www.industryemea.com
05
'22
Written on Modified on
Leifeld Metal Spinning: Patented process for rim fabrication opens up new possibilities for wheel manufacturers
It’s similar to throwing on a pottery wheel – Leifeld Metal Spinning GmbH has developed a new machine for manufacturing rims using a flow forming process, which, for the first time ever, also works with internal rollers: instead of hands, rollers are used to shape the inside and outside surfaces. Because the process works without tools, the user has maximum flexibility and can even economically produce lot sizes of one with the Leifeld WSC Flex.
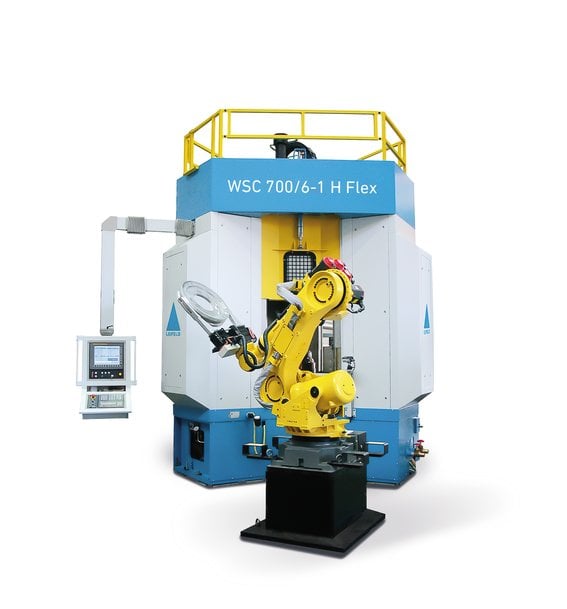
The new Leifeld WSC 700/6-1 H FLEX enables an increase in production efficiency of at least 15 percent, as well as energy savings of about 10 percent.
Efficient Wheel Manufacturing Reaches a New Level.
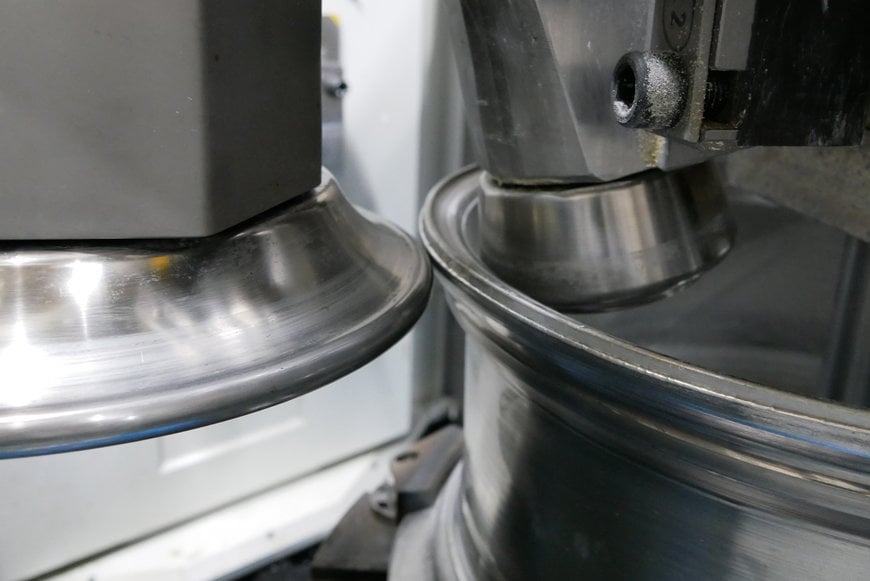
The machine is equipped with independently controllable rollers.
“Market developments and our own standards are continuing to drive the flow forming process,” says Oliver Reimann, CEO of Leifeld Metal Spinning GmbH. The global market leader from Ahlen in Germany develops machine tools for chipless metal forming that are used in the automotive, aerospace, energy, and other industries and in diverse industrial applications around the world. The CEO especially sees trends in the automotive industry. Growing design complexity and increasing wheel size along with increasing variant variety and rising cost pressures are only a few of many arguments that speak in favor of using the Leifeld WSC Flex. For manufacturers of aluminum wheels, the patented technology is a real sensation. It offers far-reaching potential in wheel manufacturing for improving productivity, lowering cost, and thus creating relevant competitive advantages for OEMs and after sales wheel manufacturers.
