www.industryemea.com
24
'20
Written on Modified on
SINK HANDLING BECOMES A ONE-MAN SHOW
Duravit not only attaches great importance to visual perfection, but also to ergonomic handling solutions during production. Duravit relies on vacuum tube lifters from vacuum specialist Schmalz to pack its beautifully designed ceramic sinks, which weigh up to 35 kilograms, into cardboard boxes after production. This reduces physically strenuous work as well as illness-related absences.
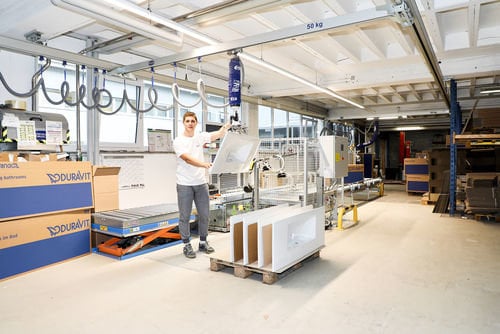
“The well-being of our employees is very important to us. That’s why we constantly try to improve work processes in order to optimize them and make them more ergonomic,” says Andreas Lotz, Head of Final Production at Duravit AG in Hornberg located in the Ortenau district of Baden-Württemberg. The company works with renowned designers to produce custom bathrooms with the aim of improving the quality of living for users in a lasting way. The leading international manufacturer is active in over 130 countries worldwide and has around 6,200 employees. 600 of them work at the headquarters in Hornberg. Their product portfolio includes bathroom furniture, showers and bath tubs, wellness systems, shower-toilets and fittings, as well as accessories and installation systems. Their primary business area is sanitary ceramics.
“We produce about 250 models in numerous variations of ceramic sinks, which can vary considerably in size and shape,” explains Lotz. During packaging for dispatch, an employee drives the sinks, which have been sorted and stacked, on pallet trucks to the packaging area. Previously, two employees removed the large sinks, which weigh between 20 and 35 kilograms, manually from the pallet without any aids and then packed them into cardboard boxes and placed them onto a pallet for further transport. Employees often manually lifted more than three tons by the end of each shift – “real heavy labor,” comments Lotz. Managers at the Hornberg site saw a need for action and focused on making work processes as ergonomic as possible. That was back in spring 2018.
Learning from Experience
“We already use vacuum handling devices from Schmalz in the grinding shop and for quality control, which allow heavy ceramic parts to be lifted, transported, and lowered ergonomically,” reports the head of final production. “We had no other choice since there was simply no room for a second employee.” And that turned out to be a good thing since both managers and, above all, operators were extremely satisfied with this solution. “We also decided to use a vacuum handling solution from Schmalz for packaging,” says Lotz.
The Glatten-based vacuum experts located in the Black Forest recommended two vacuum tube lifters from the JumboFlex 50 series for this task. These lifters can handle loads of up to 50 kilograms ergonomically and at a high cycle frequency. The production manager first goes to one of the vacuum tube lifters and then picks up the control handle. “The employee can effortlessly lift and lower the heavy ceramic sinks using central two-finger control and then release the load intuitively,” he explains. “It’s very easy.” Depending on the shape of the workpiece to be handled, the vacuum suction cup can be exchanged using a quick-change system as standard. Duravit has a total of three different suction cups available for this purpose. The work instructions tell the operator which gripper is needed for which model. Since the workpieces are always delivered sorted by type, it is rarely necessary to change grippers. “The double suction cups are currently equipped with two bellows suction cups each,” describes Lotz. “The bellows suction cups adapt ideally to the surface properties and geometry of the sinks.”
Smooth-Running Crane System
Schmalz combined the two vacuum tube lifters JumboFlex with an aluminum crane system. This two-beam overhead crane system is also designed for loads of up to 50 kilograms and has a working area of 13 x 4 meters. It is designed so that the two jibs can meet the vacuum tube lifters in the middle of the crane system. The aluminum lowers the weight and the ease of movement allows the operator to work fatigue-free for an extended period of time. This ensures both a high working speed and high positioning accuracy. To make the working atmosphere more pleasant, Schmalz also installed the vacuum generator in a silencer box. This not only reduces the noise level, but also protects the vacuum pump from external contamination.
Ideal for the Complete Line
When employees move the different models, which are sorted by type and per pallet, to the packer, they pick up the sink with the first JumboFlex and then carefully place it in the appropriate cardboard box. “We can now handle around 90 percent of large ceramic sinks with the vacuum tube lifter from Schmalz,” says Lotz with satisfaction. For models with asymmetrical shapes, the employees still have to work by hand. Once they are packaged and sealed, the goods are then transported on a roller conveyor to the end of the packaging line. The employee then picks up the package using the second vacuum tube lifter and places it on a pallet. Depending on the sink model, the workpieces can have unwieldy formats of up to 50 x 140 centimeters. “The packager handles more than 100 sinks in one shift, i.e. eight hours, with the vacuum tube lifters,” says Lotz. A colleague picks up the pallet with a pallet truck and transports it either to the high-rack storage area or to the shipping department in the central warehouse.
Duravit set a clear goal: To improve the ergonomics of the packaging process and thus protect the health of its employees. “Thanks to the vacuum tube lifters and crane system from Schmalz, we achieved an optimal result,” says the production manager with delight. The improved ergonomics have a positive effect on both the health and motivation of employees. Andreas Lotz is also enthusiastic about the cooperation with Schmalz: “Our trust was effective. We will definitely reach out to Schmalz again when it comes to ergonomic solutions for our employees.”
www.schmalz.com