result, new design and manufacturing methods using 3D printing are being discovered everywhere, in design, architecture, construction, automotive, aeronautics, railways and the whole transport sector for passengers and goods (both with driver or driverless, for long distance haulage or last mile delivery), the energy sector, electronics, the food industry etc.. This technology makes it possible to create shapes and parts that were previously impossible to make.
Make no mistake: at the heart of our workshops and factories, manufacturing techniques using subtractive machining (drilling, milling, boring, turning) and additive techniques (3D printing) are and will remain complementary. But it is clear that the latter open up new avenues for the development and manufacture of parts and systems.
And of course, if all industries can be able to benefit from this technology in future, it is also because machine prices have fallen considerably, and manufacturers are striving to develop their machine capabilities at a rapid pace. - Read more here.
••• Steed WEBZELL