www.industryemea.com
14
'20
Written on Modified on
GERMANY’S FIRST ELECTRIC CAR FACTORY SETS NEW STANDARDS
The world’s largest car manufacturer is getting ready for the future. Over the next few years, Volkswagen will make a radical transition to e-mobility, and the Volkswagen plant in Zwickau, Germany, will play a key role in this process. With the ID.3 model, the blueprint for the new generation of electric cars is being created here. The bending experts from Bystronic are also on board.
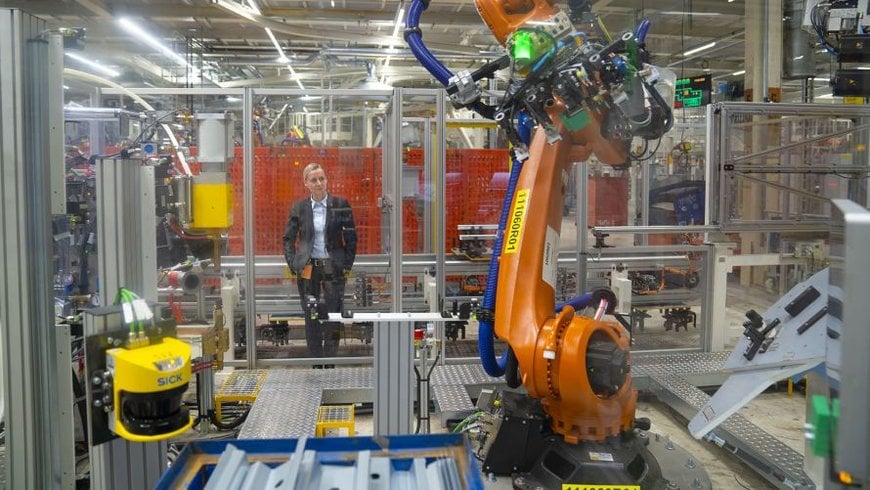
Much of what happens in the automotive industry goes on behind closed doors. This includes the realignment of the manufacturers towards e-mobility. But when the German Chancellor Angela Merkel herself fires the starting signal for the production of the new Volkswagen ID.3, everything is already very much in the open. This was the case last November in Zwickau, in the German state of Saxony. This is where the production lines for what could be the most ambitious current project in the entire automotive industry kicked into motion.
The ID.3 is more than just a new model; this new electric car embodies the future of Volkswagen and is intended to usher in a new era. The Group has set itself the objective of becoming the leading global manufacturer of e-vehicles. And this mission is being pursued with a vengeance. With investments of 1.2 billion euro, Volkswagen wants to turn Zwickau into the home of Europe’s largest e-mobility factory. In 2021, more than 330,000 electric cars are scheduled to roll off the production line.
Platform for the whole family
So far, sales of electric cars have been sluggish. The ID.3 is designed to change this – thanks to an attractive price of below 30,000 euro, rapid charging capability, and a range of up to 550 kilometers. Jürgen Stackmann, a member of the Board of Management of the Volkswagen Passenger Cars brand, promises: “The size of a Golf on the outside, the space of a Passat on the inside, and the acceleration of a GTI.” Apparently, the customers very much appreciate these attributes: More than 37,000 cars have been pre-ordered and will be delivered starting this summer.
The ID.3, the first model in the ID. family, forms the basis for a zero-emission generation of vehicles. The modular electric drive matrix –MEB for short – offers the necessary scalability from the compact car to the bus: By 2022, it will be incorporated in 27 models of four Group brands. The “ID.R Pikes Peak” prototype has already proven that the sky is the limit. On June 24, 2018, at the mountain race in the US bearing the same name, the supercar with its 680-horsepower electric four-wheel drive made motor racing history and beat the previous record set by rally legend Sebastien Loeb by a large margin. This sports car will remain a racetrack dream, but it shows in an impressive way what the ID family can achieve.
76-second cycle time
Kati Langer stands in Production Hall No. 12. She is inspecting the Xpert 40, which is connected to two Kuka robots in a production cell. The passionate Bystronic saleswoman, who has accompanied the ID.3 project with Volkswagen from the outset, is quite obviously proud of the system. In order to seamlessly integrate the bending systems into Volkswagen’s workflows, we had to overcome a number of structural challenges, she explains while we watch the two bending robots at work.
The first robot removes the part from the container station and deposits it on the centering system. The second robot picks it up, swiftly feeds it to the bending machine, and performs the first of two bending steps. Then it returns the part to the centering system and the first robot completes the remaining bending steps. Subsequently, a stationary system welds two ball nuts to the part. The gripper then picks up the part and places it on the conveyor belt.
The entire process takes exactly 76 seconds. Watching the robots perform their bending sequences is a genuine delight. If you hadn’t seen it with your own eyes, you would hardly believe how elegantly and nimbly the two robots work hand in hand – or rather gripper in gripper. Subsequently, the bent part is installed in the support structure of the chassis where it stabilizes the undercarriage. A second fully-automatic bending cell manufactures a component that is installed at the front of the car chassis.
www.bystronic.com