Leuze promotes "integrated connectivity" concept
Increased efficiency, improved commissioning, machine monitoring and process optimisation.
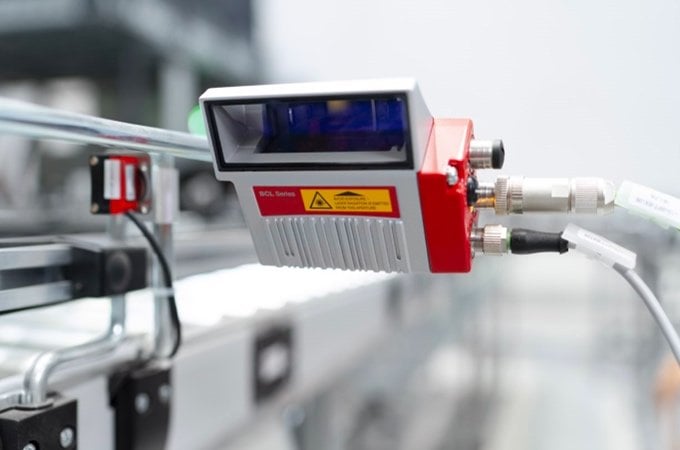
The bar code readers from Leuze (here the BCL 300i) are equipped with "integrated connectivity".
Everything in the sensor
Integrated connectivity means: All relevant industrial Ethernet interfaces are integrated into the sensor. It sounds simple but is not standard on the market. Instead, manufacturers often offer devices without an industrial Ethernet interface to save development effort. In such cases, the interface is available via a gateway. The following examples show why this is not the optimal solution and why the system operator benefits in multiple ways with integrated connectivity from Leuze. The benefits range from commissioning (device management) to machine monitoring (condition monitoring) to process optimization.
Streamlined system layout
Leuze offers devices with integrated interfaces for PROFINET, Ethernet/IP, and EtherCAT. The significant advantage that can already be gained during commissioning is demonstrated using design example with and without integrated connectivity. First a look at systems with barcode readers without integrated interfaces: here, each scanner must be connected to a separate gateway - this means an additional gateway with its own power supply for each barcode reader. As a result, the installation effort and the number of cables are twice as much as needed. The parameterization is also considerably more complex. Don’t forget: Because of the required gateways, there are significantly more devices in the system that can cause a malfunction and must be checked. In comparison, the same system with integrated connectivity: The industrial Ethernet interface is already integrated into every bar code reader. This makes separate gateways superfluous. Above all, the system layout is very clean and requires fewer cables. Last but not least, errors can be eliminated more quickly as fewer devices have to be checked.
The implementation of a linear topology for each integrated switch reduces the cabling requirements, saving time and money.
Switch included
Leuze sensors with integrated connectivity also have an additional feature that contributes to efficient commissioning: the devices have one switch as standard, i.e. an Ethernet input port and output port each. As a result, system operators do not need an external switch. In addition, several devices can be wired more easily, for example in a ring or linear topology. With linear wiring, the system operator connects one sensor to another through integrated switches. Only the last sensor in the chian is connected to the controller. The advantage here is also a simpler system design and fewer cables. Devices without an integrated switch, on the other hand, require an external Ethernet switch. Users must also connect each individual sensor to the switch via a star topology and then connect this to the controller
The usual control environment
Integrated connectivity also means that you can work in your usual control environment. This is possible because the entire device parametrization is integrated into the GSDML file ("Generic Station Description Markup Language") of PROFINET, for example. In contrast, many other Ethernet-based devices on the market generally have to be parametrized via a web server. This is complicated because each manufacturer provides its own web server version with its own user interface. Users have to familiarize themselves with new interfaces every time and find the corresponding functions. In addition: devices without Ethernet that are connected via a gateway often require productspecific manufacturer's software for parametrization. This may result in compatibility issues with the hardware used.
For example, if the manufacturer does not update their software after a few years. Here too, integrated connectivity has multiple advantages:
- Users remain in their usual control environment
- No manufacturer software installation and related training required.
- No need to access a web server
Leuze devices with integrated connectivity are very easy to parametrize. Only the GSDML file has to be downloaded from the Leuze website via the control and copied once into your engineering software. The modules are then available in the hardware catalogue. The function of the device is explained in a clear and concise way. This makes parametrization and sensor usage easy and the manual is not required in most cases.
Support from the sensor
A look at the sensor’s device profile with integrated connectivity further simplifies programming. As an example: for the AMS and BPS positioning sensors, Leuze not only provides positioning values but also a calculated speed value. Anyone who needs this value in their system saves time as it does not need to be calculated. In addition, if you only want to filter for certain barcodes without integrated connectivity, you have to do this via the controller. Leuze BCL bar code readers can be done more efficiently because here you can prefilter according to specific criteria. Only codes which correspond to the required pattern are transferred to the control. The option to duplicate PROFINET devices in the engineering tool saves time. Users only have to specify the parameters once and can then copy the settings as needed. Integrated connectivity even helps when a device is replaced: If a damaged sensor has to be replaced, the system automatically transfers all the parameters stored in the controller to the new device. The sensor is immediately ready for use.
Simple interface management in all control environments with "integrated connectivity" from Leuze.
Keeping an eye on quality
Integrated connectivity not only provides support during commissioning but also with machine monitoring, i.e condition monitoring. For efficient operation, system operators need answers to questions such as: is the plant operating correctly? When do I need to schedule maintenance? The answers are provided by the integrated interface. Via industrial Ethernet communication, it not only transmits the actual process values but also diagnostic data which are available in the controller. As a result, all identifying data can be read out via a barcode reader to manage the device. This includes the serial number or the software/hardware of the sensor. Moreover, there are quite a number of diagnostic parameters, such as the number of OK and NOK readings. In particular, the system with the bar code readers, the system also supplies a quality indicator for each individual code reading. This provides information about the quality of the readings. The value is generally between 90 and 95 percent and can be monitored to detect deviations during operation. For example, caused by contamination or mechanical damage. Remote monitoring can also be implemented as an additional communication channel via OPC UA. The control can be used for this purpose, but Leuze sensors provide a much easier solution, as they can be accessed directly via the OPC UA. As a result, system operators can monitor their devices while the process is running. This gives them real-time information on the performance of the system. If required, the data can also be transferred to a cloud - there are no restrictions whatsoever.
Simple process optimization
How can processes be optimized on the basis of the collected data? This is demonstrated by two representative practical examples using barcode readers. First example: The scanning window of the sensor can become contaminated. In some systems this does not happen for years, in others, it occurs more quickly. In order to determine which sensor is contaminated, data evaluation via OPC UA can be used. Based on the data, a software program records the reading quality of each individual decoding process. This indicates maintenance for bar code readers with impaired reading performance. Second example: The label itself can also cause problems - for example, if the code is damaged or printed incompletely. In this case, it is not enough to monitor an individual sensor to determine the error. Instead, the faulty label has to be traced along different reading stations to identify it. This makes it possible to detect similar evaluations and use the identification number to determine the label involved.
Summary: More efficient on three levels
Integrated connectivity offers advantages on several levels. It contributes to easier commissioning and provides additional information for machine monitoring. This information is particularly useful for process optimization, resulting in optimal system performance. All sensors developed by Leuze for Fieldbus-controlled automation, for example in intralogistics, are equipped with integrated connectivity. This allows system operators to save time and money. The Sensor People from Leuze are able to provide you with support to select and implement the optimum solution.