Three suspended cranes and six VERLINDE hoists in the injection mould maintenance workshop at PARKER HANNIFIN
PARKER HANNIFIN with its global turnover of €11.5bn is a world leader in movement and control technologies. The company designs, manufactures and markets a wide range of hydraulic, pneumatic and electromechanical components. The Muzillac factory in Brittany employing 130, located 25 km from Vannes, is a plastics injection specialist for products of the FSCE division and for the automatic assembly of instant fittings The factory is ISO 9001, ISO 14001 and ISO TS certified and the injection mould maintenance workshop very recently installed three EUROPONT overhead cranes on each one of which is fitted two VERLINDE hoists.
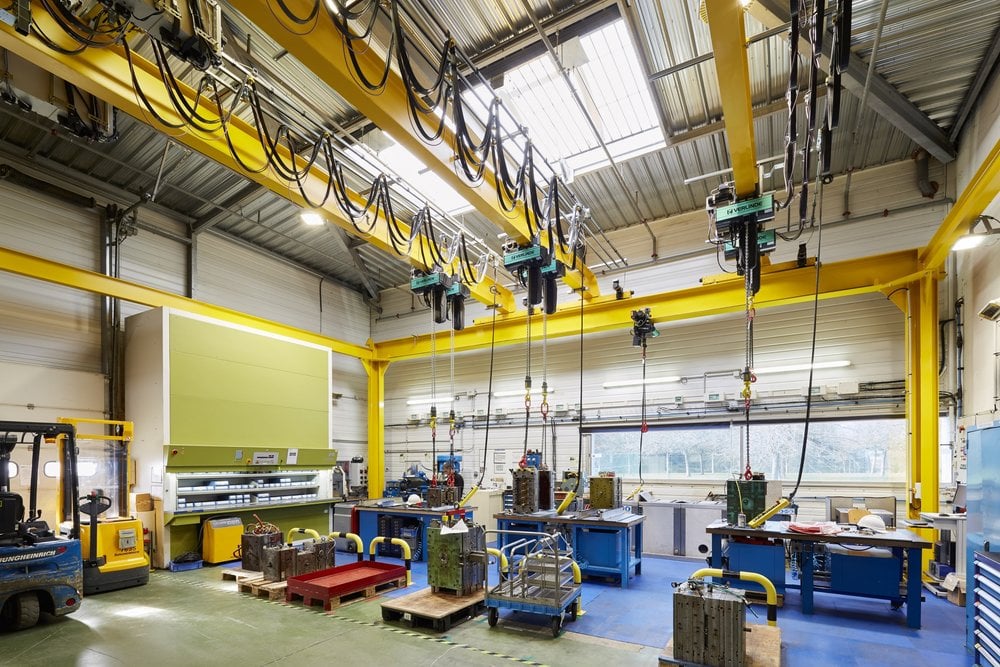
The mould routine maintenance workshop
The moulding workshop
The moulding workshop is the core production activity at the Muzillac plant. Twenty-two Engel, Fanuc or Ferromatik injection presses are served by a suspended crane fitted with a 3-tonne VERLINDE EUROBLOC VT hoist for mould changing operations. These presses are used for the moulding of connectors for small pneumatic hoses and for compressed air system couplings in industrial buildings. For the car industry, five presses are dedicated to the production of motor fuel distribution circuits integrated by Parker Autolive in its manufacturing facilities. Mickael Le Pon, injection facility production manager, explains.”We carry out between 300 and 350 parts series changes per month involving just as many injection mould changes. To ensure the moulding workshop works at full capacity it is first of all vital that the moulds are in perfect condition and as their manipulation can only be carried out with the suspended crane, the latter must be totally available and reliable.”
Mould routine maintenance, a decisive production factor.
Mickael Lepon: “Even if our activity is complex, it has to be understood that it is based in the main on two basic equipment units – plastic injection presses and moulds. To ensure production quantity and quality in phase with our targets, we have to ensure without fail regular inspections and routine maintenance of the moulds because we depend to a large extent on them to guarantee the productivity and the manufacturing quality of our products.”
