www.industryemea.com
10
'13
Written on Modified on
Champagne producer Veuve Clicquot chooses PcVue to supervise its tanks
World-renowned top-quality champagne house Veuve Clicquot uses instrumented and automated facilities. Thanks to PcVue, it now has a smart system that supervises fermentation in its 400 fermentation tanks.
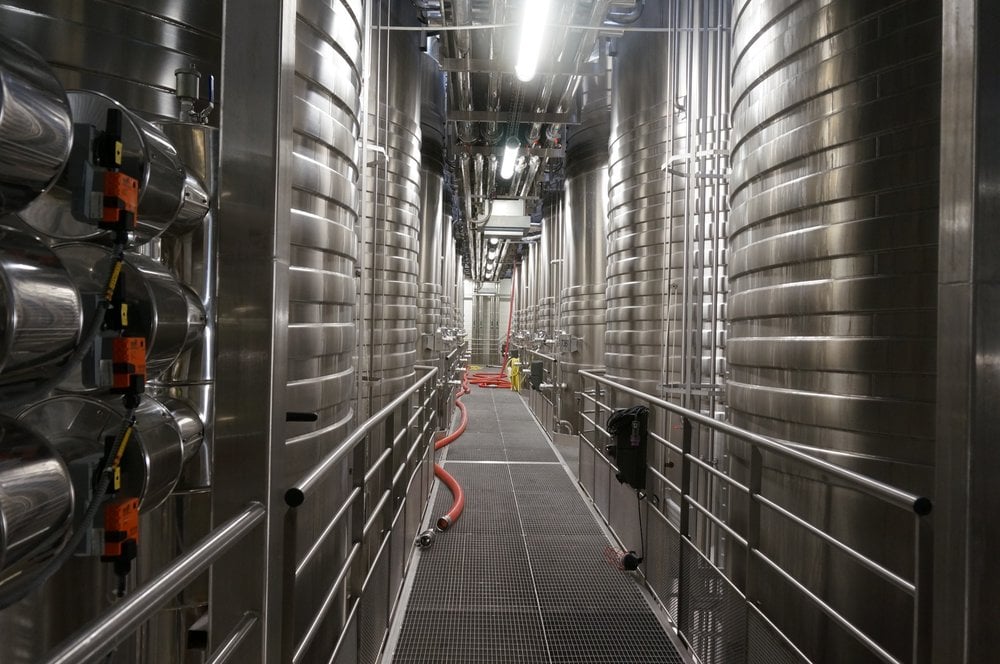
Veuve Clicquot champagne is stored in 400 fermentation tanks.
Veuve Clicquot is a French champagne house known the world over. Founded in 1772, this prestigious house is now a subsidiary of LVMH. Its reputation is obviously no accident. The house does not compromise on quality and its motto is 'Only one quality – the finest'. In order to ensure that it always makes the finest champagne, it also needs to be able to closely supervise its production systems.
That is why, in late 2012, Veuve Clicquot revamped its fermentation cellar supervision system. The fermentation cellars are where the house makes its wine from harvested and pressed grapes. Supervising the tanks in which alcoholic and malolactic fermentation take place is crucial. However, the software being used by Veuve Clicquot was at the end of its life and the publisher was no longer supporting it. It was therefore necessary that the house replace its 10-year-old supervision system by a more recent and better performing solution. "We needed to replace it by a lasting solution that would be supported for many years to come," says Franck Berruyer, sales engineer at Arc Informatique, the company behind the PcVue supervision system installed at Veuve Clicquot. "In addition to various technical factors, we chose the PcVue 10 software suite because of the relationship of trust we have maintained with Arc Informatique and because the cost of the licences is economically suited to Veuve Clicquot's needs," says Stéphane Fournier, manager of SF2I, the company that developed and integrated the supervision software. Another advantage of PcVue is that it has the same HMI as the previous software, meaning that the operators were able to use PcVue immediately. Furthermore, Guy Jendryka, manager of the electricity, automation and industrial computing department at Veuve Clicquot, stresses that one of PcVue's strengths is that it is easy to adjust and program. "With the previous system, you really had to be an IT specialist to be able to upgrade the software. PcVue is much easier to modify as needed."
The development architecture is based on PcVue objects and greatly facilitated the supervision software's design. Because Veuve Clicquot's fermentation cellars contain 400 tanks of various types and volumes (50 hl to 725 hl), the developers had to be able to use models so as to reduce programming, and hence maintenance times. Depending on their type, the tanks are fitted with up to three temperature-control sensors and manual or automatic valves. The application manages some 40 variables per tank for a total of 16,000! "The object development architecture saves time and simplifies operations. Once the model was made for the dozen existing tank models, it was simply a matter of instantiating the objects and automatically generating the communication variables," says Mr Fournier.
With its virtual architecture, PcVue runs on a server that is installed in a secure, air-conditioned and filtered room protected from the damp. The application's maintainability and portability on new physical machines is thus simplified. The fact that, in such a virtualised environment, the software is decoupled from the hardware means that reinstallation and commissioning times in the event of failure are considerably reduced.
The operators control the PcVue supervision software via a 42" touch screen installed at the entrance to the fermentation cellars.
Five web-based clients allow the cellar managers to view the supervision system and select its setpoints via their PC. Operators can also monitor and control the software via a 42" touch screen that is installed in the lobby and within view of all visitors. The software communicates with the programmable logic controllers (PLCs) over a Modbus TCP/IP network while a VPN (virtual private network) link is used to collect information from the tanks in the house's other fermentation cellars. Fourteen fermentation modules are housed in the main cellar in Reims and four others are located in various towns across the Champagne vineyard at distances of 30 to 200 km from the main cellar! The VPN saves a tremendous amount of time. "Being able to supervise all our fermentation cellars from one place eliminates the need to drive to each cellar. The supervision system issues an alert if a serious temperature control issue crops up," says Stéphane Fournier.
Mr Jendryka can now monitor all his tanks from his desktop PC. "PcVue supervisor has made our fermentation cellars smart. We can monitor every aspect of temperature control from just one place."
Encouraged by this positive experience, Veuve Clicquot's technical teams quickly realised how PcVue could be used elsewhere. Not only does it supervise the fermentation of wine in the tanks, it also monitors the production of cold during cold stabilisation after final blending.
PcVue does not control these operations; it is used simply to view their settings and archive, log and track temperatures, faults and other data. It is also used for effluent monitoring purposes at the two treatment plants – it manages acid and sodium-hydroxide levels, tracks pH and flow-rate values (weekly dashboard report for Dreal, the regional directorate for the environment, land-use planning and housing) – and to e-mail resupply alerts to the managers when levels become low. And that's not all! PcVue is being deployed to other areas of Veuve Clicquot's operations. By the end of the year it will be running on the wrapping line (placement of foil capsules and labels on bottles prior to shipment). "We are going to use it in particular to retrieve production orders from SAP and provide the laser ID to be affixed onto the glass and back-label," says Mr Jendryka.