www.industryemea.com
20
'23
Written on Modified on
WHAT SETS TOSHIBA’S CERAMIC BALLS APART?
Take a look at the behind-the-scenes of the development and implementation of a Toshiba AI quality inspection system.
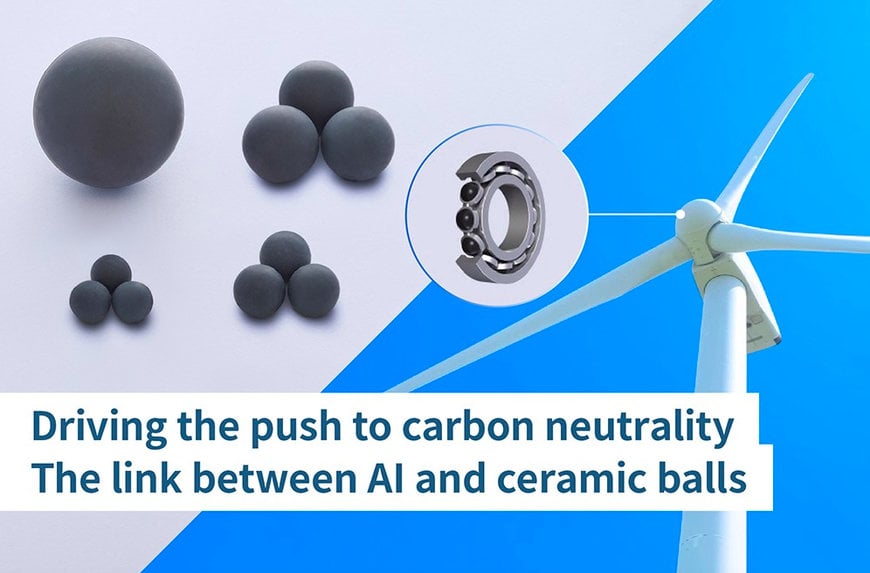
The more people use electric vehicles (EVs), the closer we get to carbon neutrality, and thankfully, sales for these vehicles have been growing worldwide in recent years. One issue that can occur with EVs, however, is the “electric corrosion” of the bearings that mount the various vital parts of the vehicle onto the motor—a serious issue, as it can lead to the breakdown of the vehicle. Fortunately, the ceramic balls Toshiba has developed for use in these bearings have succeeded in solving this issue.
The Toshiba Materials ceramic balls are provided to polishing manufacturers, then bearing manufacturers, after which they are utilized primarily by European and U.S. automobile manufacturers. Toshiba’s expertise and technological ability, as well as its advanced AI-based quality inspections, is what makes this—and their 50% world market share—possible. Here, we take a look at the AI-based quality inspections Toshiba is using for these ceramic balls.
Toshiba’s patented, high-performance ceramic balls
Get in an EV for the first time, and you’ll feel for yourself the automobile of the future, and the ways in which it differs from a gasoline-powered vehicle. No characteristic roar of the engine, even when you floor the accelerator, and yet the car accelerates—smoothly, silently, powerfully. This distinctive feel is made possible by the motors, and the bearings that are essential to these motors.
“Bearings are parts in machines that allow shafts to rotate in a smooth manner. They’re comprised of an inner ring, a ball, and an outer ring.” So explains Katsuhiko Yamada of Toshiba Materials. The inner ring, ball, and outer ring of bearings are typically made of metal. The high power required of EV motors, however, can cause a phenomenon called electric corrosion, which has long been an issue with these bearings.
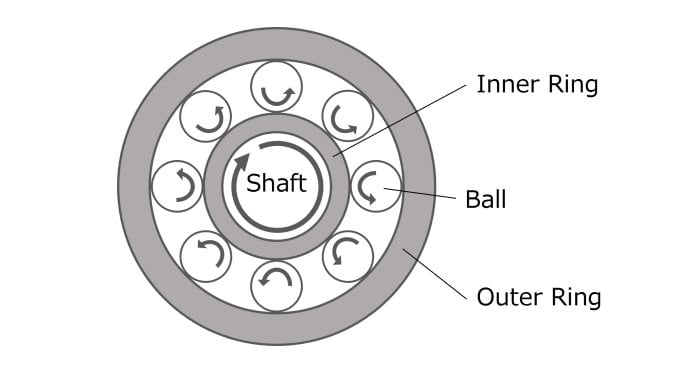
Schematic diagram of a bearing
“The shaft is attached to the inner ring, with balls between the outer and inner rings. The balls are what allow the shaft to rotate in a smooth manner. The balls should always be in contact with the inner and outer rings, but there are inevitably tiny gaps that are created between the balls and the rings. When electricity passes through these gaps, the electrical discharge can cause sparks, which damages the balls. This is what’s called electrical corrosion. High-power motors are especially prone to electrical corrosion due to the shaft rotating so rapidly,” says Yamada.