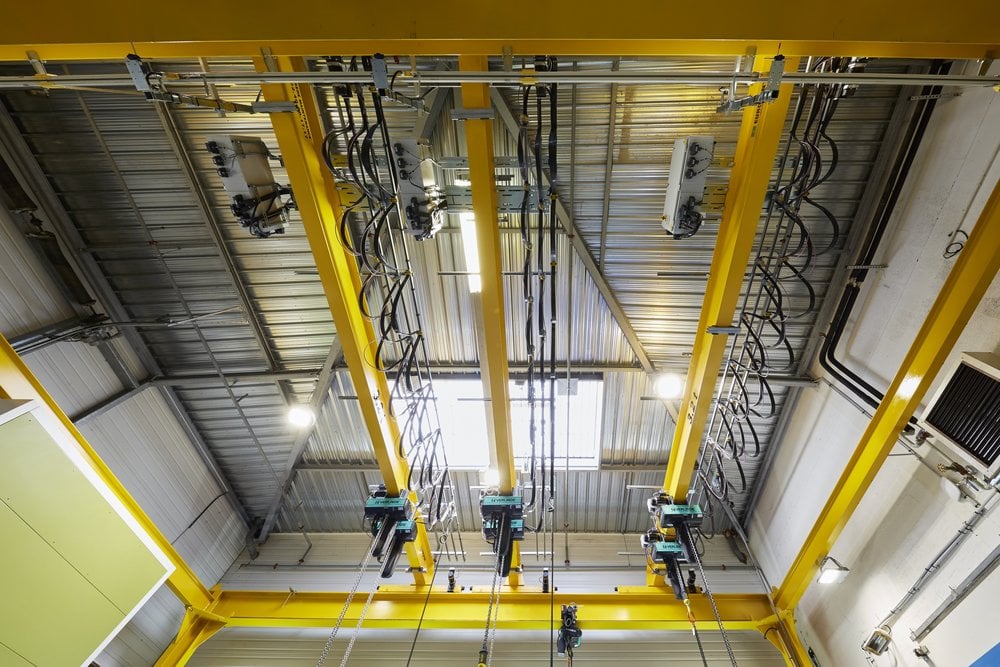
The three suspended cranes. Each EUROPONT suspended crane is fitted with two VERLINDE hoists
A special workshop for mould routine maintenance
The 500 m² workshop dedicated to mould routine maintenance consists of three successive square 10 m x 10 m work stations. After a certain number of duty cycles, the mould is removed, cleaned ultrasonically and the toolmaker is sometimes required to recondition the spindles by electroerosion or replace possible faulty parts.
Installation of suspended cranes and VERLINDE MONOBLOC VT hoists
Before the EUROPONT suspended cranes were installed, a single jib crane served the three work stations. As the manipulation of metallic moulds whose weight varies between 50 and 1500 kg necessitates taking numerous precautions, the toolmakers frequently had their work interrupted while awaiting the availability of the jib crane. It was therefore decided to make each station autonomous with its own suspended crane fitted with two VERLINDE hoists of a lifting capacity of 1.6 tonnes. The three EUROPONT cranes travel on the same metallic structure and to avoid accidental collisions, limit switches guarantee travel safety.
Following this new work organization making each work station autonomous, the productivity of the mould routine maintenance shop has risen by 25%. As moulds are made of two parts whose sizes and weights vary, each crane is fitted with two VERLINDE EUROBLOC VT hoists in order to facilitate their manipulation in complete safety.
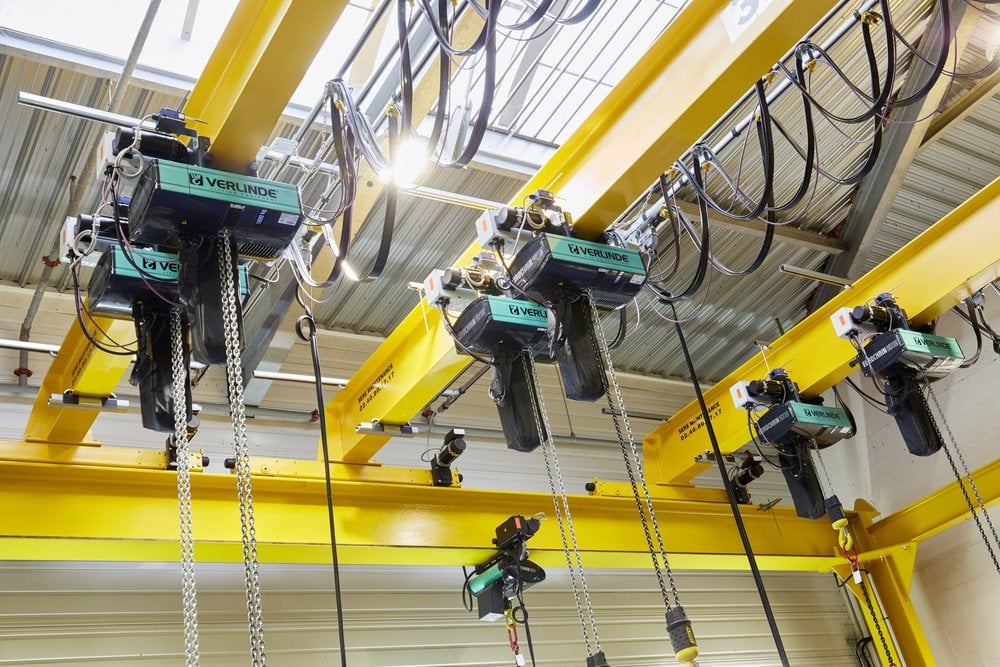
VERLINDE EUROBLOC VT hoists ready to be operated on the suspended cranes.
