www.industryemea.com
11
'15
Written on Modified on
ADVANCES IN FILTER TECHNOLOGY FOR INDUSTRIAL WATER PROCESSING
As an increasingly precious resource, appropriate treatment of industrial or municipal waste water is vital to achieve maximum recyclability while minimising the use of valuable, expensively processed drinking water. In light of growing global resource shortages and the cost of processing ‘new’ fresh water, effective treatment of used water or water for non-potable use is vital to reducing overall process costs and helping companies meet their environmental targets, whether these are self-imposed or governed by legislation.
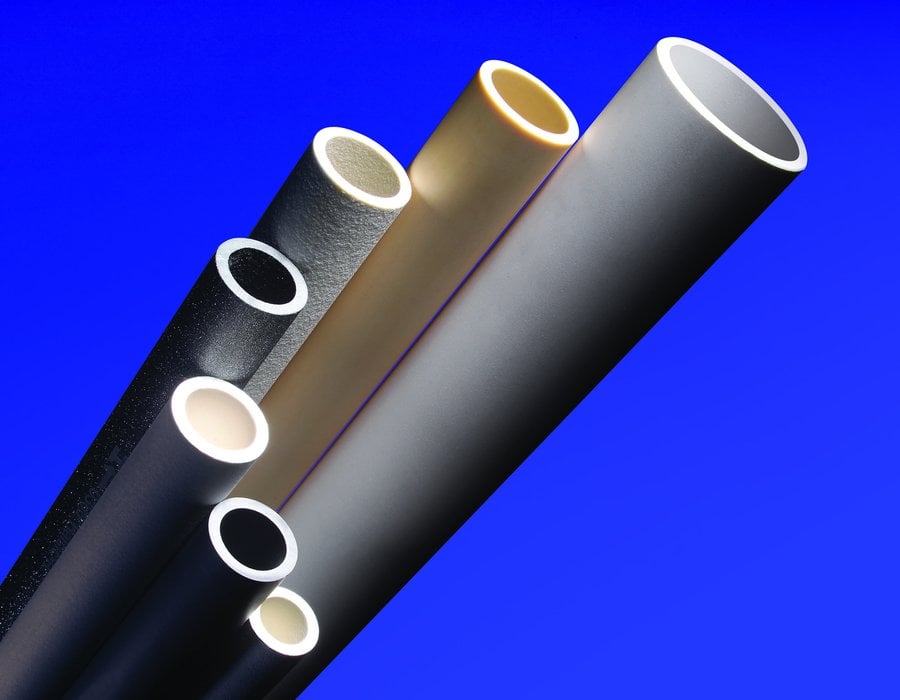
Either way, the nature of contaminants within water places severe demands on filtration media. The presence of sand or grit inevitably contributes significantly to the abrasiveness of the water being processed, placing significant physical demands on materials used in the filtration process. If the erosive effect of these contaminants reaches the point at which the filter itself fails, then the process will no longer be reliable. This means that a material with the toughness to withstand harsh abrasives must be selected for the filter.
Similarly, the potential chemical effects of the process water on the filtration media must be considered. Depending on its source and how it has been previously used, process water can be either highly acidic or alkaline in nature, or may contain aggressive chemicals. Any of these could potentially damage a filter unable to withstand their corrosive effects, thereby compromising the filtration process.
Finally, the ability of the filtration media to enable a good flow of the process water through the membrane must be considered. This attribute, known as flux property, is vital in allowing sufficient flow to process water at the required rate, but not at a high rate which impacts the quality of filtration, or that system pressure builds up to the point that other equipment, including the filter itself, may be damaged.
It is worth noting that any premature or undetected failure of the filter can have disastrous ramifications for other processes over and above the deleterious effect on the filtration process, with the potential for gradual or even catastrophic damage to downstream equipment and a complete halt to water processing. The lack of water will inevitably impact other processes and has the potential to bring all areas of production to a complete stop. Failure of any kind will in any case necessitate a delay in processing while the filter is replaced.
The choice of materials is not just vital for these reasons, however; incorrect filter specification can also result in lower filter service life, and unnecessarily high pumping pressure, with a concomitant effect on energy usage and therefore costs and environmental footprint.
Traditionally, specifiers of filters for these applications have had a choice between metals and polymeric materials. However, to date, few of these materials have been found to offer the desired performance attributes in all three key areas of mechanical resistance, chemical resistance and flux properties.
This issue and the drive for greater reliability and capacity in industrial water processing has driven the manufacturers of filters to seek to use alternative materials able to offer all three of these properties, without compromising on the effectiveness of filtration.
Two materials have come to the fore in recent years, both of which are ceramics. Formed by the action of heat and subsequent cooling, ceramics are inorganic, non-metallic materials made from compounds of a metal and a non-metal, delivering exceptional strength and stiffness when compared with metals or polymers. Alumina (Al2O3) enables the creation of extremely fine pore sizes, vital when purity is at a premium. Silicon carbide, on the other hand, delivers exceptional performance in terms of resistance to both abrasion and corrosion and so is ideal for the treatment of water containing particularly large or aggressive particles, or water containing particularly aggressive chemicals.
As well as these three properties, specifiers of filters must also consider the materials that need to be removed from the process media, the design – typically the choice is between a flat or tubular filter – and the cost of the system. Compatibility with other equipment is key to delivering optimal filtration performance and some suppliers of ceramic filters now offer complete systems comprising a carrier and membrane layer.
These are increasingly the choice of specifiers seeking a durable solution that delivers consistent filtration performance with a long service life.
For further information visit http://www.morgantechnicalceramics.com/materials.
Klaus Prosiegel, Morgan Advanced Materials