Self-contained actuator for a variety of applications
Bosch Rexroth has expanded its range of standardized self-contained actuators by adding the CytroMotion system solution. With the help of the new compact actuator, linear movements involving forces of up to 110 kN can be achieved in a range of machines and systems in smaller spaces, more efficiently and more sustainably. These benefits can be seen over the entire life cycle.
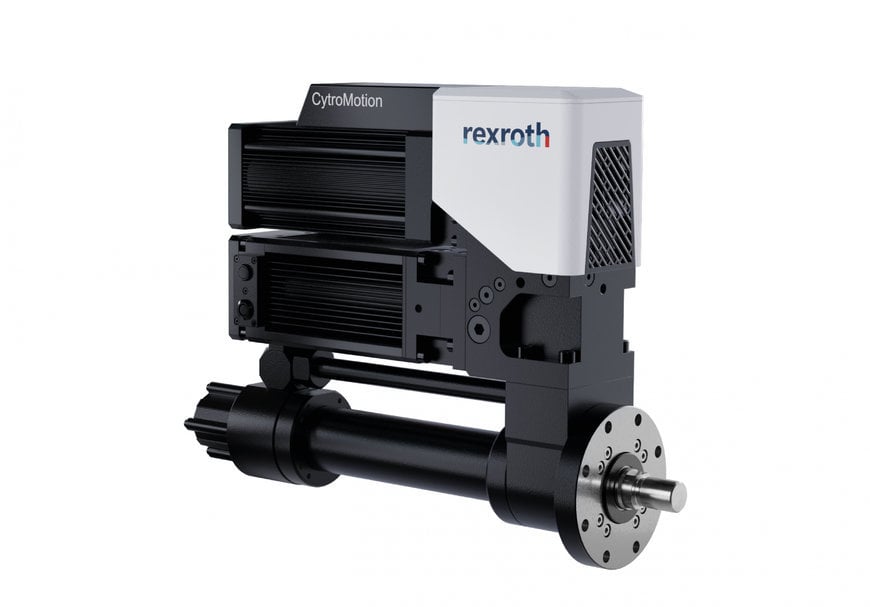
Compact hydraulic actuator, electrically controlled: With CytroMotion, Bosch Rexroth has expanded its range of self-contained actuators for forces of up to 110 kN.
- Energy-efficient compact actuator with a wide range of applications
- Low-maintenance alternative to hydraulic and electro-mechanical axes
- Electrical control makes engineering and commissioning easier
Thanks to fully electric control, CytroMotion also makes engineering and commissioning easier. The efficient power-on-demand drive and the maintenance-free, hermetically sealed design help to save CO2 and minimize operating costs.
Linear movements involving large forces and micrometer-precise positioning are found in many machines and systems. For technical implementation, a compact and simple solution is needed. At the same time, the need for greater energy efficiency and process safety is growing. Self-contained actuators meet all these requirements by combining the power density and robustness of hydraulics in a compact, energy-efficient and low-maintenance system solution. The new CytroMotion self-contained actuator offers all these benefits in the power class up to 6.2 kW.
CytroMotion combines the standard components electric motor, hydraulic pump and cylinder with important control functions and poppet valves to form a compact, integrated assembly with a hermetically sealed hydraulic part and a fully electric control system. The optional features include a digital position measurement system with an industry-standard SSI interface, a circuit variation with an engageable, reduced-force rapid traverse system and pressure relief valves for adjustably limiting maximum loads or process variables.
This innovative design approach opens up new functional possibilities for mechanical and process engineers. After all, it allows a much longer stroke compared to mechanical linear axes in the same space. It also results in a range of benefits throughout the life cycle. The electric control system is similar to that of an electro-mechanical axis and can be controlled by a conventional frequency converter from Bosch Rexroth or a third party provider. Engineering and commissioning require no hydraulics know-how and are carried out within a known control architecture of the customer. An online configurator helps to find the optimum actuator configuration for the particular application in just a few minutes. Installation is carried out without piping, hoses, or filters.
During operation, CytroMotion in conjunction with modern control technology increases not only process quality but also energy efficiency. While linear movements and forces can be regulated electronically in a straightforward and precise manner, the self-contained actuator reduces electricity consumption and the resulting carbon-dioxide emissions by up to 80 percent compared to conventional hydraulic systems. The variable-speed power-on-demand drive uses electricity only when power output is actually needed. In force holding mode where virtually no electricity is used, integrated poppet valves support the loads applied.
CytroMotion is suitable for a wide range of applications. These range from power plant systems, metalworking, and pressing and joining applications with force holding mode to ring rolling mills in the steel industry with large forming, process, and holding forces. The encapsulated hydraulic system is also suitable for testing and quality assurance and for use in the process and food industries.
CytroMotion also enables condition monitoring to maximize availability. To make it easy to measure process forces and monitor internal system parameters, open interfaces and pressure sensors are integrated. As a result, anomalies in potentially critical process parameters can be identified early on and unplanned downtimes can be avoided.
The hermetically sealed system also allows for reduced-maintenance operation. While electro-mechanical axes may need external or cyclic lubrication, CytroMotion works with the same oil from the factory over a significantly longer service life. If pressure sensors need to be replaced, the system remains sealed.
The self-contained actuator also works extremely quietly. Depending on the application and installation, the low-noise internal gear pump limits noise emissions to no more than 70 dB(A). Roughly speaking, this is as loud as the noise level of an open-plan office.
The servo-hydraulic axes complement Bosch Rexroth’s overall portfolio which includes hydraulic and electro-mechanical solutions.
For more information on the CytroMotion, visit http://www.boschrexroth.com/cytromotion.
www.boschrexroth.com