www.industryemea.com
28
'22
Written on Modified on
Dürr presents new developments for the final assembly of the future
Dürr presented a new design concept for greater flexibility and efficiency in final assembly at the first NEXT.assembly Innovation Summit. The virtual event on October 25, 2022, attracted an international audience.
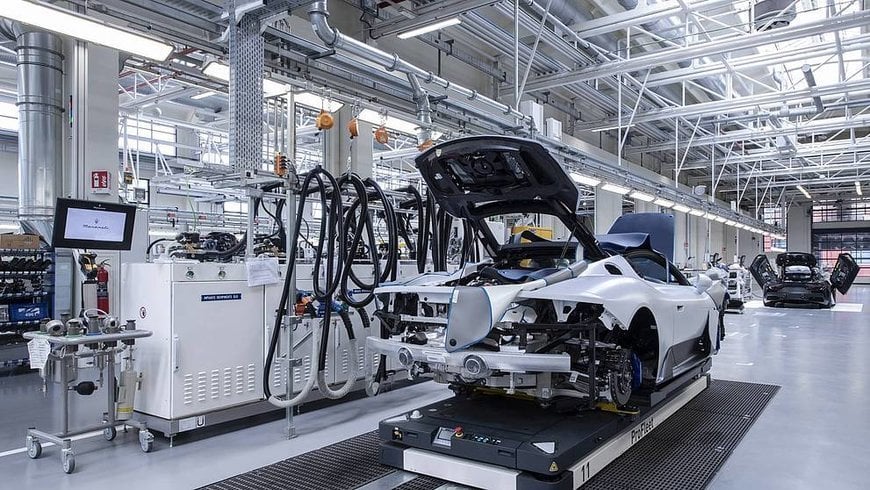
Product innovations like the combined test stand x-combined and the automated guided carrier ProLiner are central to Dürr’s final assembly of the future. They enable final assembly without pits and rigid conveyor technology, making it easy to increase manufacturing volumes and seamlessly integrate new models.
The evolution towards e-mobility and hybrid production with different drive and model variants presents car manufacturers with technological challenges. Dürr’s response is its integrated final assembly strategy NEXT.assembly, which delivers the most comprehensive offering on the market featuring innovative solutions for conveyor, gluing, assembly, filling, and inspection technology, as well as complete turnkey solutions. Consulting and digitization expertise complement the offering.
To present this variety of products to a diverse audience, Dürr launched the NEXT.assembly Innovation Summit. “Today and in the future, we want to help our customers build their vehicles in the most efficient way possible. With our first innovation summit for final assembly solutions, we demonstrate our expertise and share our ideas with the world. Our new concept for the final assembly of the future opens a new chapter in greater manufacturing flexibility,” said Bruno Welsch, CEO Paint and Final Assembly Systems of Dürr Systems AG, at the event opening. The event was broadcasted virtually from a studio near Dürr’s headquarters in Bietigheim-Bissingen.
Exemplary solutions in contemporary final assembly
The event opened with insights into completed customer projects to illustrate Dürr’s complete range of products and services for final assembly – from AGVs (automated guided vehicles) to test stands in both greenfield and brownfield settings.
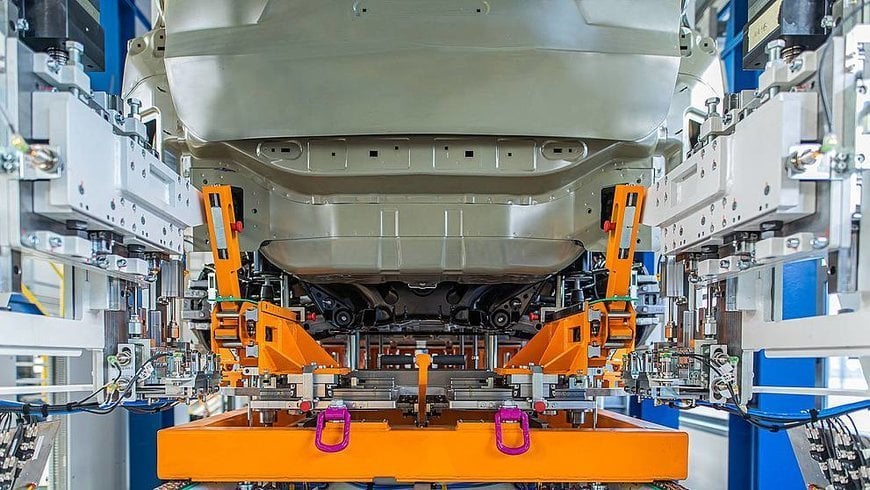
“Our successes reflect the current evolution in the automotive market. Custom solutions ensure greater agility in plant design, make it easier to integrate battery-powered vehicles into existing plants, and support greenfield start-ups of electric vehicle manufacturing,” said Dirk Gorges, Executive Vice President Sales Paint and Final Assembly Systems at Dürr Systems AG.
