www.industryemea.com
30
'20
Written on Modified on
For the development of a vaccine logistics system: Deep-freeze storage in container design
Once an effective COVID19 vaccine is available in the required quantities and is to be delivered to the vaccination centres, a specific logistical task also needs to be addressed: The vaccine must be transported at a temperature of at least -70oC to -80oC and stored on site at the vaccination centre. L&R Kältetechnik has developed a safe, flexible and economical concept for this demanding type of deep-freeze storage: a deep-freeze storage system that is installed in an industrial container.
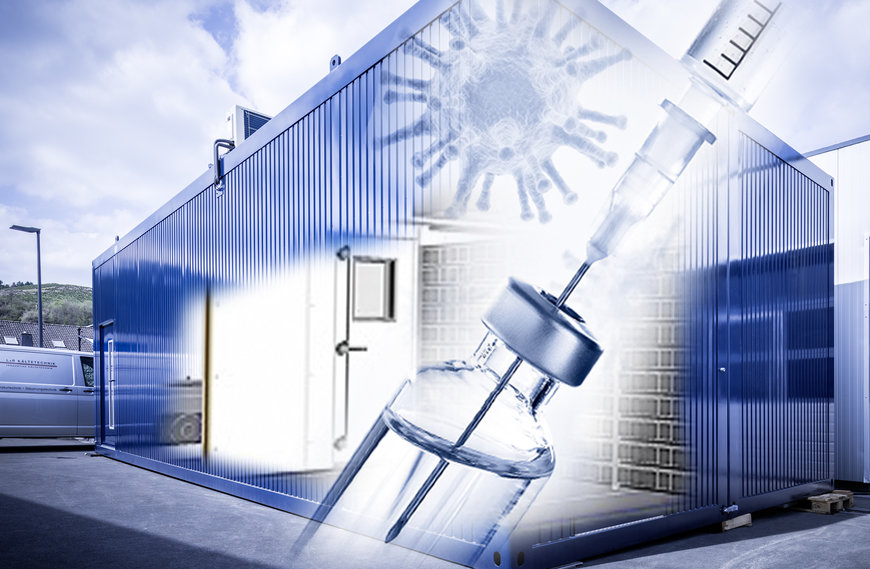
L&R has extensive experience with the deep-freeze storage of sensitive pharmaceutical active ingredients and products. Vaccine serums, blood plasma, stem cells, bone marrow and biomedical materials are among the stored goods that are kept in the walk-in L&R deep-freeze storages at temperatures down to -110°C. Such storages are in use at many pharmaceutical manufacturers - among other reasons also because they are more reliable, efficient and energy-saving than laboratory freezers.
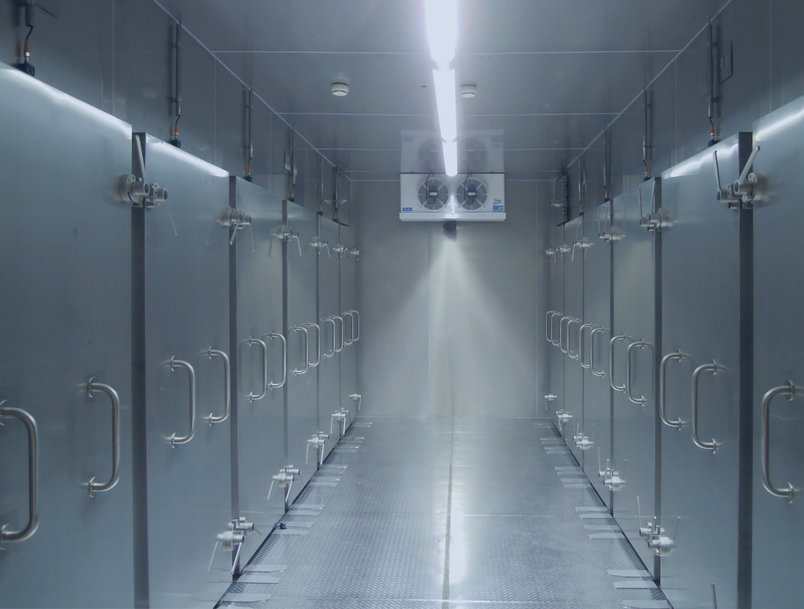
Based on this experience, L&R has now developed a solution with which millions of vaccine doses can be stored at -80oC. The basic idea: The storage cell -80°C with a precooling room -20°C is installed in an industrial container with corresponding redundant, multi-stage refrigeration technology in order to guarantee a storage option that is suitable for pharmaceuticals.
