www.industryemea.com
30
'20
Written on Modified on
THE ENERGY TRANSITION CAN ONLY BE ACHIEVED BY IMPROVING EFFICIENCY
How energy is generated is the subject of extensive debate. But how it is used is hardly ever discussed. Yet efficiency measures are indispensable in achieving the transition from fossil fuels to renewable energies. The German efficiency researcher Alexander Sauer knows how industry can make its contribution.
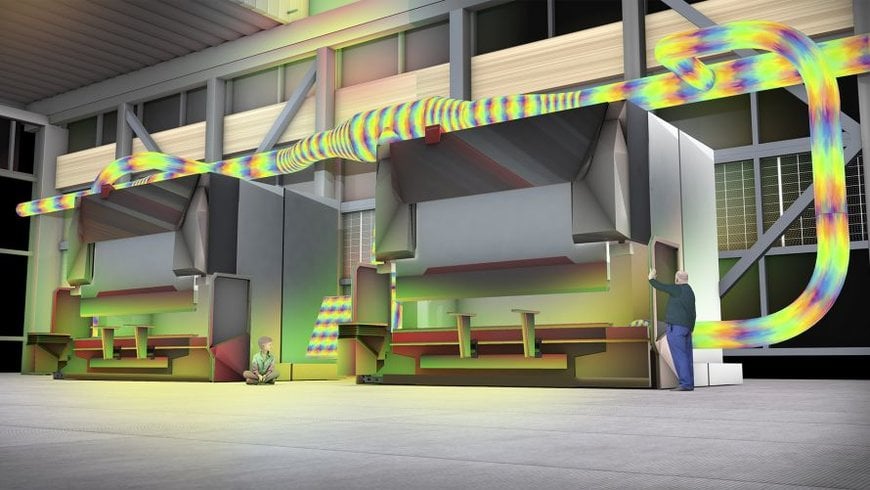
More than 75 billion US dollars. According to the International Energy Agency (IEA), this is how much is invested annually in energy efficiency in Europe alone. This is not entirely altruistic. “It is about the existential question regarding how our supply grids are to function in the future,” says Alexander Sauer, Director of the Institute of Energy Efficiency in Production at the University of Stuttgart. The transition from finite resources such as oil and coal to renewable energies, which are generally utilized in the form of electricity, is creating countless new consumers on the supply grid. In order to maintain grid stability, today’s consumers must reduce their consumption.
Industry-spanning technologies with savings potential
This means that energy efficiency is essential, and this holds especially true for the industrial sector. In Switzerland, industry consumes some 112 terawatt hours of energy a year. This means that more than one third of the total annual consumption is attributable to the secondary sector – more than to all Swiss households combined. In Germany, industry consumes a good 740 terawatt hours, and in the United States, as much as 7708 terawatt hours. Any country that is serious about the energy transition is well advised to address this sector. But how can a company tackle the task of increasing efficiency?
One thing should be stressed from the outset: Given the wide spectrum of possible approaches, there is no one-size-fits-all solution. As a rule of thumb, energy-intensive industries such as steel, chemicals, or paper production, can make the greatest impact by optimizing individual production processes and, for example, focusing on more efficient thermal processes. In the field of lightweight construction, decentralized additive manufacturing based on 3D printing is one approach towards saving transport emissions and materials.
However, the IEA estimates that around three-quarters of the energy savings that must be achieved in order to accomplish the energy transition will involve industries that are not energy-intensive and whose operations usually revolve around assembly processes. In other words, these industries must achieve the greatest savings by far. As Alexander Sauer explains, cross-sectional technologies such as supply and building technology, and not process technologies, offer the greatest savings potential in this field. In order to exploit this potential, one thing is particularly important: transparency. “This may sound trivial”, he says, “but companies are frequently surprised by how many energy flows in their factories they weren’t even aware of.” But this knowledge is crucial in order to define measures and achieve improvements.