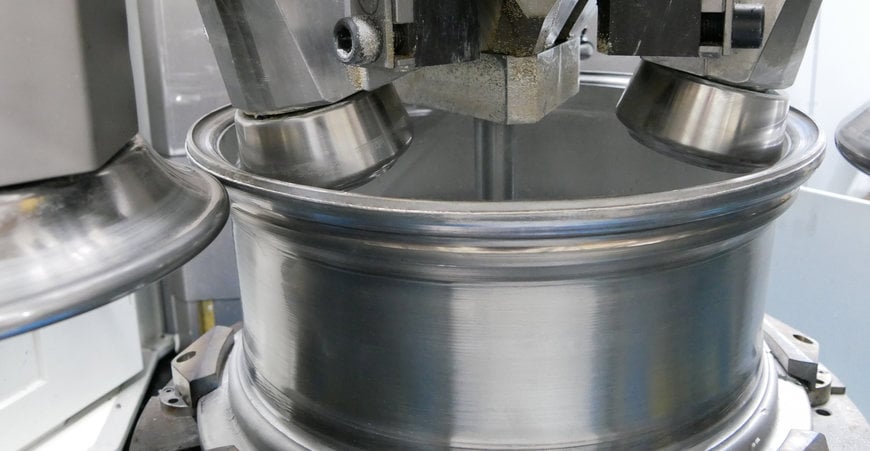
The angle adjustment of the internal rollers is performed automatically according to the offset and wheel size.
“Manufacturers must be able to react to these market developments with efficient solutions,” says Oliver Reimann. Thanks to this novel technology, the flow forming process is gaining relevance for wheel manufacturing. “With our market-leading technologies and machines, we can form vehicle rims from cast aluminum in such a way that they are considerably lighter than conventional wheels and at the same time stronger,” promises Benedikt Nillies, Technical Director at Leifeld. With wheels formed in this way, manufacturers can meet the legal requirements for reduction of CO2 emissions more easily. Lower weight means greater range, i.e., less fuel or energy consumption.
Additional Material Thickness Reduction Thanks to Higher Strength
Aluminum rims are often cast or forged as single pieces. The flow forming process improves the material’s grain structure, which significantly increases the final rim strength after heat treatment. “We have the possibility of reducing the material cross section at certain points and flexibly adapting it to the load requirements of the wheels,” says Nillies. “With this process, we achieve a better grain structure.” The resultant increase in strength makes it possible to reduce the material thickness even further. Wall thicknesses and wheel geometries can be optimally adapted to the wheel requirements – this allows for flexible wheel design and maximum weight savings.
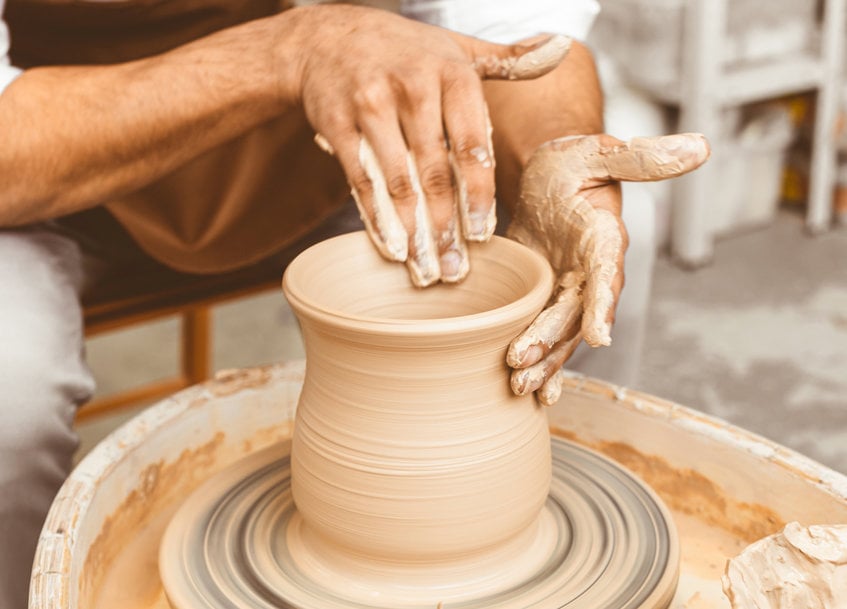
The new toolless process is reminiscent of throwing on a pottery wheel. The forming hands are similar to the axially and radially moving internal and external rollers.
