www.industryemea.com
16
'20
Written on Modified on
The hidden champion of industry: meeting sustainability targets and saving operating costs with GEA heat pump technology
There are obvious reasons for installing heat pump solutions in the industry. Some do it to reduce operating costs and thereby increase their competitiveness, others choose to do it as part of their long term sustainability targets in line with the company image and finally there are industries which have to change their heating solution away from burning fossil fuels in order to meet regulatory requirement for reducing the environmental impact we all have on our planet.
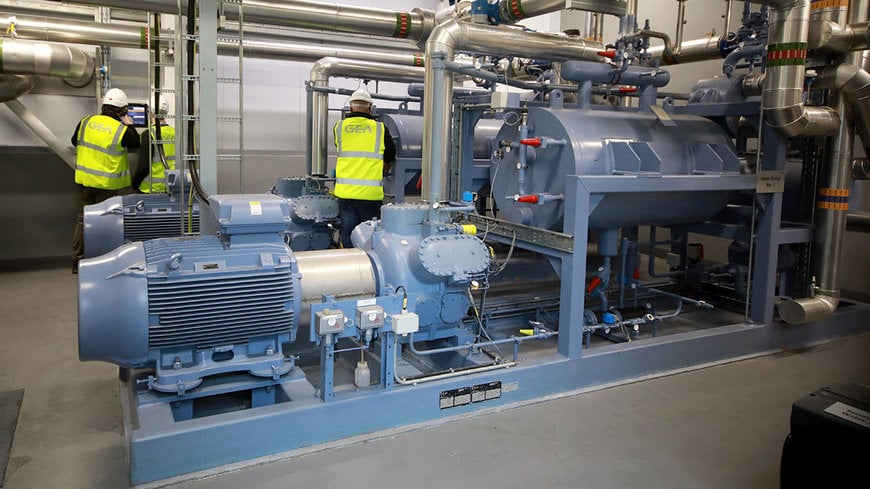
It can be just one, but mainly all of the benefits above that is the reason why heat pump solutions are installed. Whatever the reason is: energy-efficient heat pumps from GEA are rapidly becoming the technology of choice on the road to a carbon-neutral future. The high efficiency and low maintenance of GEA heat pumps give a short payback and continues to benefit the customer throughout the long lifecycle (min 20 years) of the installation. By replacing burning fossil fuels: CO2 emissions which are harmful to global climate and NOx emissions which are harmful to the local environment are avoided.
In addition, environmentally friendly natural refrigerants such as ammonia are used. The food industry in particular recognises the considerable financial and ecological advantages of using heat pumps in production processes. Most food processing is a combination of heat treatment and subsequent cold storage for long shelf life. This combination of heating and cooling maximizes the benefit of heat pump installations. GEA heat pump technology offers energy saving advantages regardless of the industry and the extent of its use. Besides applications in the processing industry, heat pumps are also often used in environmentally friendly district heating schemes, where they are being used not only to provide the base heat load, but also as adjustable heat source, their quick reaction time is a good match with large district heating networks. In these schemes they also play an important part of protecting the electrical grid as part of smart energy systems, where loads can be adjusted online according to request from the electrical supplier.
Combining climate protection with cost reduction
According to the International Energy Agency (IEA), heat accounts for more than half of the world's final energy consumption, with most of this being generated from fossil fuels. In industry and commerce, the demand for hot water and process heat is very specific. It can often be met with heat pumps. Their efficiency and short payback period make them an environmentally friendly and economically attractive alternative to conventional heating systems. A heat pump converts heat from the environment - water or process waste heat - from a low temperature level to a higher one.
The type of application is decisive when planning and selecting a heat pump system: The variety of industrial heat pumps makes them interesting for numerous applications where both heating and cooling is required. The smaller the temperature lift is for the heat pump the less electrical power is required. For heat pump installation it is important to find the highest temperature heat source and optimize the heating system for supplying the lowest practical hot water temperature. If the demand for heating and cooling changes seasonally, typically in office buildings or greenhouses, a GEA heat pump can heat in winter and cool in summer. In the seasons where both heating and cooling is required, the efficiency can be more than ten times higher than a conventional installation with boiler for heating and air conditioning for cooling.
