www.industryemea.com
17
'21
Written on Modified on
IT’S ALL ABOUT ZERO-WASTE IN THE FACTORY OF THE FUTURE
Whatever your opinion on climate change there is one thing virtually everybody agrees on, and that is that waste is a bad thing. Waste can take many forms, excess energy utilisation, wasted products, wasted time, or wasted resources like water. All this adds up to not only excess cost and reduced competitiveness but also unnecessary burden on the planet and the natural world.
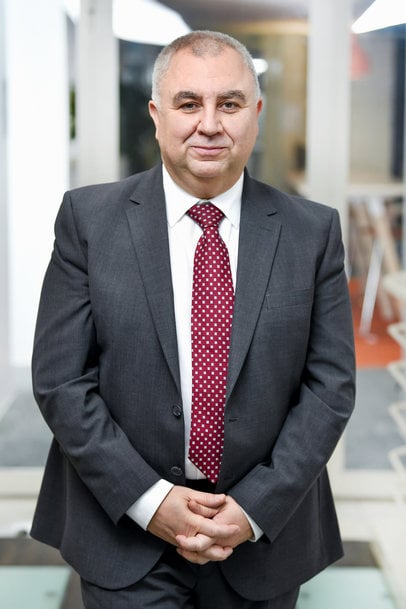
For decades, experts have warned of the impact climate change has on the planet, many chose to ignore it. However, in recent years, the focus has shifted to expose how some company operations, in particular manufacturing processes, contribute towards global warming. In the US for example, the U.S. Environmental Protection Agency reports that in 2018, industry accounted for 22% of U.S. GHG emissions, compared to 12% for residential and commercial. Food waste emissions are also high. One quarter of emissions (3.3 billion tonnes of CO2eq) from food production ends up as wastage either from supply chain losses or consumers . It is essential to understand that to reduce emissions we need to prevent food waste.
Recognising the need for action, leading companies in the food and beverage manufacturing sector are rethinking the way their factories operate and finding innovative solutions to reduce their waste.
When we think about the ‘Factory of the Future’, we may imagine robots and virtual reality headsets in every corner, with few or no human workers. This is a concept from the past. On the contrary, the factory of the future is one where the integrated application of decarbonization measures, through innovative and data-driven solutions, reduces net emissions to zero, and ‘zero waste’ becomes the norm. Zero waste not only refers to carbon and energy emissions, but also wastage of water, raw materials, product, and time.
Zero waste needs to be a common goal for many, and if it is going to work, the factory of the future must be centred around the concept of ‘circular manufacturing’, where responsible production is driven by two key areas: digitalisation and flexibility.
Unlocking the power of the human workforce
Zero waste cannot be achieved without rethinking manufacturing operations. But it is not man vs machine. Instead, we should be looking at how machine or technology can empower workers to improve operational efficiencies, supply chain planning and costs.
By equipping manufacturers with the right tools, the workforce has the ability to oversee their operation lines seamlessly, allowing them to make more informed decisions and engage with their product more holistically. In turn plant managers will clearly see which lines are performing inefficiently in real time or predict a breakdown before it occurs, and now artificial intelligence and machine learning can provide the information to make decisions quickly to mitigate these losses.
As equipment becomes more technically advanced, modern plants require ever-higher worker knowledge, which calls for more and better skills and knowledge sharing. This is key to higher plant uptime and productivity. There is a growing need for workers to share knowledge and collaborate across sites. But the good news is that staff have a strong appetite for flexible on-the-job learning, at their own pace and point of need. Digital Industry 4.0 solutions now make this possible.
With a digital and data-first approach, manufacturers can also be more efficient in how they test a product. A lot of time currently goes into testing products in the factory before they reach the shelves for customers and often these products are disposed of as waste. By automating some of this process, we can reduce the length of time it takes to test, as well as the number of products that would be thrown away.
Is it possible to predict future customer demand?
Data-led insights have helped us improve how we predict changing customer demands change over time. This has facilitated a shift towards having more flexible production lines. The benefit of product flexibility and customisation is the ability for factories to cope with the growing product variety, the desire for personalisation while ensuring optimised system performance. However, for customised product to be readily available, the factory of the future needs to be able to produce mass customised products at the cost of mass production. In essence manufacturing and supply chains will become more ‘on demand’. The introduction of mass customisation enables factories to work towards a more ‘circular manufacturing’ process, by only producing what will be used and eliminating as much waste as possible.
An example of this in action can be seen with an American juice producer that adopted a customised total maintenance program. The result was a 60%-65% improvement in OEE (Overall Equipment Effectiveness), a ~10% reduction in operational cost savings and more than 5% in waste reduction.
Another element of waste reduction could be for more manufacturers to consider is the use of second-hand equipment. Most people would not think twice about buying a second-hand automobile. Similarly in the mining industry, once they have finished using a vehicle, it is not scrapped, but instead sold to another buyer to reuse. This circularity of equipment and machinery means less waste.
Say no to waste
In manufacturing, anything that does not create value is considered a loss. For factories to archive zero waste, manufacturers need to find innovative ways to eliminate any kind of waste whether it be time or excess products. However, first they need to adopt a zero-waste mindset. Both technology and human workers will exist in harmony in the factory of the future – now, we need to understand how digital tools can enable humans to be more efficient, less wasteful, and productive.
www.tetrapak.com