Two highly efficient refrigeration systems are installed in the 20' or 40' containers, each of which ensures a permanent temperature level below -70oC. The systems are air-cooled, so only one mains connection is required for operation. And they have a redundant design so that if one refrigerating circuit fails, the second circuit can automatically take over the cooling. An optional emergency power supply or nitrogen emergency cooling (LN2) offers an even higher level of safety.
The interior equipment of the cryogenic storage is adapted to user requirements. Pallet storage spaces are possible as well as shelves and/or drawers for different product sizes. Optionally, the interior can be manufactured with a stainless steel floor according to cleanroom standards. The highly effective insulation ensures a low heat transfer coefficient. This increases the temperature holding time and reduces the energy requirement.
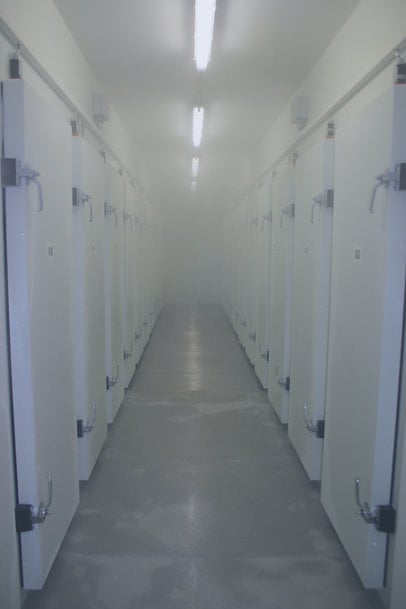
The deep-freeze containers comply with GMP requirements; they are optionally supplied with FDA approval for materials in contact with the product. Via the touch panel of the Siemens PLC, the user can control the system comfortably, and visualize the process. Remote maintenance is possible as well as GPS positioning of the container. Further options are realized according to the customers’ specifications.
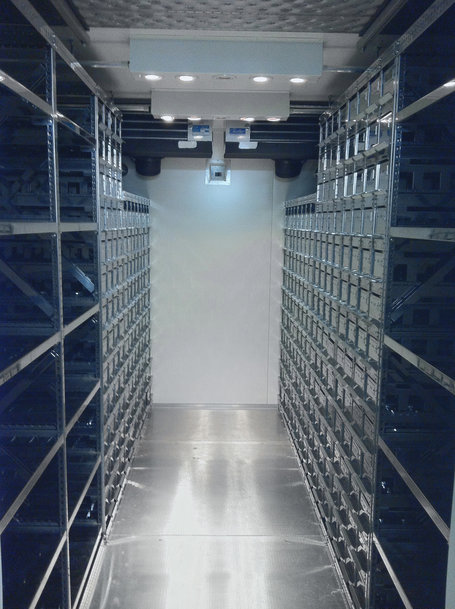
In the construction of this deep-freeze storage system, attention was not only paid to maximum safety and high energy efficiency: the worldwide availability of the components also played a role. Burkhard Rüßmann, general manager of L&R Kältetechnik: “When the vaccine production starts, the logistics must be available all the way up to the vaccination centres - not only in Germany. That's why we have made sure that our production is scalable over a wide range.”
