SECO TO DEMONSTRATE STUDIOX AI PLATFORM FOR TAILORED BUSINESS SUPPORT AND CUSTOMER EXPERIENCES WITH STATE-OF-THE-ART TOOLS
Visitors at embedded world Exhibition & Conference, Nuremberg, to discover how to unleash configurable, customisable, trainable chatbot for business performance improvement.
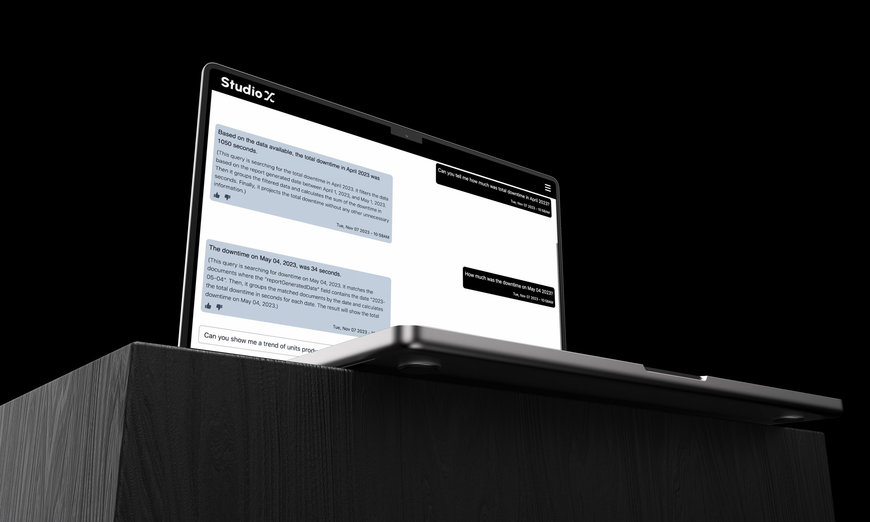
SECO, a global leader in delivering end-to-end technological solutions for industrial digitalization, has released the StudioX AI platform for businesses to create AI-powered support services that enhance internal roles as well as customer experiences. Visitors to embedded world Exhibition & Conference 2024 will be able to interact with applications developed on StudioX at the SECO booth, 1-320 from April 9-11.
Businesses can build tools with StudioX that present a chatbot for users to interact and quickly find information or support they need. The platform leverages cutting-edge technologies including generative AI, Large Language Models (LLMs), machine learning, deep learning, and computer vision. Services can be tailored to support roles such as operations management, workflow analysis, research and development, and product marketing, to boost productivity, elevate product quality, increase business efficiency, and help create new revenue streams. Interacting directly with the StudioX chatbot front-end, users can navigate a vast data landscape to quickly obtain accurate and timely information to guide their decisions. StudioX is available via SMS, web, phone, email, and WhatsApp.
This means StudioX is an ideal platform to create powerful customer experiences that cut waiting times and increase satisfaction. Multiple-language support enables services to cater for diverse linguistic preferences and services can be customized, with analysis to identify patterns and drive continuous improvement.
This Enterprise AI tool can be trained using organisational data such as manuals, technical specifications, and troubleshooting guides, quickly becoming a tool capable of providing instant assistance. In operation, StudioX can ingest data directly from operational equipment, such as machinery on the factory floor, and provide access to AI-generated knowledge in real time. Moreover, the customised StudioX is always available and provides multi-language support.
An operations manager can quickly get information about production status, equipment downtime, defects and other performance criteria, interacting through StudioX’s natural-language interface. Staff in other roles, such as R&D, can filter information from datasheets and other sources, create graphs using StudioX generative tools, greatly simplifying and accelerating information retrieval.
Embedded world Exhibition & Conference visitors can engage with StudioX at SECO’s booth, interacting via the chatbot to see how StudioX can analyze time-series data, parse and compare many types of documents, and classify data from diverse sources such as image sensors, cameras, and audio. When integrated with real business systems and workflow, StudioX can provide advanced predictive and forecasting solutions and conduct real-time manufacturing quality inspections.
SECO will present this AI tool alongside the company’s Clea open-source IoT software suite and closely related embedded-development platforms at the exhibition in Nuremberg. The company’s AI specialists will be on hand to guide visitors through the demonstrations and explain how to get the power of StudioX AI working in a real operational scenario.
www.seco.com