GEA experience with cooling systems as a decisive advantage
GEA's technicians are experts in both cooling systems and heat pumps. With more than 100 years of manufacturing ammonia refrigeration and more than 10 years knowledge from high temperature heat pumps installations the reasons are obvious. Heat pumps and refrigeration systems use the same physical principle - and they all consist of the same main components, such as compressors and heat exchangers. The principle of the heat pump is also used for cooling (as with the refrigerator), while the term "heat pump" is only used for the heating unit. In the cooling process, the useful energy is the heat absorbed from the process/cold store to be cooled, which together with the drive energy is dissipated to the environment as waste heat. When a heat pump is combined with a cooling unit, both cooling and heating are possible, so that the one-time use becomes a continuous cycle, which reduces energy costs by 30 percent or more. This is a significant saving when you consider that in the food, dairy and beverage industry up to 60 percent of energy consumption can be used for heating and cooling.
The centerpieces: GEA reciprocating and screw compressors
They are the heart and therefore literally the pump of the heat pump: GEA reciprocating and screw compressors. GEA has the largest range of high-pressure ammonia screw compressors suitable for heat pump application. Through its many heat pump installations GEA has optimized the range for low vibration levels and high efficiency. With the small cylinder reciprocating V-compressor range available for higher pressures GEA is now able to offer the most efficient ammonia compressor solution on the market. These compressors are specially designed for the high final compression pressure in a heat pump. They offer condensation temperatures which, depending on the design, are just as suitable for operating low-temperature hot water as for providing process heat.
GEA relies on environmentally friendly refrigerants
As fluorinated gases are gradually being phased out Globally to reduce greenhouse gas emissions, natural refrigerants are becoming increasingly popular, especially ammonia, an environmentally friendly refrigerant and cost-effective and has no impact on global warming or causing build-up of fluoride compounds in the nature. Ammonia is widely used in food processing plants, the beverage and dairy industries, breweries and cold stores. Thanks to improvements in compressor technology, ammonia heat pumps can now produce higher temperatures. This has paved the way for their wider use in the food, beverage and dairy industries, where waste heat can be reused and enhanced for washing, cleaning and drying products, heating water for cleaning and processing purposes, and pasteurisation.
Traditionally, these industries used boilers to cook or pasteurise products, which were then cooled down again, resulting in massive waste of energy. The heat from the cooling process was too low to be reused. However, a heat pump can raise the temperature of the refrigeration plant waste heat up to 90⁰C so that it can be returned to the cycle. This means that more fossil fuel boilers can be phased out, the heat can be regenerated or recycled, and CO2 emissions are greatly reduced - in many cases by more than 50 percent. In addition, CO2 emissions can be reduced to zero if "green electricity" is used.
Customized gear unit from GEA heat pumps is a giant step forward for the food industry
"GEA's industrial heat pumps range from 300 kW to 10 MW, which means we can handle virtually any application from hot rinse water to city-wide district heating," says Kenneth Hoffmann, Product Manager Heat Pumps, GEA Refrigeration Technologies. "But every application is different and requires a tailored approach. We have the advantage of being able to combine extensive process knowledge and expertise for integrated heating and cooling solutions. We design everything so that the heat source remains stable and permanently available, so that the use of waste heat can be optimized".
Conventional systems with gas boilers are normally designed for a much higher heat transfer medium temperature than is required in the process. This allows some inaccurate heat load calculations during design and provides only a little extra energy.
A heat pump system requires a comprehensive analysis of the required temperatures and the evaluation of the correct process parameters. In a heat pump every degree counts and the more accurate the original design, the more energy can be saved. Instead of concentrating on small pipes with a large temperature difference to keep initial costs low, a heat pump investment is based on continuous savings that are made every day.
"We have had excellent relationships with processing customers for decades because of the refrigeration systems we supply. This is where our roots and expertise lie," says Maarten Gelens, refrigeration expert, GEA Refrigeration Technologies Netherlands.
Robert Unsworth, Technical Sales Director GEA Refrigeration Technologies UK, added: "Together with our customers we strive for sustainability goals: to achieve energy savings and CO2 reduction. The use of heat pumps in the food, dairy and beverage sectors will be the biggest leap forward food production and refrigeration has ever seen".
www.gea.com