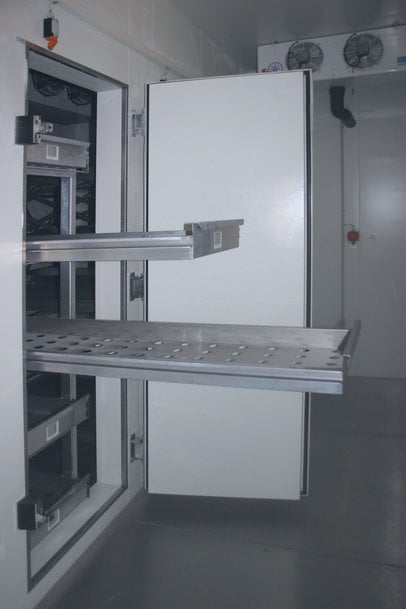
The container design is the basis for the high-quality systems to be set up with very little effort exactly where the vaccination is carried out. And it offers another advantage: Over the rest of their lifetime, the mobile deep-freeze stores can afterwards be used at other locations and for other tasks.
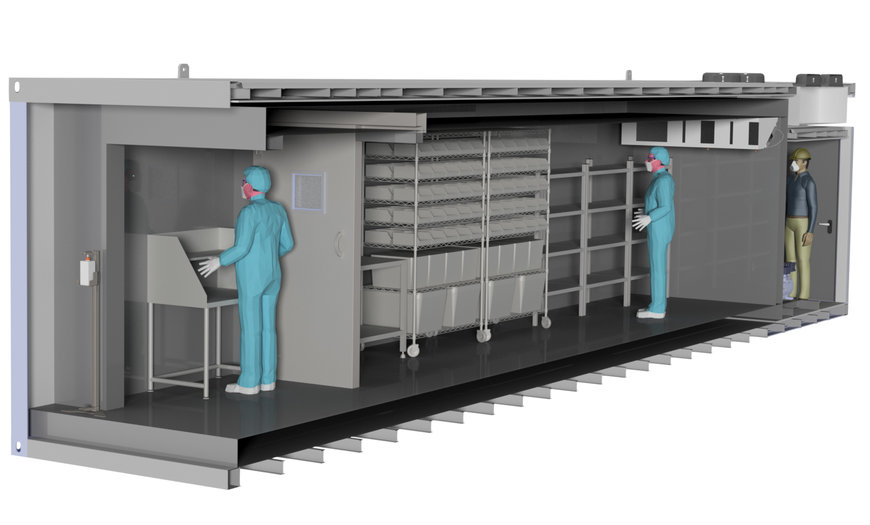
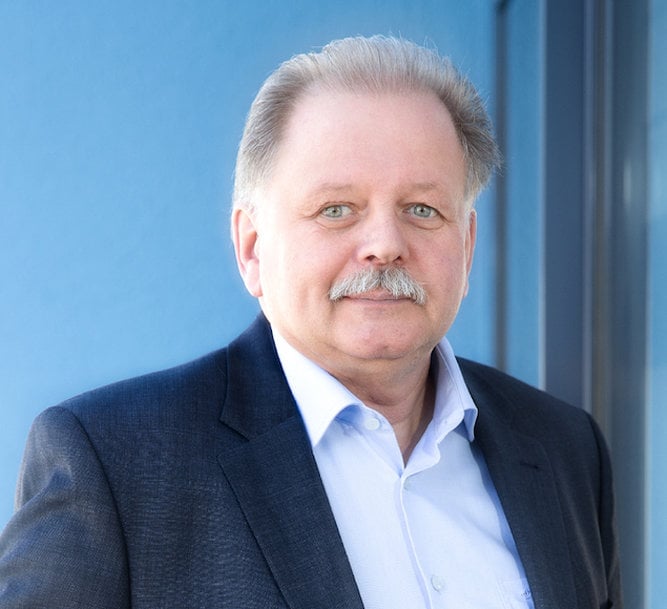