The new Voith OnCare.pmPortal – Digital data and inventory management for maximum transparency and availability
The data and inventory management of products and consumables involves a considerable amount of administrative work.
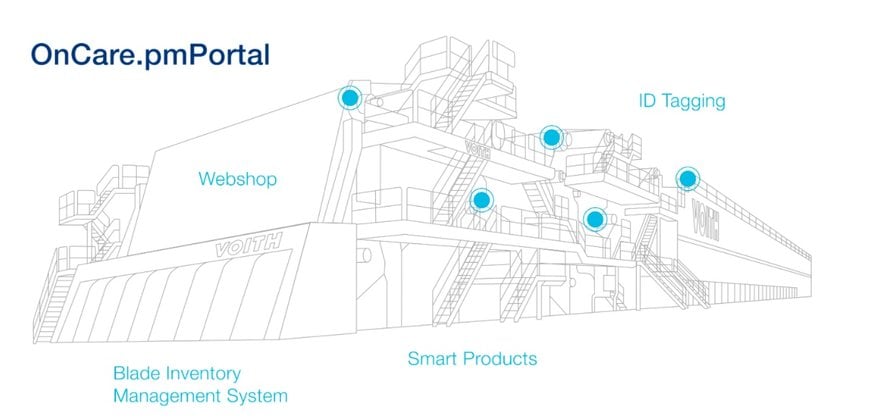
The Voith OnCare.pmPortal allows paper manufacturers to use a central data and automated inventory management system for the proactive planning of maintenance periods and downtimes.
The new digital asset management tool OnCare.pmPortal now offers paper manufacturers an optimum alternative for increasing both the transparency of product data and the efficiency of the procurement system, while also facilitating the planning of maintenance periods and downtimes and increasing plant availability. Thanks to a direct connection to the Voith Paper Webshop, registered components can be reordered quickly, easily and without any risk of confusion.
- Maximum transparency of product data, run times and inventories
- Optimally planned maintenance periods and downtimes
- Rapid reordering of registered components via the Voith Paper Webshop
With the OnCare.pmPortal, Voith has developed a powerful asset management tool that simplifies central data management and gives paper manufacturers an overview of key products and consumables in their paper machine. This facilitates optimized documentation of activities such as maintenance, repair and replacement, and simplifies data maintenance.
Richard Birkhold, Global Product Manager Asset Management at Voith
"Every day, I coordinate maintenance measures and control numerous processes," says Karl-Josef Uhlemann, maintenance manager for rolls at Schoellershammer in Germany. "With the digital inventory management tool, I can now manage consumables and rolls centrally and access the data at any time and from any place."
The OnCare.pmPortal now starts with two modules: The automated data recording of rolls and fabrics, as well as the digital inventory management of doctor blades. These product groups are automatically identifiable in the OnCare.pmPortal by means of a digital nameplate and do not require manual entry in the system.
ID tagging for rolls and fabrics: For constant visibility of product data and run times
The ID tagging module for rolls and fabrics is a combination of contactless, radio-based connection technologies and the integration of digital nameplates based on proven industry standards. The solution offers simple, user-friendly tagging of rolls and fabrics and enables seamless identification through the scan of a digital nameplate.
Regardless of the technology standard, the ID tags can be read with a smartphone and the corresponding Voith app and managed in the OnCare.pmPortal. The mobile application grants access to all product data, at any time and from any location, for efficient tracking of the product history and optimized documentation of activities such as maintenance, repair and replacement.
Thanks to the combination of OnCare.pmPortal and the ID tagging module, I can identify a product directly via the digital nameplate or search the database. The mobile application with its intuitive interface provides a quick and easy overview of product information and important product lifecycle data.
Karl-Josef Uhlemann, maintenance manager for rolls at Schoellershammer.
Blade Inventory Management System: Digital control of inventory data and fully automated management of inventories
With the help of the Blade Inventory Management System module, the operator no longer has to worry about ordering doctor blades or the associated stock control and supply chains. This is made possible with an ID tag on the packaging of the doctor blades. New doctor blades are automatically reordered and delivered by the system as soon as the stock in the warehouse reaches a minimum, individually defined level.
As soon as the new blades arrive in the customer warehouse or existing blades are removed from the warehouse, the stock is updated in the OnCare.pmPortal and can be accessed from there at any time, thus increasing inventory traceability and transparency. At the same time, there is no need to maintain inventory lists or carry out inventory controls. As a result, the OnCare.pmPortal not only reduces the outlay and costs associated with inventory management, but also increases its efficiency by using automated and digitized processes.
Voith plans to extend ID tagging to additional consumables and components in the near future and, in doing so, will offer paper manufacturers an even more powerful tool.
www.voith.com