Bearings cannot be easily replaced once a vehicle is assembled. In the U.S., bearings used in EVs are expected to be of high enough quality to withstand long distances. High-performance bearings would drive the widespread use of EVs, and contribute to the push towards carbon neutrality. The electrical corrosion phenomenon had hampered these efforts, but not anymore—therein lies the beauty of Toshiba’s ceramic balls.
What is it about ceramic balls that prevents electrical corrosion? “Ceramics are insulators, meaning they don’t conduct electricity,” Yamada explains. Ceramic balls, he continues, are also less than half the weight of metal, highly heat-resistant, and resistant to things like corrosion and rust caused by acids and alkalis.
Behind-the-scenes of Toshiba’s development of an AI-based quality inspection system
Increasing demand puts a substantial burden on the quality inspection side of the process. Initially, quality inspections for the ceramic balls consisted of visual inspections, conducted by inspectors who had passed in-house testing. The aging of experienced inspectors and recent labour shortages, however, resulted in an urgent need for automatic inspection.
The first attempt using an automatic inspection machine did not go very well. Yamada says, “The automatic inspection system was designed to capture images, evaluate the images, and flag defective products. But it wasn’t able to properly evaluate uneven colouring on the ceramic balls.” Part of the ceramics manufacturing process involves baking the material at high temperatures. While experienced human inspectors could intuitively identify small holes and other defects through subtle differences in colour, this proved to be too difficult for machines.
“I’ll admit it now, but by that point, I’d given up on the technology,” says Yamada with a wry smile. “I shelved it.” That is, until Toshiba’s Corporate Manufacturing Engineering Center came to the rescue.
Taisuke Washitani of the Corporate Manufacturing Engineering Center recalls the situation at the time. “At the time, we were promoting the automation of manufacturing and inspection processes. I was visiting a lot of different sites, and Yamada’s was one of them. As soon as I saw the images being fed into the automatic inspection machine, I knew intuitively that this task is well-suited for AI deep learning,” says Washitani.
He immediately proposed an AI-based quality inspection system, and the shelved inspection machine has come back to life, but in a different way.
“The Corporate Manufacturing Engineering Center places the needs of the site first. We try to maximize the utility of the devices and technologies used in these sites to improve the manufacturing process. In this case, we were able to make use of an automatic inspection machine that photographs balls while rotating them. We determined that if we can come up with an AI system that can evaluate whether the images are good or not, then the machine would definitely become useful,” says Washitani.
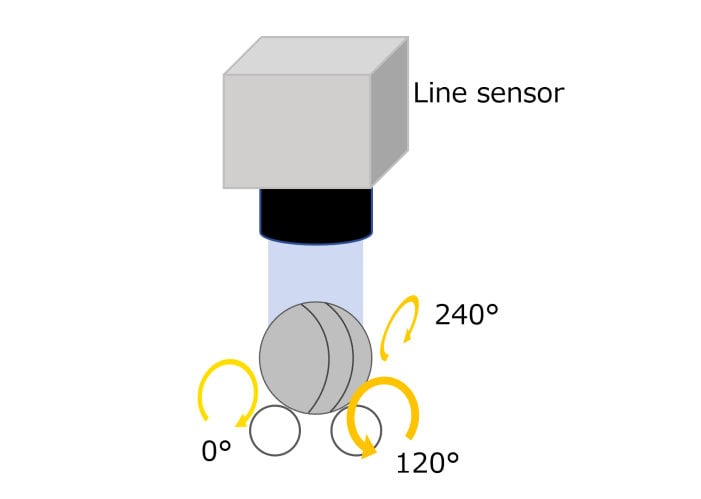
Capturing images of a ceramic ball while rotating them in three different directions/angles, using a line sensor
A typical deep learning algorithm was used for the AI system. “The hard part wasn’t developing the algorithm, but in the more tedious parts,” says Washitani, reflecting on the fact that the AI system did not perform as expected in the beginning.
