www.industryemea.com
25
'21
Written on Modified on
Combatting counterfeits
Why mission-critical industries need to fight the fakes.
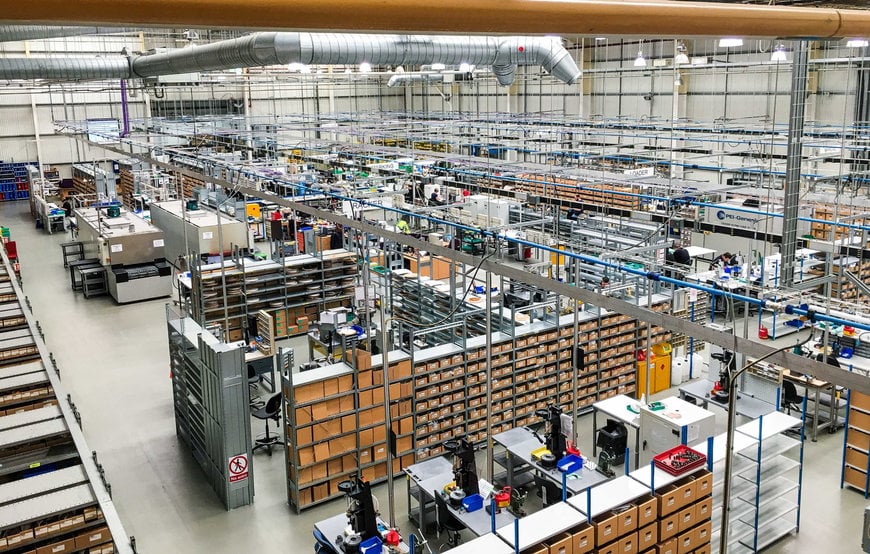
After some respite in 2019, the global shortage of electronic components worsened in 2020 due to a perfect storm of factors. Here, Jonathan Parry, Senior Vice President of Global Operations and European Managing Director at cables and connectors specialist PEI-Genesis, explains how the shortage is driving counterfeits in mission-critical sectors, and what industry needs to do to combat the counterfeits.
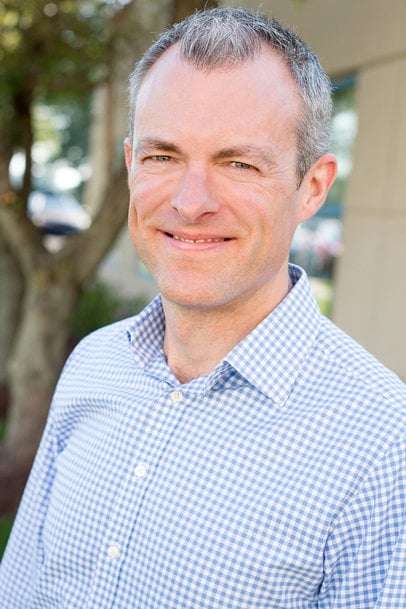
In meteorological terms, a perfect storm refers to the phenomenon born at sea when warm air from a low-pressure system collides with a flow of cool, dry air at high-pressure — simultaneously fuelled by warm, moist air from tropical climes.
It’s a perfect storm, then, that best describes the events over the last five years that have led to a global shortage of electronic components. The primary ingredients? Combine the US-China trade war and Brexit, rising copper commodity prices, the growing adoption of electric vehicles, record sales of industrial robots and a global pandemic in the form of Covid-19, and you have quite the storm.
Driving counterfeiting
A consequence of the global component shortage is the rise in counterfeiting. The mix of shortages, price hikes and obsolescence is driving many OEMs to take shortcuts. Research firm Havocscope estimates that there is $169bn worth of counterfeit parts in circulation in the marketplace. You don’t have to knowingly buy a fake to be affected either.
Despite being synonymous with the term fake, counterfeit parts include everything from unauthorised copies to those with incorrect or false markings. It also covers parts that don’t conform to the original design, model or standard; parts produced by unauthorised contractors; parts that are off-specification; and defective or used parts sold as new.