A vision for the future
Using the motto “NEXT.assembly of the future,” Dürr came up with a concrete picture for the final assembly of the future: An integrated concept that rethinks final assembly and makes the previously unachievable possible, such as the variable adjustment of manufacturing volumes or the redeployment of equipment to other factories. “An essential key to this flexibility is complete independence from the building itself,” said Dirk Gorges, explaining the innovative concept. Pits and suspended ceilings are no longer required in any process step thanks to new solutions like AGC ProLiner and x-combined.
Automated guided carrier for flexible chassis lines
In the NEXT.assembly concept, traverses are no longer used in final assembly. AGVs perform the work in the trim and final line and connect all areas with several vehicles in transit as a small buffer to compensate for interruptions on the line. “Since AGVs in the chassis line are not enough to meet the special requirements of this important manufacturing step, our engineers developed something completely new with the automated guided carrier. AGCs are autonomous, battery-powered structural steel modules with integrated hangers,” explained Denny Monti, Business Development Director of CPM S.p.A., an Italian subsidiary of Dürr Systems AG. The pre-assembled AGCs, equipped with off-the-shelf profiles, are not connected to each other and therefore are easy to redeploy to adapt the lines to corresponding manufacturing levels.
Compact, fully automatic and without pits
In a change that seemed impossible until now, the final assembly of the future no longer requires pits at the end of the conveyor belt. “This is the main pillar of our concept, made possible by our new development x-combined: the world’s first combined test stand for inspecting both wheel alignment and brakes and sensors. Depending on the respective cycle time, the headlight settings can optionally be additionally measured and adjusted with the new measurement and adjustment system x-light,” reported Jörg Neumann, Director Product Line EoL at Dürr Assembly Products GmbH.
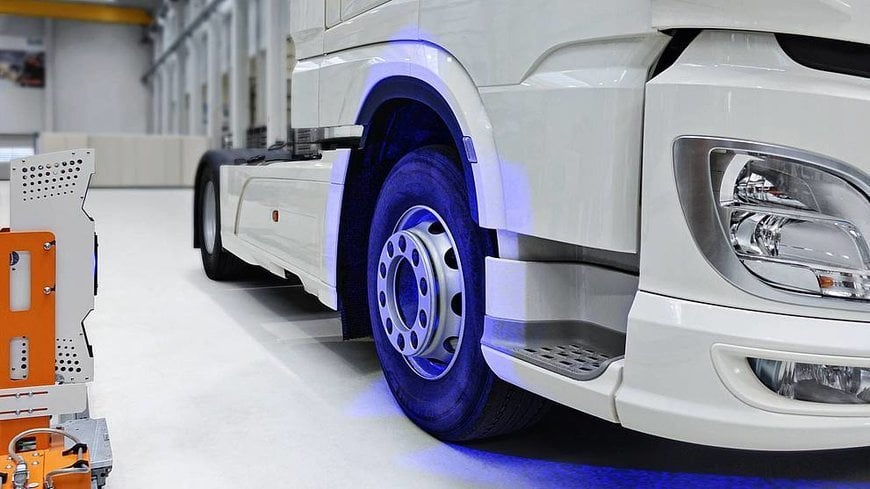
Flexible scalability
Overall, the new design concept from Dürr represents a final assembly solution that is completely flexible, modular, and scalable. Customers now have the option to adapt their manufacturing to market conditions. Furthermore, individual modules or the entire manufacturing system can be moved to another location if needed. “Massive and difficult-to-alter final assembly systems are a thing of the past. That is our central message,” summed up Dirk Gorges.
More than 400 participants from all over the world watched the event and took part in the Q&A sessions after two and a half content-packed hours. The first iteration of the NEXT.assembly Innovation Summit was geared towards interested parties in Europe and the Americas. On November 17, Dürr will host a Chinese-language event for its customers in China.
www.durr.com