www.industryemea.com
25
'20
Written on Modified on
THE SMART MONEY IS ON ENERGY EFFICIENCY
Editorial by Steed WEBZELL.
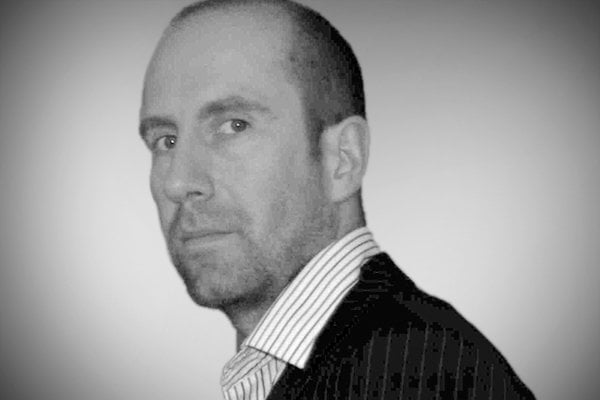
As Europe emerges from the grip of its COVID-19 crisis, manufacturers, process plants and other industrial facilities are awakening to a “new normal”. In recent weeks, machinery that had stood idle since March has begun whirring into life, and production staff have been making their way back to the shop floor, at a safe working distance, of course.
Sure enough, things are different now, but for how long? This million dollar question is one that few are brave enough to call at this stage. However, judging by major disruptive events in history, time heals wounds ... and economies. Confidence will return and investment levels will rise once more. In the meantime, the trick is to be smart about manufacturing and save on unnecessary outgoings. Within this remit, overheads are a key target as they typically constitute 30-40% of total production costs.
Sure enough, there is little that manufacturers can do about certain overheads, such as the depreciation of plant and machinery, or the cost of insurance, for example. However, when it comes to energy costs, there are major savings to be had with the right approach. The convention of powering everything up in the morning and powering it all down in the evening is no longer appropriate in a highly competitive industrial landscape.
Monitoring should be the first step in any energy-efficiency drive. Industrial facilities must be aware of how much energy is being used, and when, to ensure they make the right changes to their strategies and the right investments; ones that deliver the quickest return. Indeed, monitoring can sometimes provide surprising insights. For instance, it may become evident that certain machinery or plant equipment is idling for extended periods when it can instead be turned off. Similarly, data might reveal that some lighting circuits are being left on for entire shifts, when they can in fact be powered down for specific time periods. For this reason, the use of occupancy sensors has gained much traction in industrial settings over recent years.
With monitoring addressed, data trends will emerge that can be used to shape the energy strategy moving forward. Perhaps a manager or team leader can be appointed to take ownership and drive the project, with the best suggestions taken forward to implementation.
Some ideas will be common sense and can be actioned successfully with relative ease. However, in the age of the smart factory, there is a growing train of thought surrounding energy. What if energy monitoring and control could be achieved using Industry 4.0 strategies, with consumption data for machines, plant, equipment, systems and lighting all metered, analysed and managed via the Cloud? Well, the good news is that the technology already exists to make this vision a reality. Moreover, a number of case studies have emerged of industrial facilities successfully adopting this technology. Such premises are not only saving money, but reducing their carbon footprint and, in turn, boosting their environmental credentials.
The capabilities of Industry 4.0 and, subsequently, smart factories, have been mooted for a number of years, with a greater number of projects now coming to fruition. However, the nature of the Industry 4.0 ethos is intrinsically linked to scalability, so it perhaps comes as no surprise that concepts such as smart lighting, for example, are today being included in holistic “smart” strategies.
Of course, the havoc, misery and tragedy that the pandemic wreaked across Europe should never be forgotten. Few people or businesses will have escaped its effects. But now the rebuilding starts. And although civilisation, including industry, can do little else but live with this virus in a pre-vaccine world, the time to start adapting to the new normal, is now.
Steed WEBZELL