Flexibility Without Tools
“How can we support our customers even better in reacting to market trends such as increasing variety or just-in-time production with a high level of flexibility? That is what we asked ourselves here in the team,” says Sales Director Harald Knechtel. Leifeld’s response was to revolutionize the well-known flow forming process. “Our patented Leifeld WSC Flex technology works without tools,” says Harald Knechtel: “The principle is a little like throwing pottery. The forming movement of the hands is similar to the axial and radial movements of the internal and external rollers.”
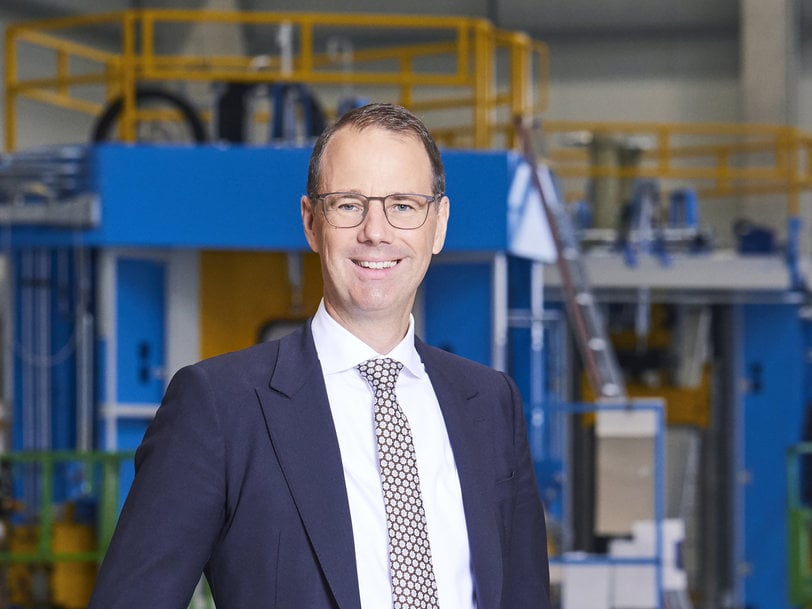
Oliver Reimann, CEO of Leifeld Metal Spinning: “The market developments and our own standards are continuing to drive the flow forming process.”
With the process, the user has great flexibility and can produce different rim diameters, profiles, wall thicknesses, and rim widths. Whereas classic flow forming uses one tool per rim type, the new Leifeld WSC Flex uses no tools whatsoever. There are thus no setup times and no product-specific tooling costs during operation. Tooling procurement costs, storage, and repair are eliminated completely. As a result, production factors are used economically and efficiently and lean production can be realized. The user can carry out product changes seamlessly without having to perform disruptive setup activities. “With a standard machine, two to three setup operations are performed on average per day, with each setup operation potentially taking about 1.5 hours due to the preheating of the tools and startup of production,” says Harald Knechtel. “Through the use of the multifunctional chuck, our new process is especially suitable for High-Mix Low-Volume Manufacturing.”
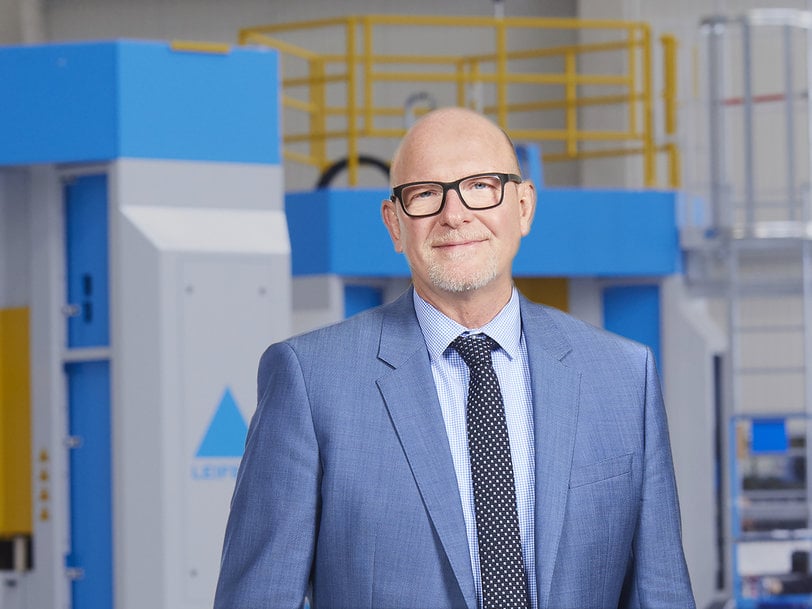
Harald Knechtel, Sales Director at Leifeld: “With these advantages, our new process is suitable for chaotic production with lot sizes of one and up.”