For the user, the consequences of counterfeits can range from mild: a loss of accuracy in a desktop robot used for small electronics assembly, to life-threatening: a pump failure in a portable ventilator, or an unresponsive sensor in a passenger plane.
It’s an issue that remains at the forefront for PEI-Genesis. We are partly a distributor but also one of the fastest assemblers of cables and connectors in the world. Headquartered in Philadelphia, in the United States, we have manufacturing facilities in North America, Europe and Asia, exclusively supplying the military, industrial, medical, aerospace, transportation, and energy sectors worldwide.
On one project, in the aviation sector, our connectors are used on Boeing’s new 777X, the world's largest and most efficient twin-engine jet airplane. We supplied a range of connectors that can suppress electromagnetic pulses and shield against other forms of radiofrequency interference. A lesser counterfeit part would lack the adequate engineering, longevity and material quality, severely compromising safety.
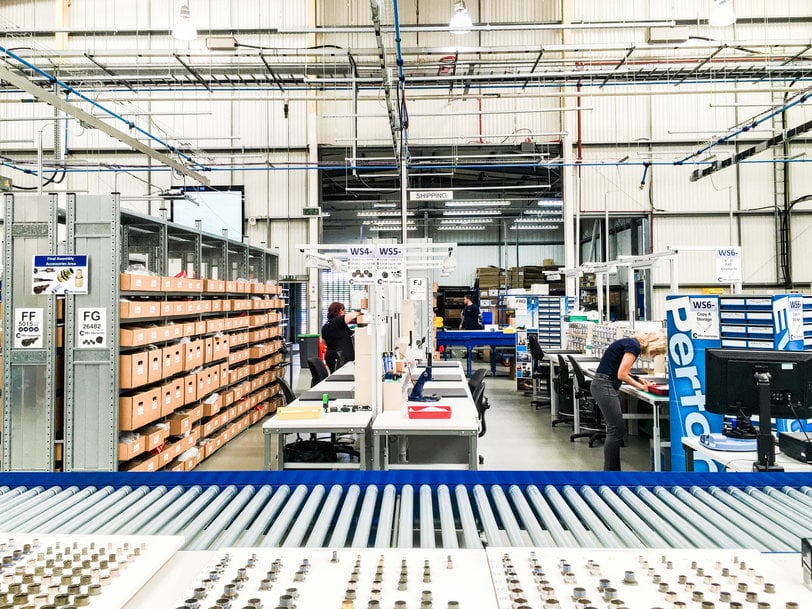
Breaking the chain
We’re uniquely placed to break the chain between component shortage and counterfeiting. We have about $90m dollars of global inventory, but the unique thing is that we hold it in component form. So, rather than hold finished products that may become obsolete, we can build millions of combinations of products using these parts. Combined with a highly automated manufacturing process that promises a 48-hour lead time and a minimum order quantity of just one, there’s no reason for customers to turn to counterfeits.
OEMs should be wary of the grey market. Buy from trusted distributors that have long standing relationships with the major brands. For brands like ITT Cannon and Amphenol we must make sure we abide by their stringent quality standards. Customers can audit our manufacturing facilities at any time, and they regularly do, once a week or so.
Over time, this transparency means that we’ve reached a trusted advisor status for many of our customers, particularly those in the defence sector, where safety is paramount. In these sectors, price is often a secondary consideration to safety and being able to trust that your supplier will deliver parts that will protect people’s lives becomes the primary objective.
Supplying cables and connectors into hazardous areas means we must provide traceability from cradle to grave. We track supplier shipments from the moment they enter the manufacturing facility to the finished product we send to customers. We inspect deliveries, matching the shipment to our records, and every person in the process wears an armband to log the movement of parts. This means we can trace a cable or connector back to when and where in the world it was produced, where the components came from and who quality-checked the product.
We live in turbulent times and industry faces a challenge that is, while difficult, not insurmountable. Understanding the nature of fakes, choosing carefully where you buy your parts and ensuring traceability in your supply chain is what’s required to create an equally perfect storm of countermeasures.
www.peigenesis.com