www.industryemea.com
27
'15
Written on Modified on
NSK bearings deliver €96,000 saving for fish processor
Interrupting a continuous manufacturing process occasionally because of a bearing failure can be irritating, but when the failures become more frequent the costs in lost production start to mount up. For one large producer of fish products, repeated bearing failures on a heat exchanger unit demanded attention, which led to NSK delivering a huge annual saving through the installation of improved bearing technology.
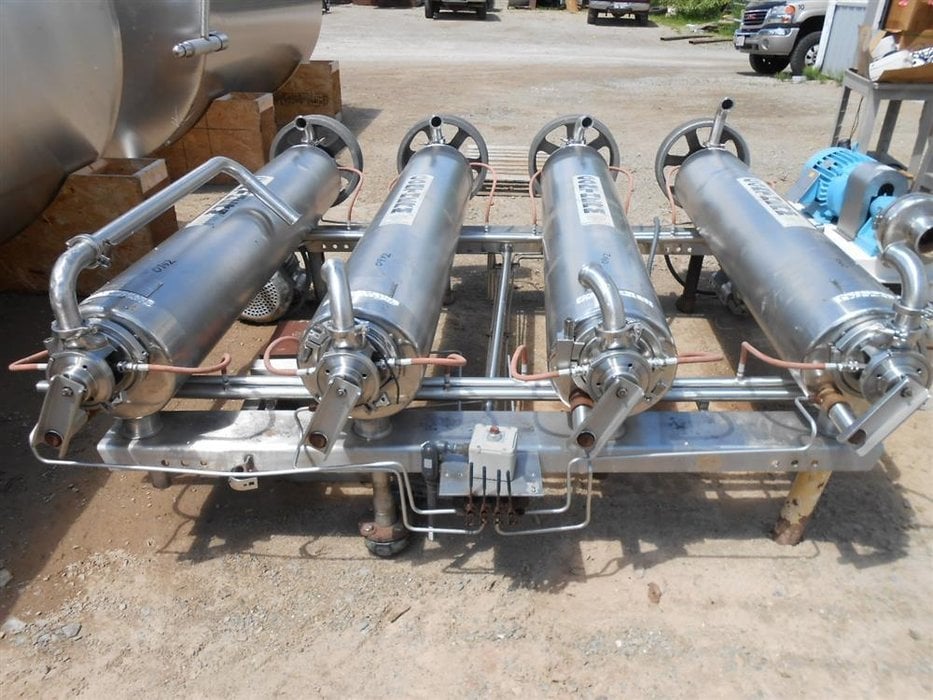
NSK offers the services of its experienced application engineers to examine the circumstances of a bearing failure, with the aim of improving reliability and efficiency. The Added Value Programme, AIP, aims to help to production and maintenance managers to understand the causes behind bearing failure and what steps can be taken to improve the situation.
In this particular case, the manufacturer of fish products had five heat exchanger units and was experiencing twelve bearing failures every year. Aside from the maintenance costs to repair the heat exchanger each time, it was the five hours of lost production time that focussed the attention of the production manager sufficiently to call-in NSK.
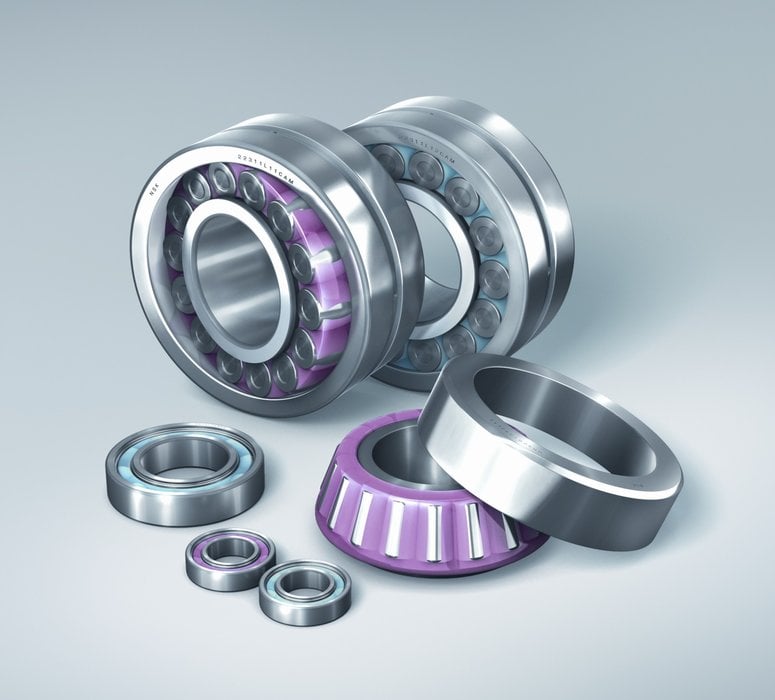
Engineers from NSK investigated the issue and conducted a failed bearing analysis which determined that both water and hard particles were contaminating the bearing and causing a breakdown of the lubricant. Considering the nature of the application and the demands of the process, NSK proposed a trial using its Molded-Oil™ deep groove ball bearings.
Molded-Oil™ technology has been developed by NSK to greatly improve the performance of bearings in terms of reliability by allowing maintenance-free operation. Molded-Oil™ Bearings are lubricated with NSK’s own oil-impregnated material – Molded-Oil™ – which consists of lubricating oil and polyolefin resin that has an affinity for oil. Lubricant slowly seeping from this material provides ample lubrication to the bearing for extended periods. Although similar designs are used by other bearing manufacturers, NSK provides a lubricating oil content of more than 50% by volume, which is considerably more than the competition currently offer.
The trial period eventually ran to more than three years without the bearing showing any signs of requiring replacement. The performance of the trial bearing was more than sufficient evidence for the production manager to request the NSK solution to be installed across all five heat exchangers.
The annual savings made as a result of the decision to use NSK Molded-Oil™ bearings were significant. By avoiding any major loss of production, the company’s total savings were in excess of €96,000.
NSK is offering its Molded-Oil™ technology on standard deep groove ball bearings, spherical roller bearings and tapered roller bearings with inside diameters up to 110mm. For applications where corrosive environments exist or for exposure in wash down facilities, the bearings can be manufactured from stainless steel.
NSK’s Added Value programme, AIP, is designed to improve efficiency and reduce the frequency of breakdowns attributed to bearing failure. By implementing this comprehensive programme, customers such as this one, can expect to improve profitability and competiveness.