www.industryemea.com
06
'23
Written on Modified on
The IE5+ synchronous motors from NORD DRIVESYSTEMS Pioneering in saving CO2 and material
The European standards DIN EN 60034-30-1: 2014-12 (mains operation) and DIN VDE 0530-30-2: 2019-02 (frequency inverter operation) define the four efficiency classes for electric motors from IE1 to IE4+. Based on the underlying criteria, even more efficient drives are known as IE5 within industry.
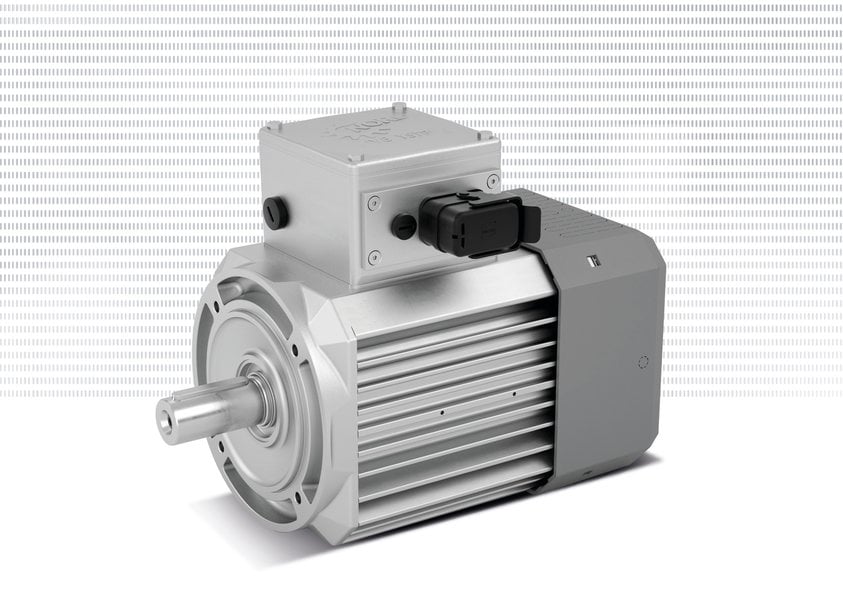
The IE5+ permanent magnet synchronous motorfrom NORD DRIVESYSTEMS significantly exceeds the highest efficiency class IE5. The especially compact and energy-efficient motor offers a constant high efficiency of up to 93 percent and more over a wide torque range and thus also develops optimal energy performance in partial load and partial speed ranges.
Significantly lower CO2 emissions than IE3
This means that the IE5+ motor not only saves energy, but also emissions. In comparison to a conventional IE3 asynchronous motor, an IE5+ synchronous motor reduces emissions by around 0.15 t CO2 per year. This applies to one single motor. In large systems, for example in intralogistics with hundreds or even thousands of drives, this adds up to an impressive total saving. This model calculation is based on the following assumptions:
• IE3 asynchronous motor with 0.75 kW, 83% motor efficiency and helical bevel gear unit
• IE5+ synchronous motor with 0.75 kW, 93% motor efficiency and helical bevel gear unit
• Period: 16 operating hours per day, which corresponds to 4,000 operating hours per year
• Energy savings of the IE5+: around 400 kWh per year
• Reduction of emissions: 0.15 t CO2 per year (with a CO2 emissions factor of 366 g/kWh)
Savings not only in energy – also in material
The IE5+ motor from NORD can also impress with another sustainability factor: material efficiency. “Various innovations in the motor design help us to realise significant material savings with our new IE5+ series”, Jörg Niermann, Head of Marketing at NORD, emphasises. NORD DRIVESYSTEMS designed the IE5+ as an 8-pole synchronous motor in an IPM design. This reduces the size of the motor’s active components, which not only results in material savings in the sheet metal package but also in the magnet material.
Less rare earth elements
In the course of material savings, it was also possible to reduce the proportion of rare earth elements in the magnet material. Rare earth elements are mainly found in Russia, China and Brazil and can only be mined with great environmental impact. “We are glad that we were able to significantly reduce the use of this material”, Niermann explains.
With 8-pole synchronous motors, the stator can also be manufactured with the so-called single-tooth windings. As a result, valuable material such as copper is only used where it is actually productive, and inefficient use in the winding head is reduced.
“Our IE5+ synchronous motor combines energy efficiency with material efficiency and thus scores twice in terms of sustainability”, Niermann highlights. Of course, this not only applies to the IE5+ motor itself but also to the DuoDrive geared motor, in which the IE5+ is integrated.