www.industryemea.com
09
'20
Written on Modified on
REMOTE TESTING IS THE KEY TO CONTINUITY AND EMPLOYEE SAFETY IN TESTING NEW NETWORK EQUIPMENT, SAYS HUBER+SUHNER
The ongoing Covid-19 pandemic has shown how important it is for companies to operate remotely.
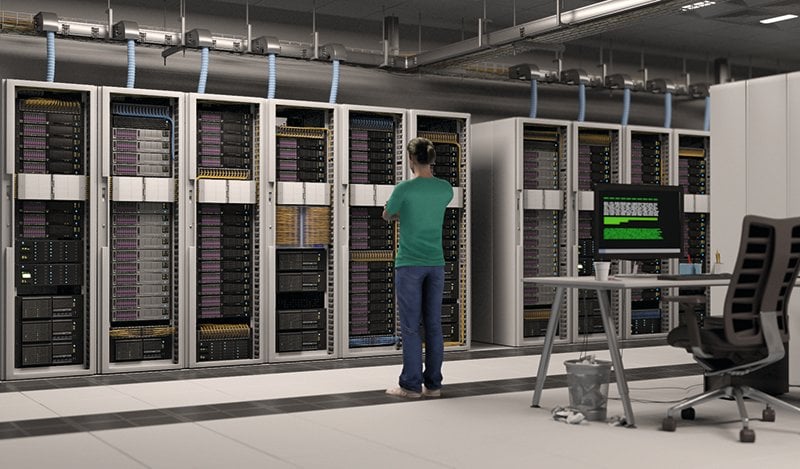
In fact, it’s the difference between completing a task or facing extensive delays for businesses relying on new, certified equipment for day-to-day activities, Chris O’Conor, Regional VP, Service Provider Sales at HUBER+SUHNER Polatis said today.
According to O’Conor organisations are under intense pressure to rapidly test and deliver enhanced network services, validate new equipment and quickly resolve customer issues. To do this they must get more out of their network system test resources. In today’s ever-changing business climate, automating test infrastructure and resources is vital to increase test capacity while reducing costs.
O’Conor added that testing and certification of new devices prior to deployment in networks depends on technicians. Typically, this is done on-site in confined spaces within test laboratories where each device is manually patched to test equipment, which may make it difficult to comply with social distancing requirements. The longer it takes to certify new equipment and new services relying on a manual test lab operation, the longer it will take to generate higher revenues and gain a competitive advantage – making fast, repeatable and agile lab operations crucial to reduce time to market.
“Lab automation is not a new idea, but many labs fall short due to a lack of investment in personnel and resources or simply little awareness that a well-run and automated lab can be a hugely competitive advantage,” said O’Conor. “By adopting innovative solutions, lab managers can simply deploy a component once and run all future tests remotely using orchestration software – perfect at a time when remote working has never been more crucial.”
O’Conor went on to explain that as networks are migrating rapidly to line rates of 400G and beyond, and more connected devices and equipment are required to deliver these expected services, the network test lab is becoming increasingly complex and expensive. Simply using traditional layer 2/3 infrastructure to interconnect equipment test beds adds complexity, increases costs and causes equipment to be upgraded every time the traffic speed or formats change.
All-optical switching overcomes these challenges by providing a transparent, user-configurable fiber layer independent of the traffic format or bit rate to enable customers to rapidly reconfigure network test beds in seconds, rather than hours or days, to meet the speed and flexibility required.
“What was once considered a luxury, is now a requirement as the current situation drives forward the inherent need for remote lab management,” concluded Chris O’Conor. “By adopting solutions like our Polatis optical switches, organisations can not only continue to operate as normal to ensure that projects are completed on time but also open up the capability to leverage a geographically diverse work force – allowing them to work across multiple test topologies simultaneously without concern of conflict between virtual networks.”
www.hubersuhner.com