The selected VERLINDE EUROBLOC VT hoists are fitted with 2-speed motors for lifting and a variable speed motor for horizontal travel. In this way the load is totally controlled horizontally and vertically without any rocking effect. The daisy-chain type power supply is conventional and the control boxes are wired. This solution was in fact preferred to a wireless system for reasons of safety, in order to avoid any possible confusion between the control boxes of the three work stations.
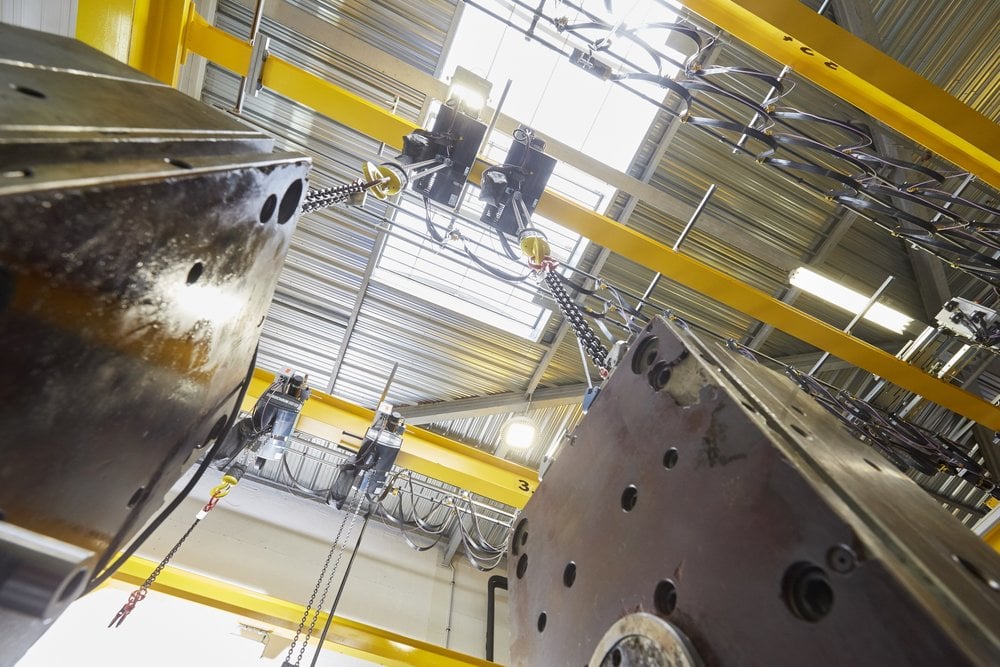
The two parts of a mould raised by VERLINDE hoists.
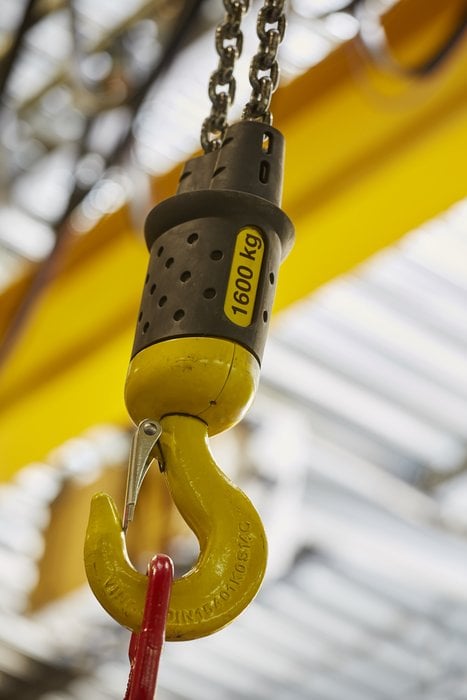
Lifting hook with safety latch
VERLINDE, a long-time partner of PARKER HANNIFIN at Muzillac
Mickael Lepon: “We have enjoyed a relationship of trust with SERE Maintenance for decades and so quite naturally we called upon them to re-organize our mould routine maintenance workshop. They delivered and installed the cranes and hoists and together we inspected the equipment at reception before testing the strength of the metallic structure under load. Our experience with a varied range of Verlinde equipment led us to install EUROBLOC VT hoists whose reliability meet our requirements with a high level of cost effectiveness.
To this can be added the fact that SERE Maintenance is located not far from us making their preventive maintenance service very convenient. In the mid/long term, we envisage installing a second suspended crane in the moulding workshop to be accompanied by a further Verlinde hoist.”
Sere Maintenance, managed by Ludovic Mathis, is a partner of Verlinde and has been a member of the EUROPONT overhead crane manufacturers’ network for more than forty years. A workforce of fifteen ensures the smooth running of the company’s different activities: lifting operations representing 80% of the company’s turnover, together with an activity involving the cathodic protection of metals, mainly for water, gas and compressed air circuits for industry. A whole range of services are also available to customers, such as lifting and handling equipment maintenance.