www.industryemea.com
08
'21
Written on Modified on
Can machines think?
The potential of artificial intelligence in motors and drives.
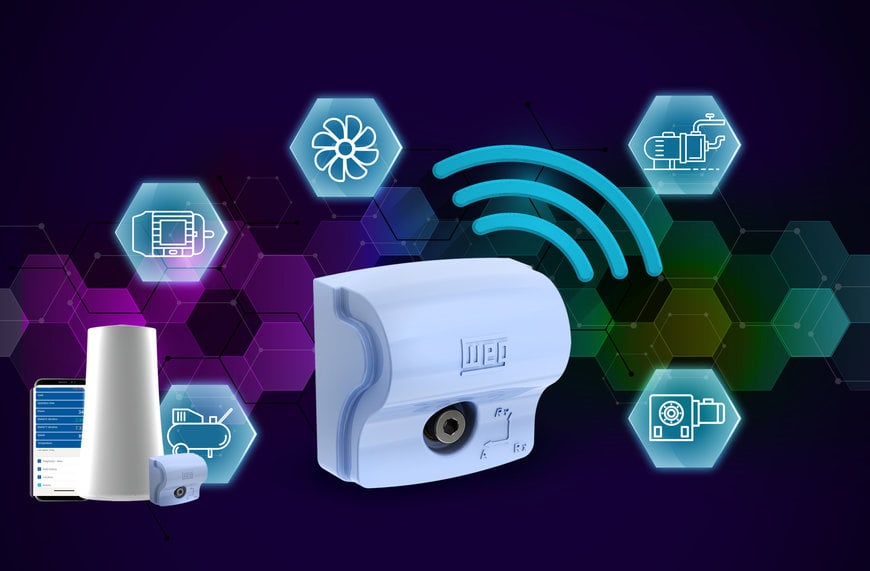
Computing Machinery and Intelligence, the seminal paper by Alun Turing, posed the question, “Can machines think?” Turing's research proved that a digital computer could simulate the behaviour of any other digital machine, given enough memory and time.
Here, Marek Lukaszczyk, European and Middle East marketing manager at motor and drive manufacturer WEG, explains how this has led to an effective digital manufacturing environment in which the potential of artificial intelligence (AI) in electric motor and drive applications could soon be unleashed.
AI, which was originally coined by American academic John McCarthy in 1956, involves creating algorithms and programs that allow computers to follow hundreds of millions of instructions — thanks to significant improvements in data-processing power and the advent of big data.
In fact, AI is now a key component in today’s manufacturing plants. Advanced machine learning has allowed computers to solve problems without needing to follow a comprehensive list of instructions. This allows powerful programs, which are based on neural networks, to be trained to perform specific tasks, carrying huge potential for motor and drive applications.
Motion Control
Design engineers want to introduce the power of AI to motors, for advanced motion control. For example, embedded algorithms could be used, based on information provided by intelligent sensors, to alleviate some common motor performance limitations.
Essentially, these systems compare a data-based model of motor performance with real time analytics to correct performance issues with voltage commands, generating torque when phase faults arise. The goal of these systems is to minimise the impact from phase faults, making them more manageable, especially in critical safety situations.
Additionally, these motors can boost motion control performance by improving efficiency, uptime and energy consumption. By using WEG’s motor scan, the performance of electric motors can be monitored with sensors, which facilitates predictive maintenance. Once installed onto the motor, WEG’s motor scan technology uses these sensors to send data to the cloud for analysis, alerting operators to suboptimal data trends.
What the future holds
In the past, technology was simply too expensive to measure the temperatures in an electric motor. Since then, however, sensors have developed and become much more accessible.
For example, thermal protection is achieved by monitoring the temperature of the motor windings. By using Positive Temperature Coefficient (PTC) sensors, thermistors can be installed into the motor windings to protect the motor against locked-rotor conditions, continuous overload and high ambient temperature.
Going forward, scientists from the Department of Power Electronics and Electrical Drive Technology at the University of Paderborn aim to develop software capable of estimating the temperatures at certain points. As part of the project, funded by the German Research Foundation (DFG), researchers are using AI and machine learning to find new models for estimating the temperature in drives and other power engineering applications.
This involves training their software, with a software testing method that examines the functionality of an application without peering into its internal structures, and test-bench measurements, to obtain precise temperature readings.
Turing's research proved that a digital computer could simulate the behaviour of any other digital machine, which has led to digital manufacturing as we know it. AI holds huge potential, especially for electric motor and drive applications, but research still has some way to go.
www.weg.net