Profitable Right Down the Line
Leifeld offers the WSC Flex with various workpiece changeover concepts and with different numbers of rollers, depending on customer-specific performance requirements. The cycle times of the new machine are comparable to those of tool-bound machines. One function that was previously not available allows a completely cylindrical region to be formed with the new process for improved wheel stability. “Our WSC Flex technology is a world first with high market potential. Our customers will achieve an efficiency increase of at least 15 percent, as well as energy savings of about 10 percent,” says Sales Director Harald Knechtel. “We have concentrated primarily on customers that manufacture cast wheels. The new process also offers numerous advantages for manufacturing of forged vehicle wheels.” With the WSC Flex technology from Leifeld, the user can chaotically process 18- to 24-inch wheels starting at lot size one.
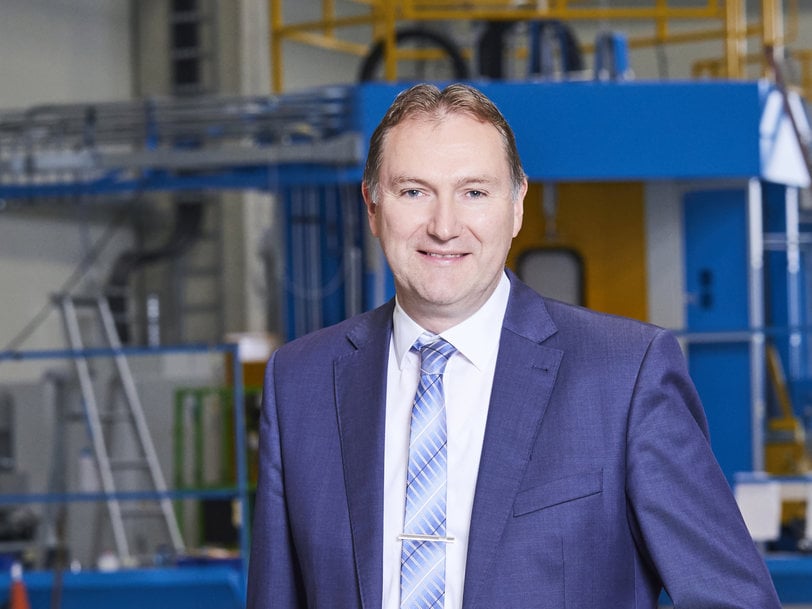
Benedikt Nillies, Technical Director at Leifeld: “With the flow forming process, we achieve a better grain structure and improved strength.”
CEO Oliver Reimann is pleased with the positive market resonance: “The patented Leifeld WSC Flex takes its place as another innovation in our portfolio. The wheel industry is finally capable of flexibly flow-forming rim profiles that up to now could only be made with expensive tools and increased efforts.”
www.leifeldms.com
Efficient Wheel Manufacturing Reaches a New Level.
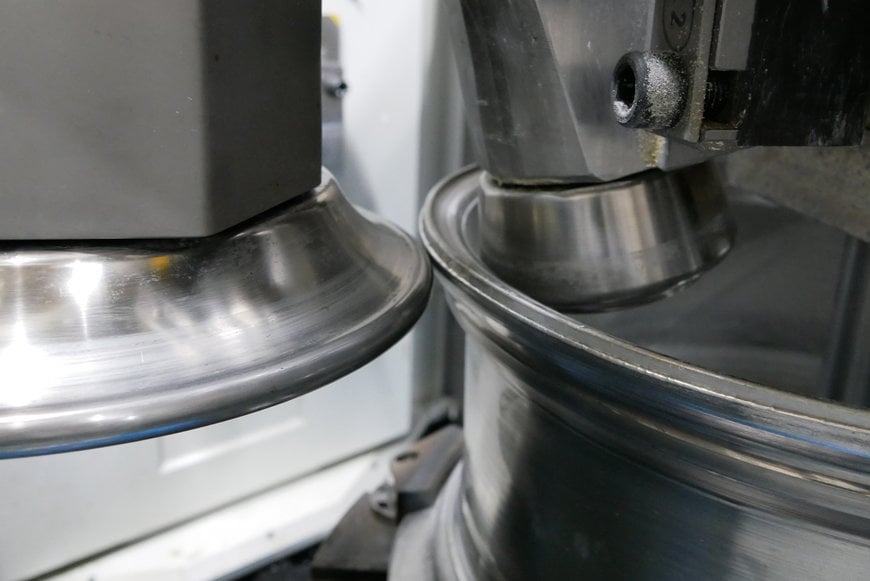
The machine is equipped with independently controllable rollers.
