www.industryemea.com
25
'21
Written on Modified on
Flexibility in motion with the new Delta AX-8 series
With the introduction of the new AX-8 series, Delta has extended its capabilities in motion control. Thanks to the embedded multi-core technology and real-time extension, this powerful IPC controller based on the CODESYS platform guarantees high performance in a compact fan-less design.
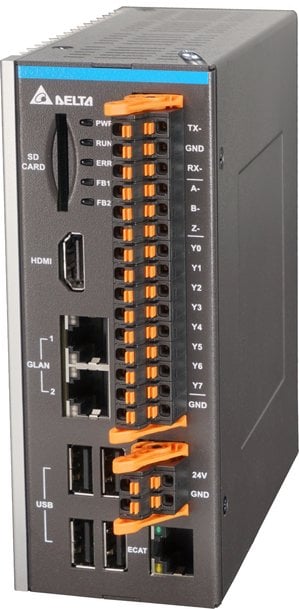
Over the last 30 years, the role of industrial PCs in machine automation has evolved constantly.
They started as simple service devices, mainly dedicated to interfacing, supervising and data collecting activities, IPCs have assumed a central role in the control of the machines.
Thanks to the evolution of HW technology, today they offer improved reliability: this, along with increased shock and vibration resistance, a lack of rotating parts, and solid-state memory storage devices, have all become essential in modern industrial environments. The subsequent advent of real-time extensions and multi-core processors gave industrial PCs the capability to control automated machines and, at the same time, maintain the flexibility provided by standard operating systems. This enabled machine builders to benefit from the increased performance of last generation CPUs to fulfill the requests of the most demanding applications.
Delta’s AX-8 series is all of that, and much more.
IPC architecture to enhance performance and flexibility
The AX-8 is a powerful industrial PC series, equipped with the Windows 10 IoT operating system. The embedded Intel J1900 Quad Core processor offers optimal performance and ensures low power consumption in a compact, fan-less format. Despite its small size (54.2×141×137.5 mm), it includes a wide range of interfaces: three independent 1Gbps Ethernet ports, four USB ports, one HDMI and an SD card slot to provide additional memory storage for data backup. Comfortable push-in connectors give easy access to the power supply and the additional I/O port, which includes 16 DI/DOs, incremental and SSI encoder interfaces and RS422/485 serial port.
Thanks to the CODESYS platform and its embedded real-time extension, the AX-8 becomes a powerful motion controller able to control up to 64 axes through the embedded EtherCAT interface. PLC, Motion Control and Windows OS can live on the same device without affecting each other’s performance. Users can also leverage the flexibility of a standard operating system; for example, installing 3rd-party SW tools or running HMI applications on the AX-8 itself.
DIADesigner-AX: the Delta CODESYS-based engineering platform
With the new AX-8 series, Delta has adopted the well-known SW automation suite CODESYS, which is now integrated into the DIAStudio environment.
This new powerful tool, called DIADesigner-AX, offers many advantages for users and developers:
• Standard programming. It meets international standards like IEC61131-3 for PLC programming and PLCopen for motion control programming. All IEC languages are supported, from ladder to structured text, including the support of Object Oriented Programming (OOP).
• Integrated commissioning tools like digital oscilloscope, data monitoring, breakpoints, diagnostics, online changes.
• Simulation mode to test PLC/motion programs without physical target devices
• Planning and execution of both simple and complex applications for motion control, including single-axis and multi-axis movements in accordance with PLCopen standard
• Integrated graphical interface to create electronic cams
• Planning and execution of CNC and robotics applications
DIADesigner-AX keeps the typical project tree structure of CODESYS projects: PLC programming, Task Configuration, hardware configuration and all the other functionalities can be accessed in the same environment. This dramatically reduces the learning time, helping users to develop a complete motion control project quickly.
In addition, DIADesigner-AX includes some special graphical tools for hardware, network and axis configuration to make the user experience even more user-friendly.
Designed for motion
The AX-8 Series, in combination with the DIADesigner-AX engineering platform, represents a complete solution for motion control applications. The support for PLCopen standard (part 1, 2 and 4) makes it suitable for both single and multi-axis movements and provides a clear benefit for users in terms of SW reusability.
Electronic cams can be designed by the integrated graphical editor, or can be created and modified directly in the PLC program. This is an essential requirement for high-end packaging machines.
The CNC+Robotics package extends the operating range of AX-8 series. The standard DIN66025 G-code interpreter provides the ability to interpolate axes and, together with functions like tool length and tool radius compensation, enables users to build CNC applications.
Thanks to the supported kinematic transformations (SCARA, Cartesian, Tripod and many others), there’s no need to use external dedicated robot controllers anymore: robots, servo drives, inverters, I/O modules and all the machine’s other devices are controlled in the same project, which leads to clear advantages in terms of efficiency, flexibility and production capacity.
Extensive fieldbus support
One of the most useful features of the AX-8 series is the wide support of fieldbus technologies and communication protocols.
The integrated EtherCAT interface allows high-speed control of Delta field devices, such as the AC Servo Drive ASDA-A3-E, ASDA-B3-E, ASDA-A2-E Series, High Performance Compact Drive MH300 Series, Compact Drive MS300 Series, General Vector Control Drive C2000 Plus Series and R1-EC, R2-EC Series and DVP remote I/O modules. No restrictions are placed upon the use of other EtherCAT slaves; by importing the ESI file provided by the manufacturers, AX-8 can easily control 3rd-party devices.
For the connection with other devices, the machine-to-machine data exchange or the communication with the upper levels of the automation hierarchy, the AX-8 series offers Modbus TCP/RTU and Ethernet/IP.
The integrated OPC UA Server is robustly connected to the PLC program and allows users to browse, read and write variables. Thanks to the encrypted communication (in accordance with OPC UA profile Basic256SHA256), it provides an intrinsically secure way to exchange data with other devices, as well as databases, MES and ERP systems, which makes this solution ready for Industry 4.0. User management is also supported: different users (each one with their own credentials) can be created, making the project administrator able to assign specific variable sets to the different groups.
HMI options
Traditionally, HMI applications run on dedicated operator panels like the Delta DOP-100 series. The new DIAScreen tool by DIAStudio makes the PLC-HMI tag sharing very simple. The users select the PLC variables to share, and those variables become accessible in the HMI engineering platform by symbol. There’s no need to consider variable addresses anymore, which leads to clear benefits during SW development.
Additionally, AX-8 series also includes HMI runtime. The HMI application developed in DIAScreen can be downloaded to the AX-8 on top of the operating system. Connecting touchscreen or standard monitors to the HDMI interface, the AX-8 will be in charge of PLC, Motion and HMI functions, making it a genuine “all-in-one” solution.
Advanced users can also develop their own HMI applications in high-level languages like C#, C++, VB.NET or Python. In fact, the AX-8 series provides fast and convenient methods to access PLC variables.
Applications
The Delta AX-8 series can fulfill your demands across a wide range of applications in many different market segments, such as packaging, woodworking, metalworking and material handling. Flow pack machines, labelling machines, palletizers, as well as CNC milling machines, assembly and robotic pick & place applications, are just some examples of how it can be utilised.