www.industryemea.com
04
'21
Written on Modified on
A NEW ERA OF PRODUCTIVITY
Today's plants and machinery take up a lot of space. But only a fraction of their footprint contributes to the production process itself.
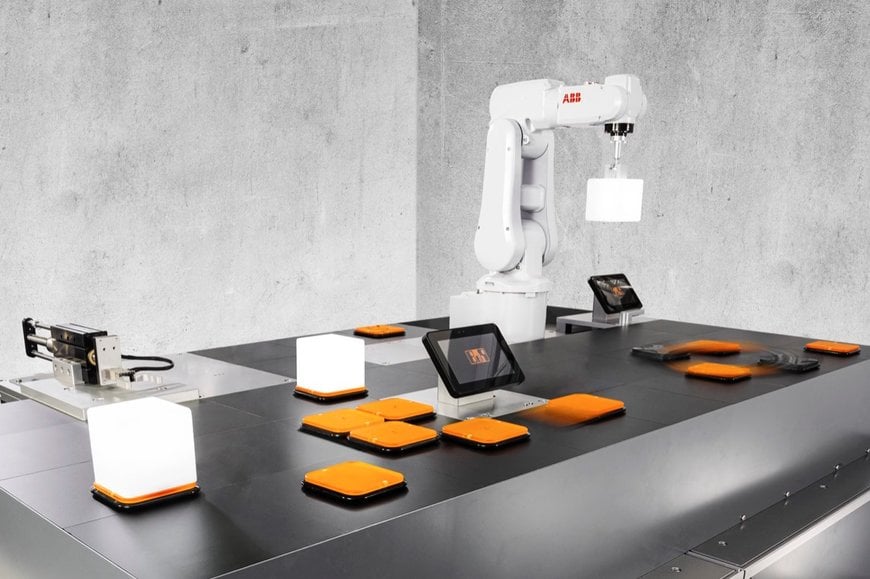
Author: Stefan Hensel, Corporate Communications Editor
Far more real estate on the plant floor is dedicated to carrying products from place to place. The time has come to break free from the limitations of one-dimensional product transport – and set the stage for a new era of productivity.
Conveyor belts, rotary tables, carousels – there are many ways to move products from processing station to processing station. But they all have one thing in common: they don't contribute to the production process itself. Quite the opposite, in fact – they consume valuable floorspace and reduce the overall output per square meter.
"For machinery and equipment manufacturers, product transport is simply a necessary evil," says B&R mechatronics expert Dario Rovelli, not mincing words. In addition to all the space they take up, conventional product transport systems have a second costly disadvantage: they make the machine inflexible.
Henry Ford's breakthrough in industrial mass production was achieved through conveyor belts and strict production cycles. But, what once lifted productivity to new heights now weighs it down. Says Rovelli: "To meet the demands of smaller batches, shorter lifecycles and increasing personalization, we need to remove the shackles of rigidly sequential production."
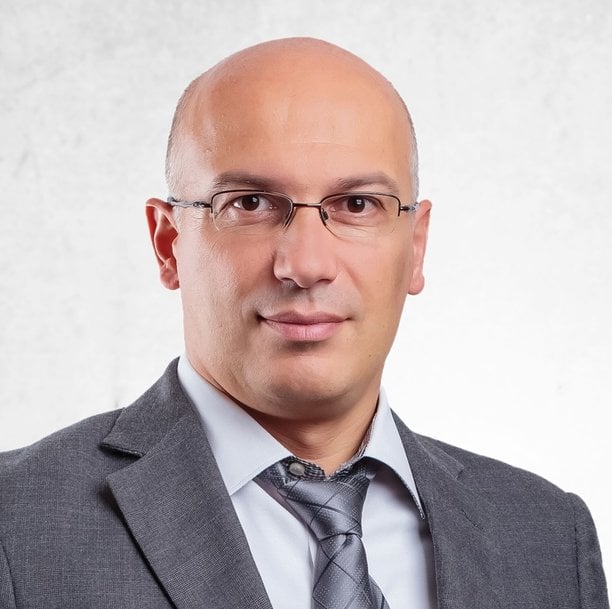
"The time has come to break free from the limitations of one-dimensional product transport – and set the stage for a new era of productivity," says Dario Rovelli, Head of Product Management - Motion & Mechatronic Systems at B&R.