“Market developments and our own standards are continuing to drive the flow forming process,” says Oliver Reimann, CEO of Leifeld Metal Spinning GmbH. The global market leader from Ahlen in Germany develops machine tools for chipless metal forming that are used in the automotive, aerospace, energy, and other industries and in diverse industrial applications around the world. The CEO especially sees trends in the automotive industry. Growing design complexity and increasing wheel size along with increasing variant variety and rising cost pressures are only a few of many arguments that speak in favor of using the Leifeld WSC Flex. For manufacturers of aluminum wheels, the patented technology is a real sensation. It offers far-reaching potential in wheel manufacturing for improving productivity, lowering cost, and thus creating relevant competitive advantages for OEMs and after sales wheel manufacturers.
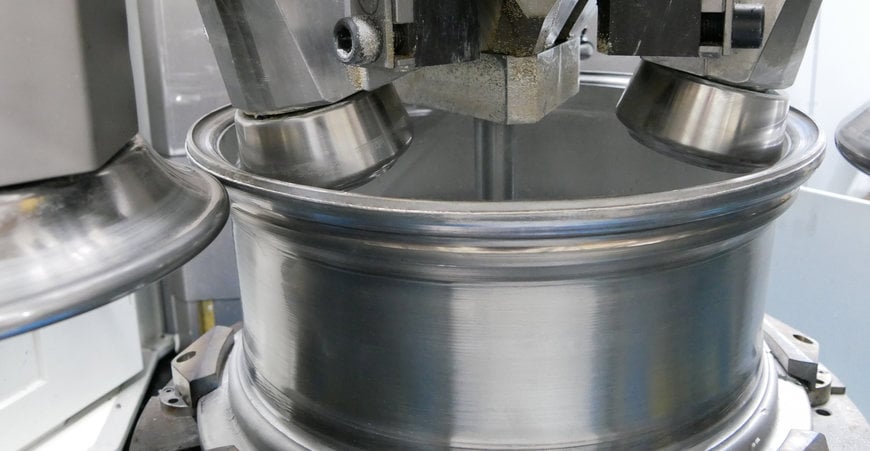
The angle adjustment of the internal rollers is performed automatically according to the offset and wheel size.
“Manufacturers must be able to react to these market developments with efficient solutions,” says Oliver Reimann. Thanks to this novel technology, the flow forming process is gaining relevance for wheel manufacturing. “With our market-leading technologies and machines, we can form vehicle rims from cast aluminum in such a way that they are considerably lighter than conventional wheels and at the same time stronger,” promises Benedikt Nillies, Technical Director at Leifeld. With wheels formed in this way, manufacturers can meet the legal requirements for reduction of CO2 emissions more easily. Lower weight means greater range, i.e., less fuel or energy consumption.
Additional Material Thickness Reduction Thanks to Higher Strength
Aluminum rims are often cast or forged as single pieces. The flow forming process improves the material’s grain structure, which significantly increases the final rim strength after heat treatment. “We have the possibility of reducing the material cross section at certain points and flexibly adapting it to the load requirements of the wheels,” says Nillies. “With this process, we achieve a better grain structure.” The resultant increase in strength makes it possible to reduce the material thickness even further. Wall thicknesses and wheel geometries can be optimally adapted to the wheel requirements – this allows for flexible wheel design and maximum weight savings.
