Voith supplies technologies for successful PM 2 rebuild at Schumacher Packaging in Myszków, Poland
Voith and Schumacher Packaging have successfully started up PM 2 in Myszków, Poland. Except for a few existing components, the entire production line was modernized to achieve the highest sustainability and efficiency standards.
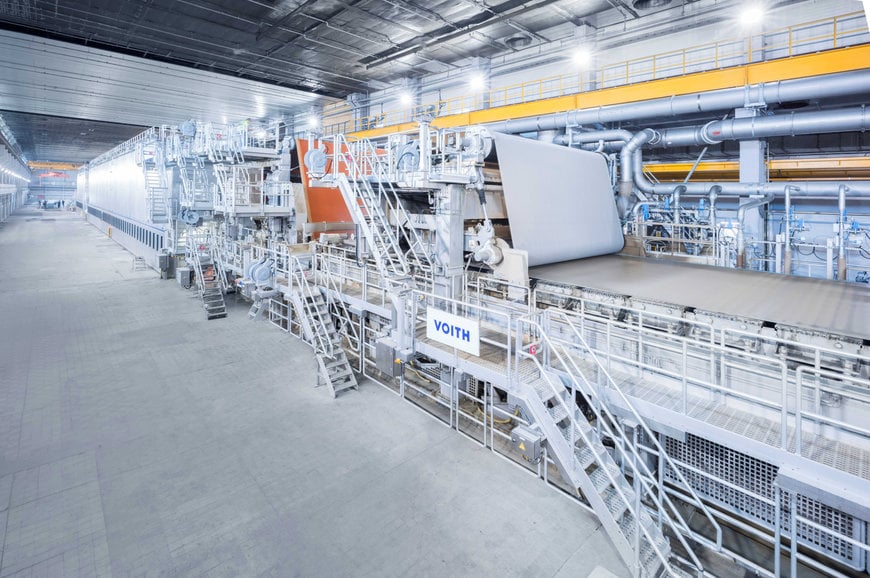
- Voith provides the latest technologies for stock preparation, paper machine and winder, minimizing interfaces and risks.
- Rebuild will double production capacity of PM 2 for lightweight containerboard grades, while increasing sustainability and efficiency.
"We are very satisfied with the rebuild of our PM 2 by Voith. As a leading full-line supplier, Voith was able to reduce many interfaces and thus reduce significant risks during the rebuild," confirms Björn Schumacher, CEO Schumacher Packaging Group.
Rebuild doubles production capacity with high sustainability, machine availability and process efficiency
The successful rebuild of the PM 2 will significantly increase the production capacity of lightweight containerboard grades. In the interest of the customer, the highest priority was placed on sustainability, machine availability and process efficiency when planning the rebuild.
"The rebuild enabled us to double production capacity from 500 to 1,000 tons per day in a way that minimizes waste and reduces fiber, energy and freshwater consumption. We are glad to have found a long-term partner in Voith, which also pursues ambitious sustainability goals and thus has the right products in its portfolio," says Henryk Drechnowicz, Managing Director at Schumacher Packaging Myszków Paper Mill.
Voith had already modernized the plant’s OCC stock preparation line in 2018. To meet the increased production capacity and further increase plant efficiency, the OCC line has now been expanded with additional technologies from Voith’s BlueLine portfolio; sensor technology from BTG; and technologies for water, reject, and sludge handling from Meri.
"Schumacher Packaging has found in us a long-term partner who shares the same values. This has led to a particularly close cooperation between the project teams," says Philip Schnellinger, Process Technology Manager at Voith Paper. "I am proud that we as a full-line supplier with our comprehensive portfolio were able to meet all requirements and guide the project to this important milestone."
Best production quality through innovative technologies
State-of-the-art machine concepts – including a DuoFormer D, MasterJet Pro headbox and DuoShake DG – ensure the best possible quality for profiles and paper strengths. Other advantages include lower operating costs as well as fast and smooth grade changes. In addition, the press section was renewed and equipped with Voith's NipcoFlex technology for two shoe presses, which significantly increases dry content and capacity and reduces specific steam consumption.
A fully automatic VariFlex NG winder with its proven technology rounds off the major rebuild. This features the unique Gecko OneStep system, which enables web separation as well as start and end gluing in just one step. In addition, it ensures stable winding quality at maximum speed thanks to an integrated drive control and the innovative SmoothRun hydro-pneumatic damping system.
www.voith.com