www.industryemea.com
21
'22
Written on Modified on
New laser cell for more sustainability
Sustainability - yes, of course! But how do you implement it in everyday industrial life? With the support of TRUMPF, the Reutlingen-based company Rieber, has improved the material and energy efficiency in its production - for the sake of the environment.
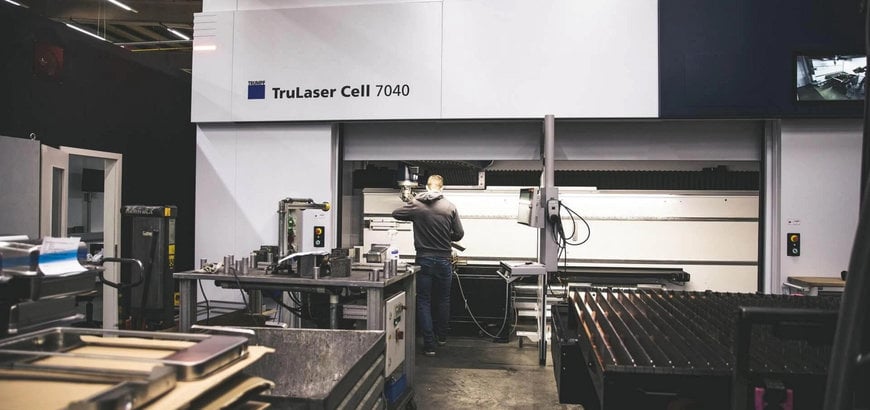
Anyone who comes to Rieber cannot miss the advertising board at the entrance. The company is committed to sustainability as "Your future and our passion". The passion is first evident in the showroom, where the company exhibits some product highlights: a grill plate for canteens, for example, which heats up in just six minutes.
"A conventional grill plate made of steel needs around 25 minutes to heat up," says Ingo Burkhardt, general representative at Rieber, adding: "Due to the increased energy efficiency, our grill plate will have already paid for itself in less than a year." This is made possible by a special material combination out of aluminium and stainless steel, which is used only by Rieber in this form. Also on display are "intelligent meal boxes", a kind of digitalized returnable system. For example, this allows restaurateurs to track by smartphone, where their containers are currently situated, and to collect them again at the end - thus dispensing with disposable packaging. Rieber products, as quickly becomes clear in their showroom, stand for efficient and thus also sustainable cooking and storage of food.
SPECIAL COMPETENCE IN DEEP DRAWING
When the Reutlingen-based company was founded in 1925, it started out as a cabinetmaker's shop. It was not until the 1950s that the company discovered stainless steel as a material for sinks and sink units and placed it at the center of its product range. In the meantime, Rieber has become a leading supplier of kitchen technology for both the catering industry and private households. Its core competence is deep drawing, one of the most important manufacturing processes for containers of all kinds and indispensable in industry. In this forming process, a press presses on a firmly clamped sheet of metal until it becomes a hollow shape. This is tricky because the sheet metal must not tear during forming.
Today, parts up to 600 millimeters drawing depth made of stainless steel and formed parts made of titanium are part of Rieber's product range. Customers use these not only in kitchen technology, cafeterias or serving utensils, but also in the aerospace industry. Many products can be individually adapted to customer requirements. In production, this means that the employees manufacture numerous variants.
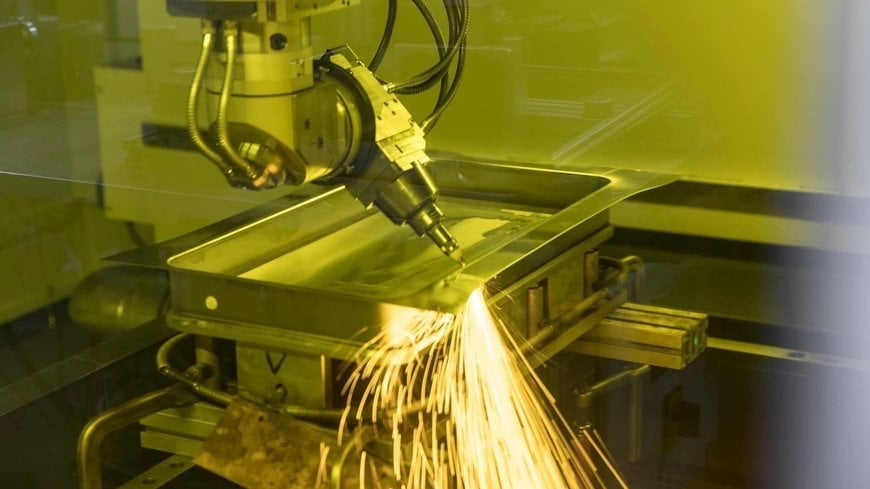
Deep drawing is one of the most important manufacturing processes at Rieber. But after that, a flexible tool is needed to precisely cut off the edges before joining the deep-drawn components. This is what the TruLaser Cell 7040 with an integrated TruDisk 3001 disk laser is for on the Rieber factory floor.