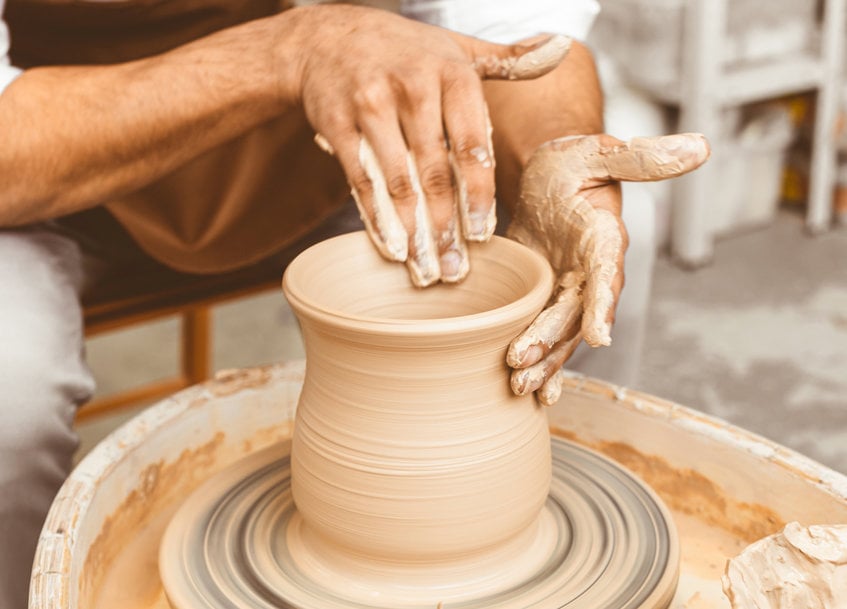
The new toolless process is reminiscent of throwing on a pottery wheel. The forming hands are similar to the axially and radially moving internal and external rollers.
Flexibility Without Tools
“How can we support our customers even better in reacting to market trends such as increasing variety or just-in-time production with a high level of flexibility? That is what we asked ourselves here in the team,” says Sales Director Harald Knechtel. Leifeld’s response was to revolutionize the well-known flow forming process. “Our patented Leifeld WSC Flex technology works without tools,” says Harald Knechtel: “The principle is a little like throwing pottery. The forming movement of the hands is similar to the axial and radial movements of the internal and external rollers.”
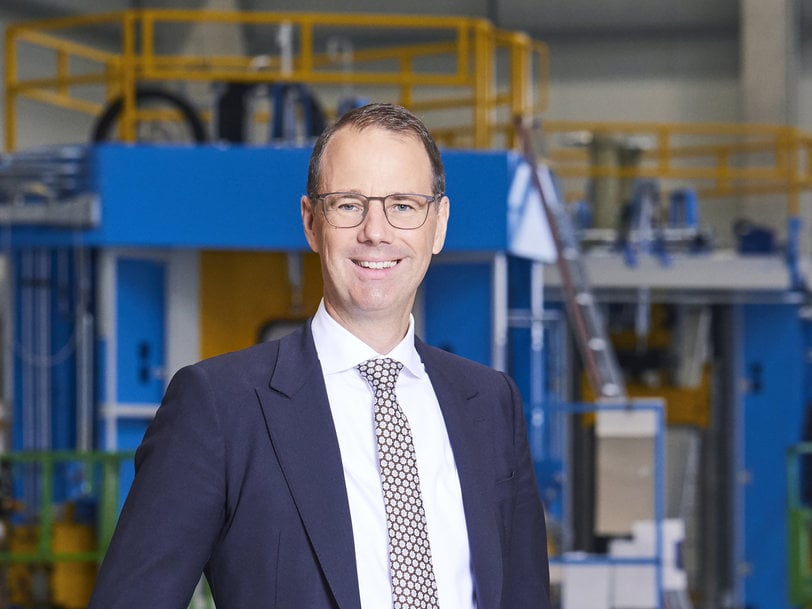
Oliver Reimann, CEO of Leifeld Metal Spinning: “The market developments and our own standards are continuing to drive the flow forming process.”
With the process, the user has great flexibility and can produce different rim diameters, profiles, wall thicknesses, and rim widths. Whereas classic flow forming uses one tool per rim type, the new Leifeld WSC Flex uses no tools whatsoever. There are thus no setup times and no product-specific tooling costs during operation. Tooling procurement costs, storage, and repair are eliminated completely. As a result, production factors are used economically and efficiently and lean production can be realized. The user can carry out product changes seamlessly without having to perform disruptive setup activities. “With a standard machine, two to three setup operations are performed on average per day, with each setup operation potentially taking about 1.5 hours due to the preheating of the tools and startup of production,” says Harald Knechtel. “Through the use of the multifunctional chuck, our new process is especially suitable for High-Mix Low-Volume Manufacturing.”