“AI learns from the data created by people. When the data contains ambiguities, i.e. images that would be marked defective by some inspectors but not others, the AI’s judgement also becomes ambiguous. Therefore, we weren’t able to get the kind of accuracy that we needed.
What we ended up doing to improve the accuracy was simply to not feed any ambiguous images to the AI. This was a tedious way to solve the problem, but it worked. Once the AI became relatively usable, we implemented it in the sites, and had people check the AI’s judgment to improve the algorithm. The process took a long time, with the AI learning like this for about a year and a half, and the algorithm improving little by little,” says Washitani.
How MLOps dramatically reduces inspection times and labour costs
And so the AI system was implemented for quality inspection. This, however, was just the beginning of the story. This is because the accuracy of this kind of AI quality inspection fluctuates with the slightest of changes to preceding conditions, such as the way that the light hits the ceramic balls or changes to the material itself. In order to maintain accuracy, the AI system must be adjusted to account for these changes. In other words, it is not enough to operate the system—it must also be maintained. This is where MLOps comes in.
MLOps is a term that combines “machine learning” with “operation.” Tomoya Kobatake, who develops MLOps systems at Toshiba’s Digital Innovation Technology Center says, “These systems automate the entire life cycle of an AI system, from checking accuracy to updating its learning processes.”
“Our ceramic balls go through slight changes about every year and a half due to changes in material and other factors. To keep up the accuracy of the quality inspections, we have to continually update the AI system itself. The MLOps system automates that process,” says Kobatake.
Earlier, Washitani mentioned the “tedious” way in which they had initially improved the accuracy of the AI system. “I think if we’d used MLOps from the start, we could’ve done that more efficiently,” he says. It turns out that the MLOps system in question had not been ready in time for the development of the ceramic ball quality inspection AI. As such, it had been implemented after the AI system was already in operation.
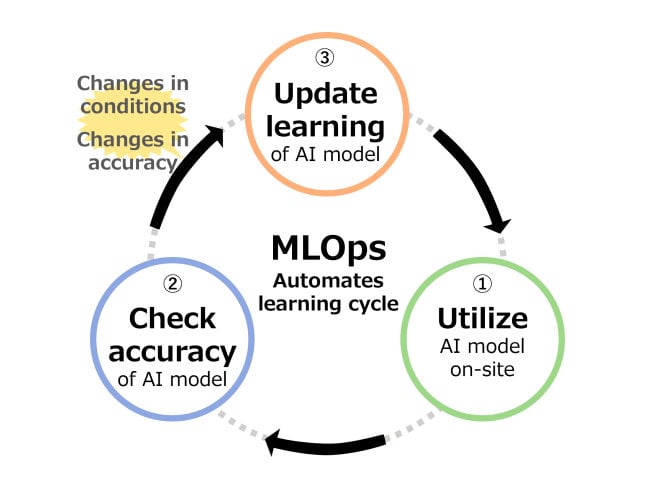
MLOps system
“By implementing MLOps across all of our AI systems going forward, we would be able to shorten development times, maintain and improve accuracy, and reduce the manpower needed to operate the AI systems. The team in charge of the MLOps system is small and flexible, the company itself is making and implementing decisions quicker, and there’s a lot of horizontal collaboration going on. We want to use these strengths to implement MLOps in all the different areas of Toshiba,” says Kobatake.
This was how the AI-based quality inspection system for the Toshiba ceramic balls came to be. And indeed, it has been noticeably effective at resolving the labour shortage issue that the process has long faced.
“We’ve been able to dramatically reduce the time spent on these inspections. Ceramic balls are expensive compared to their metal counterparts. They have so many different strengths, and yet they haven’t been able to replace the metal ones precisely because of this particular issue. If we’re able to reduce the cost through AI quality inspection, we’ll be able to lower the price of the products themselves,” says Yamada.
As mentioned at the start of the article, the use of EVs is accelerating with the push towards carbon neutrality. This will mean a further increase in the demand for ceramic balls. Toshiba’s plan is to build a new production building and increase production capacity by 150% of what it was in FY2021.
www.toshiba-clip.com