www.industryemea.com
16
'23
Written on Modified on
Portescap Motion performance and durability for high-dexterity robot build
Portescap worked with a robot OEM in China to optimise motion performance and durability, while ensuring cost-effective production.
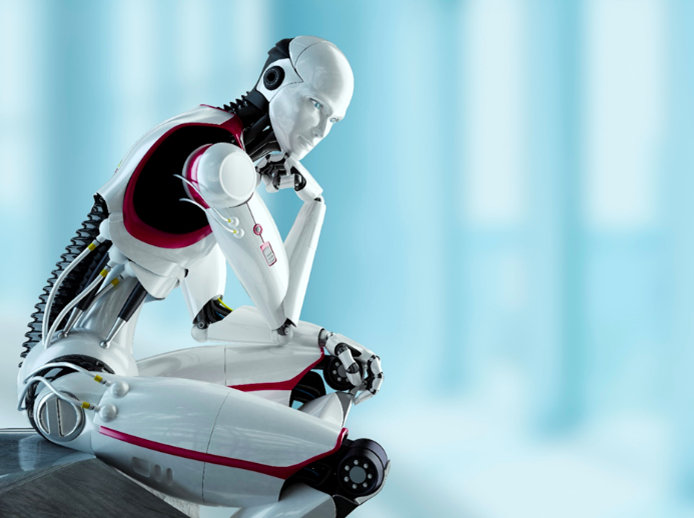
One of the key functions of humanoid robots in industrial applications is to improve efficiency and safety while performing tasks in environments that are arduous or even dangerous, yet require utmost precision in every action. As a result, they are increasingly used in numerous arenas ranging from manufacturing through to healthcare and space research.
The primary objective of humanoid robot development is to maximise the capabilities of dexterity. Today, humanoid robots are a reality that can provide support in tiring or arduous tasks, or else can be used in situations that would otherwise be too dangerous for humans. As such, these machines are used in applications ranging from healthcare through to military operations, or exploration and search in hazardous environments. On the contrary, cobots, or collaborative robots, typically featuring a base and arms, are designed to work alongside humans, replicating human movements. Often installed to assist in manufacturing production, cobots can increase productivity and process efficiency.
To achieve a high level of robotic dexterity and precision, multiple motor axes are required. Humanoid robots need more than 20 motor axes to actuate human-like movements, each axis representing a degree of freedom in movement, such as rotation or translation. Alternatively, cobots usually have six to eight motor axes, controlling each robotic joint for movement and positioning in the shoulder, arm, and wrist, as well as end effectors, such as grippers.
Ensuring dexterity and control
A Chinese manufacturer of humanoid robots and cobots approached Portescap to provide a motion solution to drive and control the arm and knee joints of several of its robot designs. The requirements for motion performance were high in order to achieve the necessary speed and accuracy of motion. This would ensure dexterity as well as the control to establish safety when working in proximity to humans. With a high number of axes involved, cost-effective manufacture was also a priority for the robot OEM.
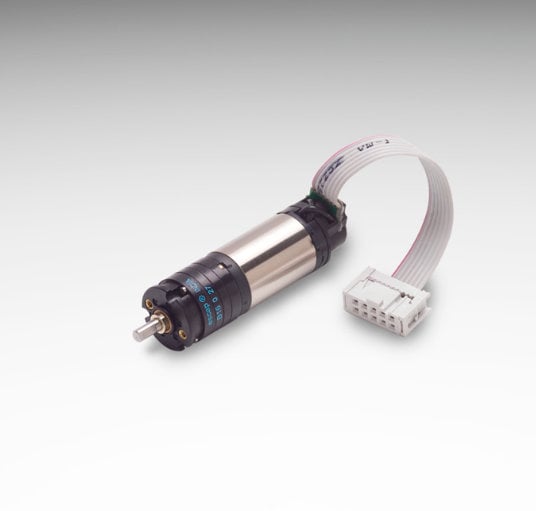
Both cobot and humanoid robot designs had highly defined physical footprints and would also need to minimise mass to optimise overall dexterity and movement efficiency. Additionally, the motion solution had to fit within a compact, low weight envelope. Moreover, working alongside humans, the robot noise levels had to be kept to minimum, so the motors driving them needed to ensure quiet operation.
Minimising weight and footprint
The OEM engaged Portescap based on its extensive experience in designing motion solutions for robotics. The motion solution designer specified its Athlonix™ 24DCT brush DC motor and MR2 encoder to meet the OEM’s requirements. Neodymium magnets helped to increase available torque by 20% over the competing motor designs, thanks to the properties of greater magnetic strength, which also enhanced power density. The motor’s coreless design, free from a traditional iron core but instead utilising surrounding permanent magnets, also contributed to a lower mass motion package.
To optimize the lifetime of the motors, Portescap’s solution included constant spring force carbon brushes. This design ensured that regular contact with the commutator would minimize the potential of bounce and increased friction during operation, as well as improving performance with a more consistent electrical connection. This smooth performance would also reduce both audible and electronic noise, which is crucial when operating in environments alongside other electronic equipment.
Motion solution customisation
Accurate position control for the robotic joints was achieved with a Portescap MR2 magneto-resistive encoder. Utilising a resistive element to measure position, accurate feedback with up to 512 lines of resolution could be provided. Meanwhile, the resistive design gave inherent durability, even in harsh operating environments, thanks to its free-of-moving-parts design, as well as protection with Portescap’s sealed housing.
To achieve the robot manufacturer’s cost targets, Portescap tapped into its global supply chain to source the most cost-optimal components while still meeting the necessary performance criteria. Portescap’s engineers were also able to collaborate closely with the robot OEM’s design team throughout the project. This process enabled the customisation required to achieve the specification, while meeting the tight timescales for development, and minimising cost of production.
www.portescap.com