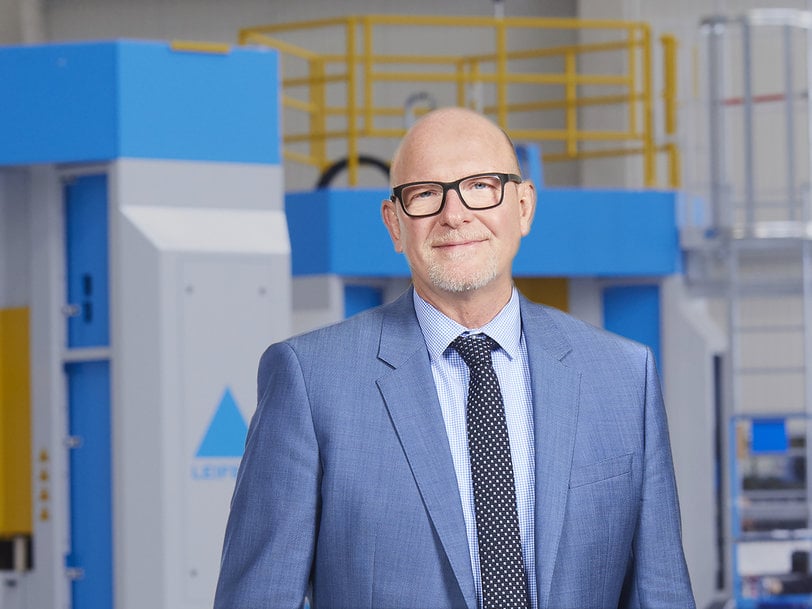
Harald Knechtel, Sales Director at Leifeld: “With these advantages, our new process is suitable for chaotic production with lot sizes of one and up.”
Profitable Right Down the Line
Leifeld offers the WSC Flex with various workpiece changeover concepts and with different numbers of rollers, depending on customer-specific performance requirements. The cycle times of the new machine are comparable to those of tool-bound machines. One function that was previously not available allows a completely cylindrical region to be formed with the new process for improved wheel stability. “Our WSC Flex technology is a world first with high market potential. Our customers will achieve an efficiency increase of at least 15 percent, as well as energy savings of about 10 percent,” says Sales Director Harald Knechtel. “We have concentrated primarily on customers that manufacture cast wheels. The new process also offers numerous advantages for manufacturing of forged vehicle wheels.” With the WSC Flex technology from Leifeld, the user can chaotically process 18- to 24-inch wheels starting at lot size one.
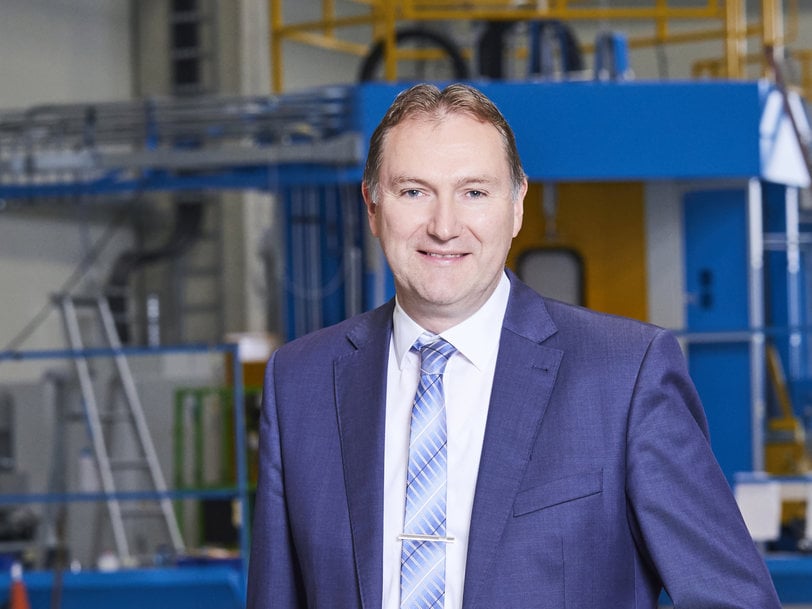
Benedikt Nillies, Technical Director at Leifeld: “With the flow forming process, we achieve a better grain structure and improved strength.”
CEO Oliver Reimann is pleased with the positive market resonance: “The patented Leifeld WSC Flex takes its place as another innovation in our portfolio. The wheel industry is finally capable of flexibly flow-forming rim profiles that up to now could only be made with expensive tools and increased efforts.”
www.leifeldms.com