www.industryemea.com
06
'21
Written on Modified on
NSK Life-Lube® bearings drive cost-saving improvements in food plants
NSK’s Life-Lube® bearing units are proving increasingly popular in the food and beverage industry, and with good reason. These advanced bearings combine the corrosion-resistant properties of Silver-Lube® housings with the excellent sealing and lubricating properties of Molded-Oil inserts. Life-Lube® units are specifically for use in sectors where contact with water and process fluids is unavoidable, and where excellent chemical resistance and long lubrication life are primary requirements. By taking advantage of the benefits available, food and beverage plants can tap into considerable savings from reduced downtime and maintenance costs.
Astute design engineering means Life-Lube® bearing units (comprising a housing and bearing insert) are adept at withstanding the often harsh operating conditions of food and beverage plants, while simultaneously preventing any contamination of the processing environment to meet strict hygiene regulations.Corrosion resistance
Primary among the design considerations is the unit’s housing material: thermoplastic polyester (PBT), which is highly resistant to corrosion. In conjunction with Molded-Oil bearing inserts and nitrile rubber seals, this design guarantees good chemical resistance and long service life.
In particular, the polymer housing not only eliminates any risk of contamination from painted or coated surfaces, but its smooth finish prevents dirt adhesion and reduces wash-down time. Complementing the housing is the stainless steel insert, which delivers improved corrosion resistance for wet environments. Moreover, the Molded-Oil insert cavity contains a lifetime of lubricating oil and polyolefin resin that means no re-lubrication is required for the lifetime of the product.
Another important feature for the food and beverage industry is the flinger seal, which prevents the ingress of bacteria and protects the Molded-Oil filled cavity. There is also no potential for lubricant leaks.
Bacteria-free
NSK has taken great care to ensure the design of its Life-Lube® bearing units are free of crevices and ‘bug traps’ that could harbour mould or bacteria. As a result, the bearings are ideal for food manufacturing environments that involve dust (dry or wet), water (spray or submerged) and wet abrasive contamination, as well as temperatures up to 80°C. Life-Lube® bearing units are also suitable for use in some starch-based environments, as well as those involving low temperatures, down to -18°C.
The suitability of Life-Lube® bearing units for food applications is vast, encompassing tasks that include primary (cutting and mixing), secondary (moulding), conveying, inspection, heating and packaging processes, while beverage applications include bottle moulding, filling, sealing, inspection and packing. In these operating environments, Life-Lube® will resist excessive moisture, washdown chemicals and contamination, all while operating at continuous high speeds if required. The speed factor is maximal dn = 12 x 104 ( dn =bore diameter in mm x speed in rpm).
Substantial savings
A major snack food producer is among those now taking advantage of Life-Lube® bearing units. Previously, the company was experiencing frequent bearing failures on its cutter line, so it requested the assistance of NSK to help reveal the root cause.
NSK analysed the failed bearings and reviewed the application as part of its AIP Added Value Programme. By following a process map survey of the site, it was evident that extensive grease washout had been taking place following production line washdowns. To help keep the line running and avoid costly unplanned downtime, the plant was replacing the bearings every six weeks as part of preventative planned maintenance, but failures would often occur beforehand.
NSK engineers recommended replacing the existing bearings with Life-Lube® housed units, commencing a trial on one production line. One year later, the units were still performing well with no failures, delivering substantial annual cost savings in maintenance labour, replacement bearings and lost production time. Due to this success, the food plant is currently adopting Life-Lube® bearing units on its two other production lines.
Today, the plant enjoys many other benefits of Life-Lube® bearing units, which include a spherical housing seat and spherical outer ring that allows for any initial misalignment on mounting, and the availability of various locking methods as standard to ensure close-fit shaft mounting. In addition, quiet and efficient running comes courtesy of super-finished raceways.
This success story is one of an increasing number across the food and beverage industry, where plants are discovering that the combination of thermoplastic housing, special nitrile rubber seals, stainless-steel bearing material and Molded-Oil lubricant makes the Life-Lube® range ideal for wet and/or contaminated environments.
1) NSK’s Life-Lube® bearing units are ideal for many food plant applications, including cutting lines. Photo: alterfalter/Shutterstock
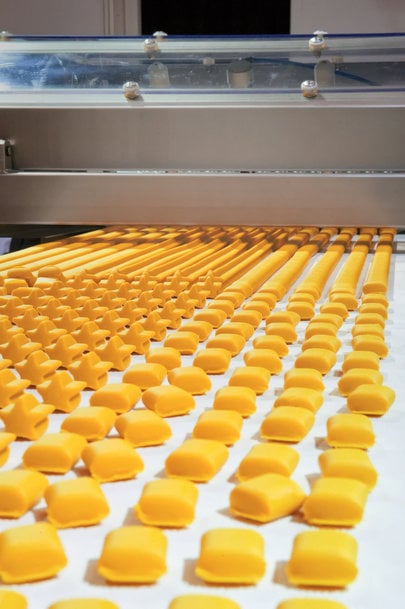
2) A cutaway section of an NSK’s Life-Lube® bearing unit, showing the stainless steel insert and Molded-Oil lubrication. Photo: NSK
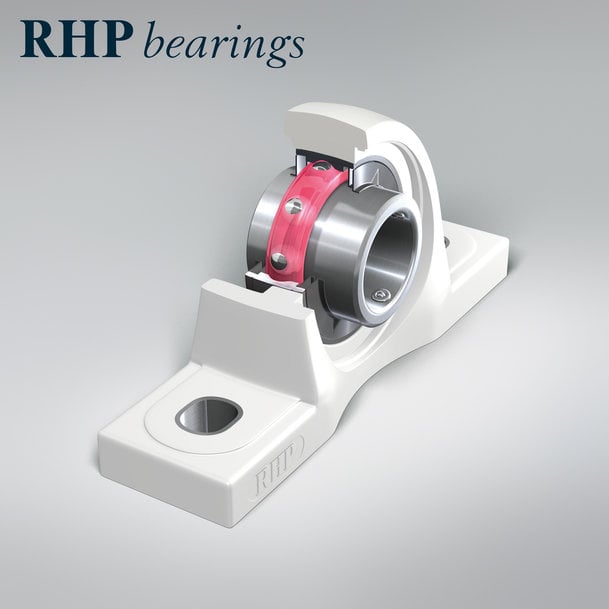
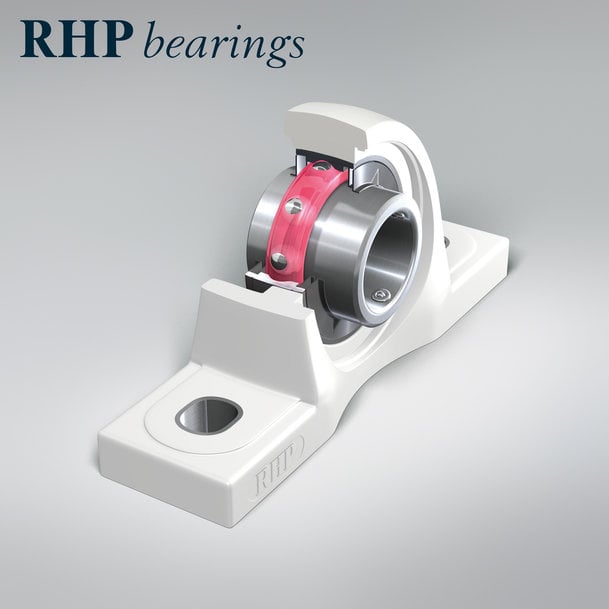