SUSTAINABILITY ALSO IN RIEBER'S OWN PRODUCTION
For Rieber, however, the products themselves are only one half of the path to greater sustainability. "We also want to conserve resources and the environment in the manufacture of our products," Burkhardt explains. Hence, the keywords are energy efficiency in production. To this end, Rieber has exchanged ideas and consulted with its long-standing partner TRUMPF. Now a new TruLaser Cell 7040 3D laser machine with an integrated TruDisk 3001 disk laser is on Rieber's factory floor. The new laser system reduces energy consumption by a whopping 63 percent! "Consequently, we save about 60 tons of CO2 annually," Burkhardt is pleased to report. In addition to better energy efficiency, the TruLaser Cell 7040 also brings noticeable improvements to everyday production. The cutting speed for some components is up to 85 percent higher than the previous cutting system, which reduces the overall processing time accordingly. "The axis acceleration on the TruLaser Cell 7040 reaches up to 10 m/s², and the positioning accuracy of the linear axes is just 0.08 millimeters," adds Ralf Motz, manager of the TRUMPF Alb-Bodensee sales office.
LASER CUTTING MACHINE FROM TRUMPF WORKS PARTICULARLY PRECISELY
This precision is important: "The stainless-steel sheet has residual stresses after deep drawing. When they are released, the laser must be able to compensate for this," says Fabian Renz, who is responsible for development, design and tool construction at Rieber. To be able to join the deep-drawn components, you must first cut off the edges where the sheet metal was fixed in the press. Rieber joins the components in the further production process by means of laser welding, which again requires particularly low tolerances. Particularly in the aerospace industry, for which Rieber supplies components and assemblies made of stainless steel and titanium, increased quality is required. After all, safety-relevant components are involved here. Therefore, the producer must precisely coordinate the cutting operations, even if the process speed is reduced.
The quantities for the 3D laser cutting machine are small, down to batch size 1. "For us, the non-productive times are sometimes longer than the cutting times. That's what makes fast set-up so important," says Renz. "That's not a problem for TRUMPF. We offer the TruLaser Cell 7040 with two flexible stations. This design makes it possible to set up and manufacture in parallel," adds Motz. Renz explains how his company makes efficient use of this setup: "On the one hand, we can also manufacture in quantities of one or development projects, while on the other hand we produce larger quantities. Hence the machine pays for itself very quickly for us."
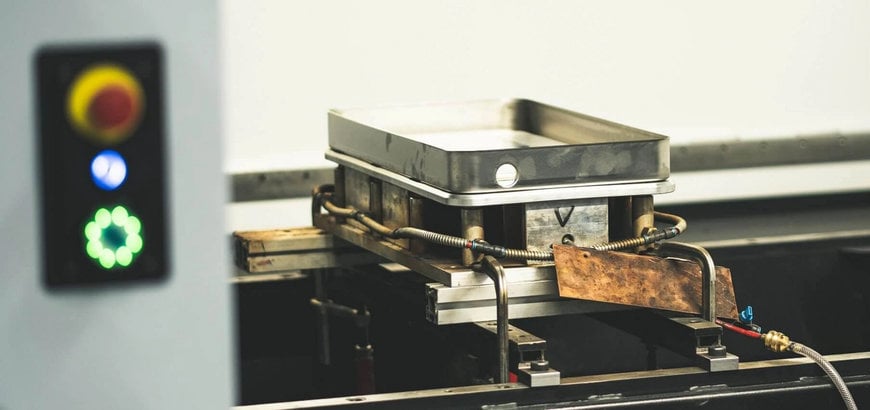
Rieber wants to conserve resources and the environment in its production. The new 3D laser system from TRUMPF makes sure of that: it minimizes energy consumption by an impressive 63 percent and thus saves about 60 tons of CO2 annually.
www.trumpf.com