3D Systems Expands Plastics Materials Portfolio to Address Broadest Set of Applications in the AM Industry
3D Systems (NYSE:DDD) today is announcing several innovations for its plastics materials portfolio designed to help manufacturers address a broader portfolio of applications.
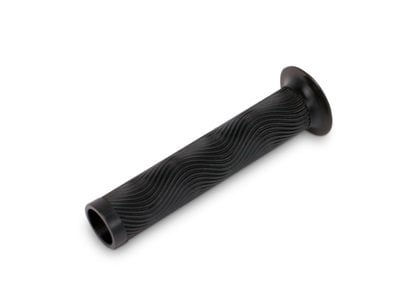
- Figure 4 RUBBER-65A BLK new mid-tear strength elastomer has high elongation at break for flexibility, strength and durability
- Accura Fidelity - ultra-low viscosity, antimony-free SLA resin – enables medium to large sized, light weight, and easy to handle casting patterns - leading to an increase in casting yields
- Introduction of Figure 4 JEWEL MASTER GRY opens new jewelry workflows
These materials – Figure 4 RUBBER-65A BLK, Accura Fidelity, Accura Bond, Accura Patch, and Figure 4 JEWEL MASTER GRY – are designed for the company’s Figure 4 and Stereolithography (SLA) printing technologies. With the expansion of its renowned materials portfolio, 3D Systems continues to open new production applications.
“Our team has continued developing new materials across our plastics portfolio to address a broader set of production applications and providing data sheets with key test results and performance specs to make it easy for our customers to make the optimal material choice for their needs,” said Menno Ellis, SVP and general manager, plastics, 3D Systems. “Our material scientists and technical experts have leveraged decades of experience to engineer these high performing materials to deliver accurate, economical, and repeatable results to enable our customers to maintain competitive advantage.”
Figure 4 RUBBER-65A BLK – A Production-Grade Rubber Suitable for Multiple Industrial Applications
Building on its portfolio of production-grade materials, 3D Systems is introducing Figure 4 RUBBER-65A BLK. This mid-tear strength elastomer has high elongation at break for flexibility and durability, is engineered for long-term environmental stability, and is tested per UL94 standards. These properties enable production of end-use elastomeric parts with a high degree of accuracy and minimal scarring from supports, which makes it ideal for applications such as air/dust gaskets, seals for electronics, vibration dampeners and pipe spacers. Figure 4 RUBBER-65A BLK is biocompatible capable per ISO 10993-5 and ISO 10993-10 so it can be used to produce grips and handles as well as padding for splints and braces. Parts produced using Figure 4 RUBBER-65A BLK and 3D Systems’ Figure 4 technology can be produced faster than other similar competitive materials that require a secondary thermal post-cure.
“As a mechanical engineer and designer of medical devices, I can think of many uses for a robust elastomeric material such as Figure 4 RUBBER-65A BLK,” said Matthew Cavuto, mechanical engineer, Imperial College London. “Custom sealing grommets, damping elements, or even soft-touch grips are just a few of the applications that come to mind – all of which would expand the capabilities and streamline my process of prototyping on the Figure 4. Functionally, Figure 4 RUBBER-65A BLK is quite impressive. When matched with the right part and application, it has great tear strength and exceptional print quality.”
As with all of 3D Systems’ production-grade materials, Figure 4 RUBBER-65A BLK is specially formulated for additive manufacturing by addressing three key customer needs: Production Performance Properties, Production Mechanical Properties, and Production Testing Standards. This complies with the comprehensive testing standards – per ASTM and ISO - the company employed when it released data for several of its Figure 4 materials in March 2020, including Long term Indoor and Outdoor Environmental Stability, Dielectric properties, Flammability, Biocompatibility, and Chemical compatibility. General availability for this material is planned for late June 2020.
New Investment Casting Materials Strengthen First-to-Market Platform
3D Systems introduced the first 3D printed casting pattern to the market nearly 30 years ago that enables tool-less, complex geometries and design optimization not possible with traditional tooling for patterns. Since then, foundries have trusted 3D Systems’ QuickCast® process to facilitate direct production of medium to large size, high precision 3D printed investment casting patterns. Today, the company is introducing a new casting material and two new post-processing materials to enhance this trusted platform.
Accura Fidelity is an ultra-low viscosity, antimony-free stereolithography (SLA) resin with clean burnout that is designed to create patterns for a variety of castable metals, including titanium and aluminum alloys. When used as part of 3D Systems’ QuickCast process, Accura Fidelity enables rapid creation of medium to large, lightweight, and easy-to-handle casting patterns - leading to increased casting yields.
“The new Accura Fidelity material for Stereolithography printing has improved the post-processing of our QuickCast investment casting patterns,” said Nancy Holt, director of operations, 3D Systems On Demand. “The low viscosity of this material facilitates better drainage and faster cleaning of the patterns, resulting in an expected increase in throughput by up to 30% as we move into full production with this material. The ultimate test is in its castability, and our foundry customers are providing very positive feedback. One customer, SeaCast, said the QuickCast pattern with Accura Fidelity casted extremely well with their process and they were very pleased with the final metal part.”
3D Systems is also introducing a new UV curable class of post-processing materials with Accura Patch and Accura Bond. Accura Patch is a high viscosity material designed to fill QuickCast pattern drain holes during post-processing. Accura Bond is a high viscosity material created to join various printed patterns together into one large pattern. Both solutions can also be used with any of 3D Systems’ SLA resins for creating larger parts and for patching during post processing.
Accura Fidelity is currently available while general availability for Accura Bond and Accura Patch is planned for July 2020.
Figure 4 JEWEL MASTER GRY Opens New Applications
3D Systems began 2020 with the launch of Figure 4 Jewelry - a specially designed and optimized solution for the burgeoning 3D printed jewelry market. As an integrated production solution, Figure 4 Jewelry is designed to address three application-specific workflows: jewelry casting patterns, master patterns for molds, and prototype/fit check models. The solution launched with the jewelry casting workflow using Figure 4 JCAST-GRN 10 material. Today, the company is announcing Figure 4 JEWEL MASTER GRY - a versatile master pattern material for high volume jewelry silicone molds and for prototype/fit models. The material’s high heat deflection temperature ensures compatibility with a range of silicones for creating master patterns.
Figure 4 JEWEL MASTER GRY is well suited for producing high definition master patterns for making silicone or RTV molds - especially for high volume, mass production of designs. This material also delivers exceptional precise surface quality for design and functional prototyping, as well as snap-fit and stone-in-place testing. Figure 4 JEWEL MASTER GRY meets biocompatibility standard ISO 10933-5 for cytotoxicity, making it safe for try-ons and fittings. General availability is planned for late June 2020.
www.3dsystems.com