More flexible with track systems
In recent years, new technologies have made production much more flexible, especially track systems like SuperTrak and ACOPOStrak. They can move each product independently and can also serve as a motion control axis at processing stations. Not only that, but they allow product flows to divide and merge at full speed.
"Track systems have set a major milestone," explains Rovelli, "by synchronizing asynchronous processes." In other words: productivity is no longer throttled to the speed of the slowest processing station. By adding multiple instances of slower stations, an incremental investment brings exponential gains in productivity.
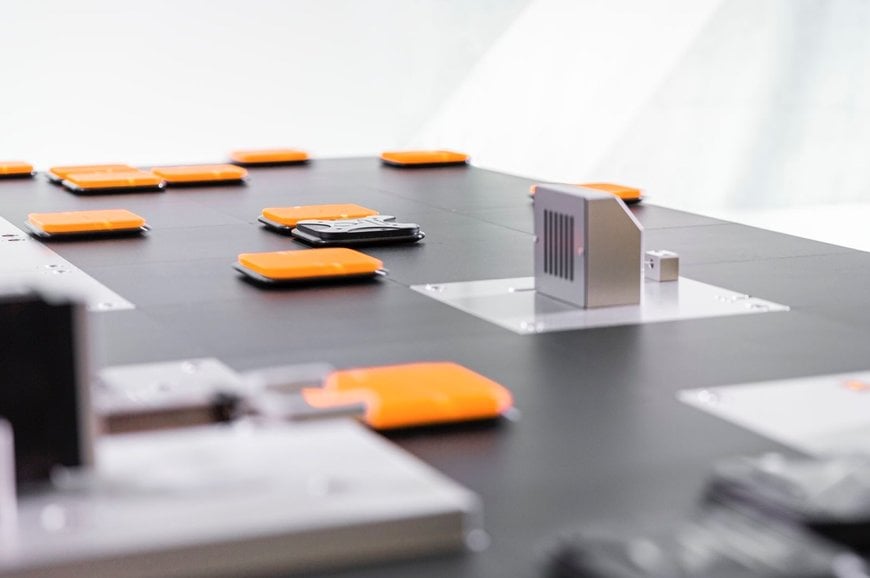
Dissolving the traditional model of linear product transport creates a multidimensional production space.
Mass customization
"Track systems let you do mass customization – for the first time – in a way that is economically sustainable," says Rovelli. Wherever there is a clear sequence of processing steps that need to be adapted dynamically to each product, a track system provides the necessary flexibility. Yet, there are other applications where the sequence of steps itself is constantly changing. These applications demand complete freedom in the flow of production.
"Manufacturing visionaries have had a dream for many years," says Rovelli. "They dream of dissolving the linear model of product transport entirely, and creating a multidimensional manufacturing space – where each product moves independently from station to station without being bound to a rigid, sequential production flow."
