www.industryemea.com
15
'15
Written on Modified on
NSK solution saves €40,000 at automotive supplier
When a global manufacturer of bus gearboxes was unexpectedly faced with having to replace roller bearings in a series of helical transmission gears due to failures within the warranty period, NSK was invited to assess the cause of failure and suggest a solution.
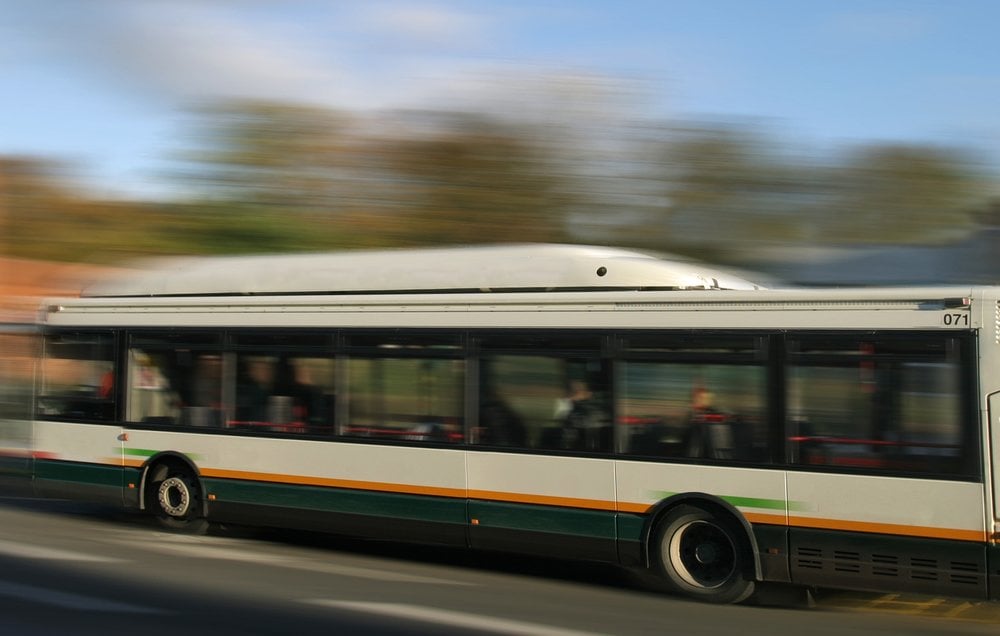
Involving the customer at every stage of the AIP process, the team recommended the adoption of ready-to-install flanged bearing units. NSK both designs and produces these customised units for several manufacturers of mobile production machinery in market sectors such as agriculture, construction and material handling equipment, and it was deemed the perfect solution to the issue of roller bearing failures at the gearbox plant.
NSK’s customised flanged bearing units are sealed and pre-configured units that comprise the bearing, enclosure and mounting parts. As they are supplied ready for use, assembly errors no longer occur.
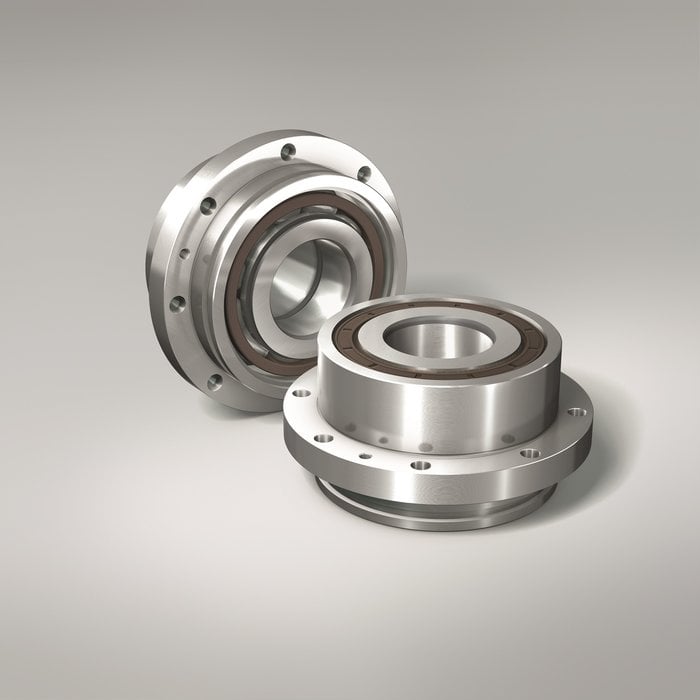
Sample parts were made within a short lead-time by the NSK factory at Munderkingen, Germany. The angular ball bearing deployed in the unit offers a larger contact angle of 35° to better accommodate high axial forces, while a special shaft gasket with a vent hole also features. An O-ring is utilised to seal the corrosion-proof housing from external contaminants.
With the sample flanged bearing units complete, tests were completed, the success of which prompted the gearbox manufacturer to order 4,000 flanged bearing units from NSK on annual basis.
As a result of the NSK’s Added Value Programme (AIP), together with the inclusion of the customised bearing, the customer is now highly satisfied with the gearbox performance and has made an annual saving of €40,000 from the production process.