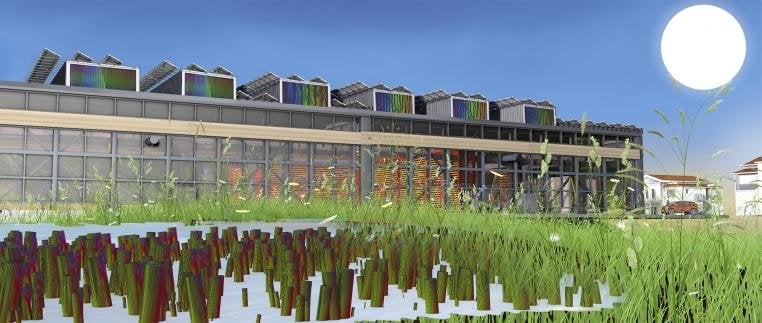
The smart factory is equipped with a photovoltaic system and produces large part of its energy requirements autonomously
Coordination is key
Based on the example of a German industrial company, Alexander Sauer explains what such measures could look like. A photovoltaic system provides the energy. To ensure that this electricity is utilized efficiently, the company uses an intelligent energy management system. “As a result, processes that tend to be energy-intensive are scheduled for execution when the forecasting tool predicts high solar radiation and thus a high electricity output.” In order to also utilize electricity production surpluses, the company produces the inert gases it requires for its core processes in-house. Inert gases such as helium, argon, or CO2 displace air and ensure, for example, that packaged food perishes less quickly or that metals do not oxidize during processing. The excess electricity is thus converted and can be stored more readily. In winter, a biogas cogeneration plant provides heating and additional electricity. The reed field, which supplies raw material to offset the biogas, is located right next to the company premises.
Coordination is key to increasing efficiency – coordination of production and consumption, but also of operational processes with each other. “This can mean, for example, that the intelligent energy management system synchronizes a process that produces waste heat with another process that can utilize this heat – for example, by using a heat exchanger to heat water for showers,” Alexander Sauer explains. “In this way, the waste heat does not have to be vented into the atmosphere while at the same time another process has to be conventionally heated using additional energy.”
Alexander Sauer also sees great energy-saving potential in the production of compressed air, which is used in industry in paintshops, for hoisting equipment, sandblasting, cleaning, cooling, and heating, to name but a few applications. “The generation of compressed air requires a great deal of energy. More than 90 percent of the energy consumed is converted into heat. Less than 10 percent is ultimately available in the form of compressed air. And of this, some 30 percent is lost through leakage.” If a company couples the compressor that generates compressed air with a cogeneration plant, thus using the waste heat, and also eliminates air leaks, it can achieve considerable efficiency improvements. And this is not to be underestimated from the perspective of society as a whole: EnergieSchweiz calculates that around two percent of Switzerland’s energy consumption is attributable to compressed air applications.
Last but not least, Alexander Sauer believes that a great deal can be achieved just by applying common sense: “Although automated lighting systems that can be linked to an intelligent energy management system are available, a company does not necessarily need complex controls to switch off the lights, shut down the machines, and close the doors.”
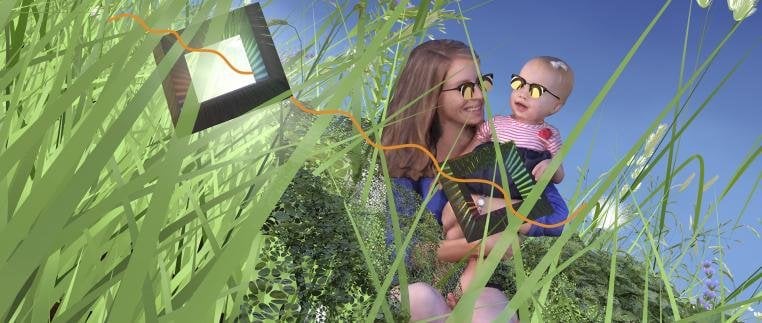
Efficient use of energy protects the environment and saving costs
www.bystronic.com