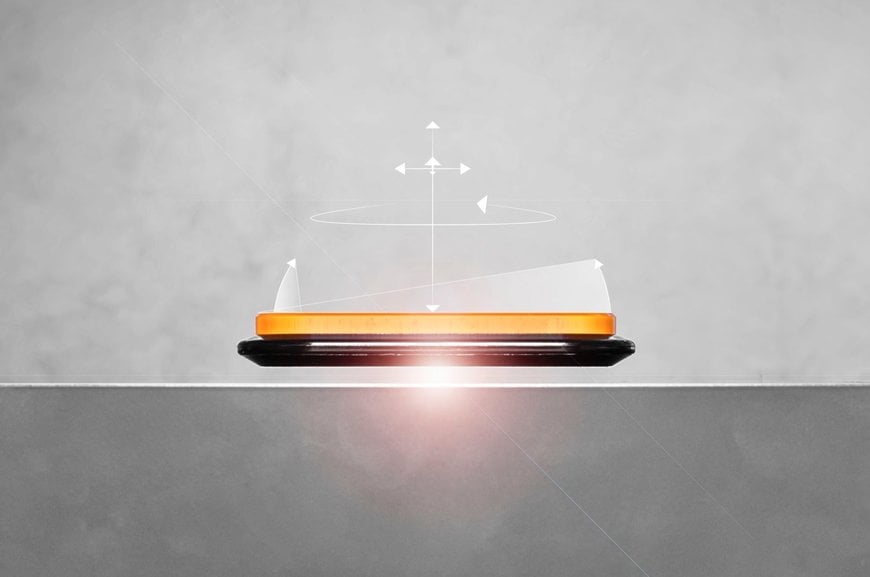
Magnetic levitation technology makes it possible to move and manipulate products with six degrees of freedom.
Contactless, noiseless, precise
What has long sounded like wishful thinking is now becoming reality, thanks to modern magnetic levitation technology. As if guided by an invisible hand, shuttles glide freely above a surface, accelerating and maneuvering skillfully in every direction. "Ever since the first time I saw this technology in action, I've been completely fascinated," says Rovelli. "It's contactless, noiseless and extremely precise. I realized immediately the profound impact it would have in shaping the world of manufacturing for years to come. And now, magnetic levitation has advanced to the point where it can deliver serious benefits in industrial applications."
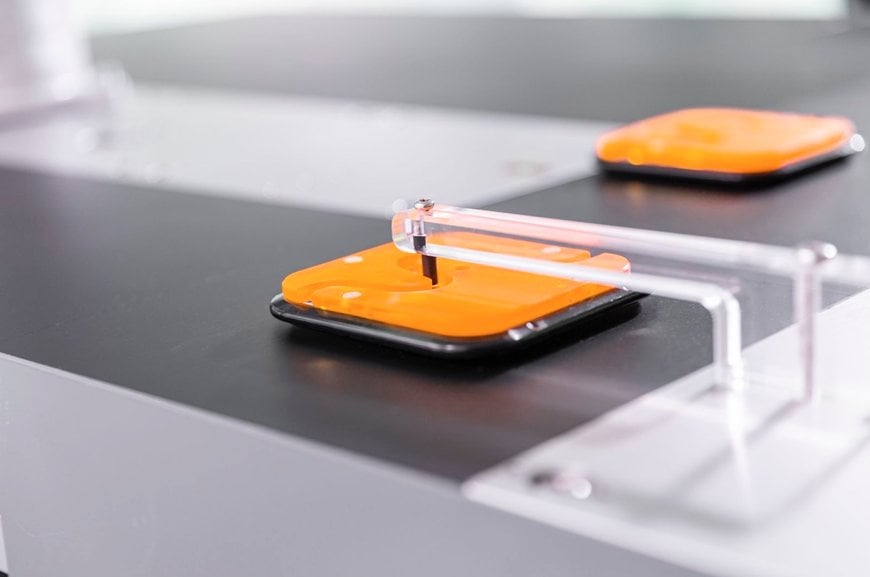
An ACOPOS 6D shuttle carrying a workpiece could follow a CNC path, for example, allowing the processing tool to be mounted rigidly.
The future of manufacturing
This same vision led B&R to fully integrate magnetic levitation technology into its automation system. ACOPOS 6D now heralds a transition from strictly linear production to an open, adaptive manufacturing space. "We're talking about nothing less than a revolution in the way products are manufactured, assembled and packaged," Rovelli says.
Cropping up again and again in discussions of Industry 4.0 and the Industrial Internet of Things has been the concept of products navigating their own way through the production process. "It's often been dismissed as a pipe dream," says Rovelli, "but now we actually have the technology to turn the vision into reality." With ACOPOS 6D, one machine can simultaneously manufacture different product variants or even entirely different products. Each product navigates its own path to the stations it actually needs. "We're witnessing the birth of swarm production."
www.br-automation.com