www.industryemea.com
06
'21
Written on Modified on
Kennametal Introduces First Stellite Powder For Laser Powder Bed Additive Manufacturing
Stellite 21 AM powder unlocks the superior wear and corrosion resistance of the Stellite alloy family for additive applications in oil and gas, power generation and beyond
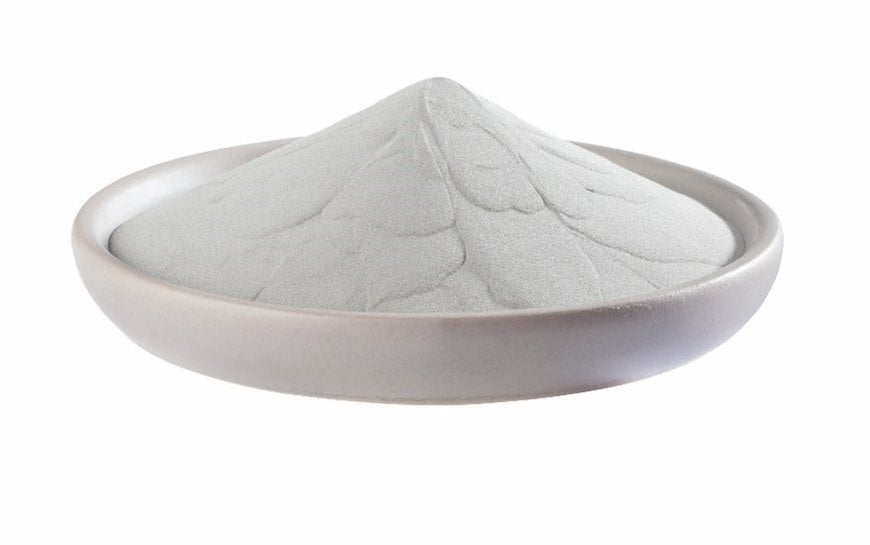
Kennametal’s new Stellite 21 AM metal powder (shown here) unlocks the superior wear and corrosion resistance of the Stellite alloy family for laser powder bed additive applications in oil and gas and power generation.
Kennametal Inc. (NYSE: KMT) announced today the launch of Stellite 21 AM powder, the first Stellite powder qualified for laser powder bed additive manufacturing, and the latest addition to Kennametal Additive Manufacturing’s portfolio of high-performance metal powders optimized for 3D printing. With Stellite 21 AM powder, the unique corrosion and wear-resistant properties of the Stellite alloy family are now available for laser powder bed additive platforms to produce high-performance wear components for the oil and gas and power generation industries. Kennametal Additive Manufacturing is the Company’s 3D printing and production business unit within its Infrastructure segment.
“Kennametal Additive Manufacturing is drawing on our longstanding expertise in metal powder production to help our customers leverage the advantages of 3D printing and make better parts, faster and more efficiently,” said Sam Lomasney, Marketing Portfolio Manager, Kennametal. “The addition of Stellite 21 AM powder to our portfolio of high-performance cobalt, nickel and iron powders is another proof point of how we continue to innovate in materials for additive manufacturing.”
The business drew on deep expertise in metal powder production for hard facing and thermal spray applications to develop Stellite 21 AM powder. It is available direct to customers for use in their own 3D printing applications or in combination with Kennametal’s end-to-end additive production capabilities to make fully finished components.
Valued for its superior wear and corrosion resistance, the Stellite 21 alloy has a long history of success in traditional manufacturing applications in the oil and gas, power generation and aerospace industries. Stellite 21 AM powder enables customers to achieve similar wear and corrosion resistance properties in additively manufactured parts. It is ideally suited for flow control applications and can be integrated into complex designs to mitigate cavitation, erosion, or corrosion failures.
The new powder’s composition features a Cobalt Chrome Molybdenum alloy matrix, containing dispersed hard carbides which strengthen the alloy and increase its hardness while decreasing the material’s ductility. It also has excellent corrosion and thermal shock and mechanical shock resistance.
Kennametal Additive Manufacturing offers comprehensive 3D printing solutions, from raw material to finished part. It utilizes gas atomization powder production capabilities to supply cobalt, nickel and iron powders optimized for specific additive manufacturing processes. In addition to the new Stellite 21 AM powder, the business also recently added Delcrome 17-4 AM and Delcrome 316L AM powders for direct metal laser sintering (DMLS) systems to its portfolio of additive powders. At its research and development, prototyping and production center in Latrobe, Pennsylvania, Kennametal Additive Manufacturing utilizes laser powder bed and binder jet printing technologies, combined with post-print processing capabilities, including sintering, hot isostatic pressing and machining, to produce fully finished wear components. These include parts printed with powders specifically designed for 3D printing, including Kennametal KAC89 tungsten carbide and Stellite 6 AM, a wear resistant cobalt-chrome alloy.