Mitsubishi Electric and TMEIC Develop Electrical Motor-design Support System Incorporating AI
Contributes to workload and lead time reduction by dramatically shortening time to achieve same results as existing methods.
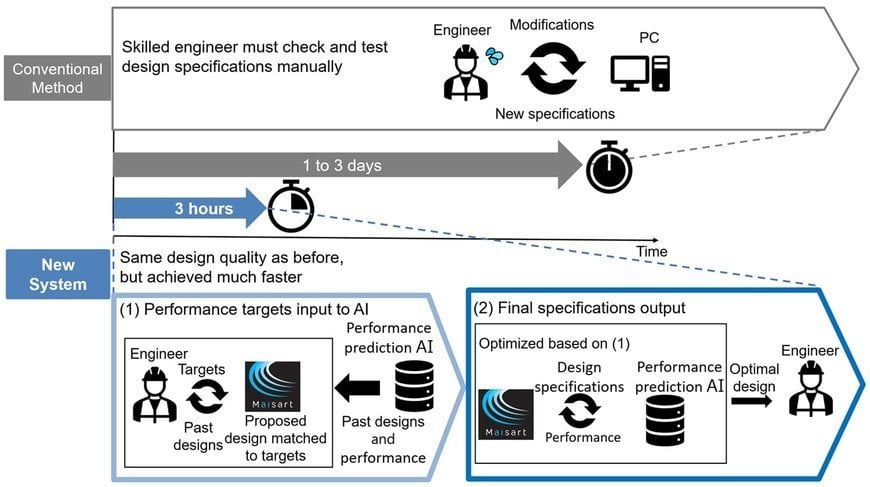
New industrial motor design support system incorporating AI
Mitsubishi Electric Corporation announced today that together with Toshiba Mitsubishi-Electric Industrial Systems Corporation (TMEIC) they have developed a electrical motor-design support system incorporating Mitsubishi Electric's Maisart®* AI technology to dramatically shorten the time required to produce electrical motor designs that achieve the same performance as conventional design methods deployed manually by skilled engineers. TMEIC plans to adopt the system for internal operations in FY 2024.
The new system can be used to design electrical motors for pumps, compressors and fans application in industries. When designing such motors, design engineers conventionally must repeatedly adjust design specifications to balance performance versus design, such as power efficiency versus motor size. For engineers with limited experience, it can be especially challenging to balance specifications to satisfy all requirements, often requiring them to implement time-consuming trial-and-error testing, which later must be checked by skilled engineers.
Using the new system experimentally to perform design tasks that had already been completed in the past by engineers, Mitsubishi Electric confirmed that design time can be reduced to a mere three hours compared to one day for experienced engineers and up to three days for less experienced engineers (assuming one day equals eight work hours). The system also helps to simplify and standardize design processes, since performance targets can be simply adjusted to have the AI generate appropriate new specifications. In addition, the system is expected to support the transfer of designing skills to less experienced engineers and help them to become more proficient.
The new system will be presented during a meeting of the Institute of Electrical Engineers of Japan at the Higashi Osaka campus of Kindai University as well as online on September 29-30.
Key Features
1) Electrical motor-design support system achieves results equal to manually produced designs
- Engineers input performance requirements and then the AI proposes the best specifications by referring to historical design data.
- Engineers check the AI-proposed specifications for performance, adjust targets if necessary to obtain finely tuned new AI-proposed specifications. The interactive process can be repeated until specifications that best satisfy the final performance targets are achieved.
- The results are equivalent to conventional manually produced designs.
2) Performance-prediction and specification-optimization technologies dramatically cut design time
- AI technology predicts electrical motor performance using design specifications accumulated in the past by TMEIC.
- Engineers can interact with the AI by fine-tuning performance targets to obtain precise specifications based on past designs that the AI searches and then optimizes.
- Design time is dramatically reduced from one to three days to just three hours.
Fig. 1 Work flow for determining best design specifications that meet overall requirements
Plans for the Future
The newly developed electrical motor-design support system will be introduced commercially at TMEIC in FY 2024. The time required for designing processes and production lead time are expected to become much shorter as a result of introducing the new system.
Detail of Features
1. Interactive multi-objective electrical motor-design technology produces high-quality designs quickly
Using conventional multi-objective optimization techniques, is has been difficult to quickly produce ideal design specifications that satisfy all performance targets covering every category, such as motor size, power efficiency and heat generation, some of which are inversely related. Mitsubishi Electric’s new interactive multi-objective design optimization technology, however, enables performance specifications to be designed within a remarkably short time by using both meta-heuristics, a method for efficiently searching combinations of parameters, and a back-and-forth process in which engineers interact with the AI.
The technology has two basic components: (1) the engineers register desired performance targets with the AI, and (2) the AI presents optimal design specifications, including by referring to past specifications that would best achieve the desired performance targets. Thereafter, engineers check the proposed specifications against the targets and then make adjustments, if required, to have the AI propose finely tuned new designs. This interactive procedure can be repeated until the engineers are satisfied with a design that best satisfies the final performance targets. As a result, specifications that closely match desired performance, similar to those that conventionally must be obtained manually, can be acquired in a significantly shorter timeframe.
2. High-speed performance prediction technology and efficient presentation technology
Mitsubishi Electric’s new AI technology creates specifications by referring to past designs, searching for the best specifications and then presenting multiple combinations of possible specifications optimized to performance targets. Engineers can choose the specifications that best suit overall needs and quickly determine a final design that matches their final performance targets.
In the case of applying multi-objective optimization in electrical motor design, engineers conventionally must spend much time calculating the performance of many sets of design specifications. TMEIC, however, has developed a fast performance-prediction technology that learns past specifications and their performance results. By combining TMEIC’s electrical motor knowledge and Mitsubishi Electric’s AI expertise to produce evaluation criteria that synthesize electrical motor performance and AI search knowhow, the system produces specifications that precisely match desired performance targets.
Mitsubishi Electric has confirmed that the time for designing motors can be shortened dramatically to three hours. Also, less experienced engineers can use the system to produce motor designs of the same quality as those produced manually by expert engineers. As a result, the newly developed AI designing system is expected to help reduce workload and shorten lead times.
In the example case shown in Fig. 1, the design engineer inputs desired performance targets for electrical motor size, power efficiency and heat generation. Size and efficiency are prioritized, so the AI proposes appropriate specifications. The engineer decides that C is initially the best option, but seeks a slightly more efficient design, to which the AI responds with adjusted specifications. The resulting design D offers the best combination of specifications, so the engineer uses the AI to optimize D. Several versions are output and the engineer selects the revised version D Rev. 2 as the best overall design.
www.mitsubishielectric.com