www.industryemea.com
10
'24
Written on Modified on
Process Reliability in Tube Production: How PackSys Global Optimizes Production Using SIKO Technology
PackSys Global relies on monitored changeovers with digital position indicators from SIKO in tube welding machines.
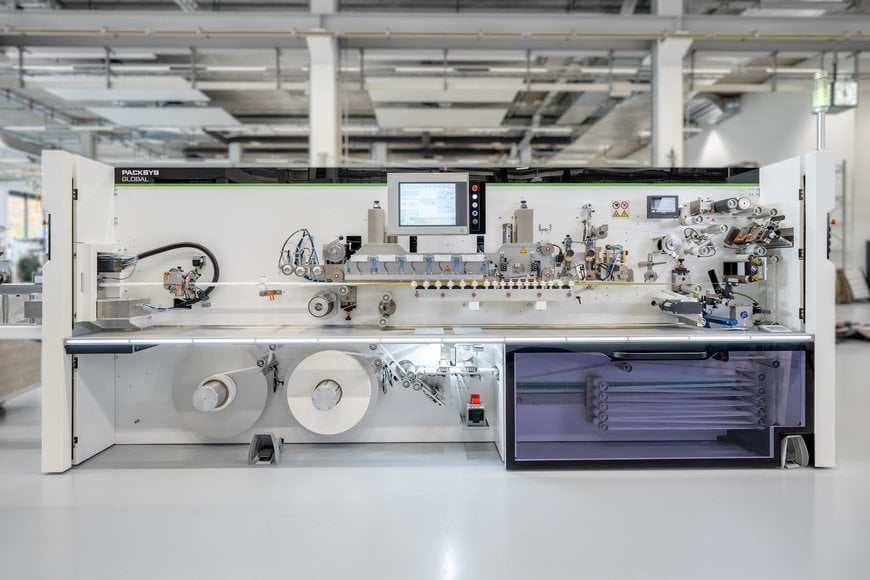
Large tubes, small tubes, long tubes, thick tubes, flat tubes, miniature tubes—tubes are produced in countless sizes and formats for oral care, cosmetics, and in the pharmaceutical industry. The machines that produce the packaging for toothpaste and cosmetic products come from PackSys Global AG in Rüti, Switzerland. The company’s focus is on efficient processes, high output, and ease of use for its customers. This is achieved through increased digitization, automation, and streamlining of process steps. An important aspect that significantly influences process reliability is the proper changeover of machines, specifically the adaptation of settings to accommodate various tube formats. PackSys has integrated a monitored changeover solution from SIKO GmbH, the German specialist for sensors and positioning systems, in order to increase the ease of use of its tube welding machines and ensure the safe adjustment of the various units.
PackSys Global AG, which belongs to the Brückner Group, is specialized in systems for the production of plastic tubes. PackSys Global also supplies hot stamping machines for applying decorative metallized coatings, roll cutting and folding machines for plastic closures, as well as packaging machines for cans, tubes, and closures to transport them from the manufacturer to the filler.
Monitored Changeover in New Tube Welding Machine
Many of the company’s machines require regular changeovers. The most common method to accomplish this is to use mechanical position indicators that are manually set to a position value stored in the documentation. This has a high potential for error, as values may be read and set incorrectly. Especially in the case of frequent adjustments for different tube variants at several positions, the integration of digital position indicators for monitored changeovers is worthwhile as an alternative. The switch to digital position indicators was tested during the development of a new tube welding machine, the FlexSeamer.
The choice for the digital AP05 position indicator with IO-Link interface from SIKO was made for several reasons: It stood out due to its compactness, universal applicability regardless of the axis orientation (vertically or horizontally), and intuitive readability thanks to two LED lights. The displays are used at approximately ten positions throughout the system, for example, to check settings like the thickness or length of the plastic laminates or a varying print image. Another SIKO position indicator, the AP10S, is used to monitor the positioning during linear movements.
From Laminate to Tube
The FlexSeamer is used to unwind a flat belt material, a plastic laminate, from a large roll of material. Depending on the product requirements, the plastics processed are usually material blends that must have good barrier properties in order to minimize the amount of oxygen reaching the product inside and limit the diffusion of aromatic substances out of the tube.
The plastic sheet is folded lengthwise, formed into a tube, and then provided with a longitudinal weld seam, transforming the flat material into an endless tube. The plastic tube is cut into individual sections by a rotary blade. This is the actual body of the tube into which the cosmetic, toothpaste, or pharmaceutical product will later be filled. In a subsequent machine, known as the “Header & Capper,” a so-called shoulder with threaded and capped ends is placed on one of the two sides. The other side is left open so that the contents can be inserted through this opening during filling process and a final transverse weld seam can be applied.
FlexSeamer: High Speed and Reliable Operation
What sets the new welding machine apart is that it features a high speed of 250 tubes per minute, long heating and cooling sections designed for modern laminate types, and intuitive, fast, and reliable operation thanks to the digital capture of most settings. While mechanical position indicators only display the actual value of a position, digital position indicators also show the target value of a setting. For example, the dimensions for a particular type of tube are stored as a recipe in the machine control system and are then transferred to the respective indicators via IO-Link. An operator must then adjust the setting to match the actual and target values. This is the only way to continue with the production process. Reliable indicators here include the two LED lights, which illuminate green only when the values match. As long as a red light remains illuminated on the system, the process must be stopped and readjusted.
For Aitor Henao, Head of Marketing & Communications at PackSys Global, the advantages of such a solution are obvious: “Formats can be quickly and easily adjusted. Any product can be reproduced at any time with exactly the same settings because the dimensions are stored as a recipe for each variant. This means a consistently high level of quality because the processes are stable and reliable at all times.”
Emanuel Heusser, Group Manager Automation Engineering in R&D, emphasizes another aspect that is relevant to quality: “It is often only when products are subjected to random destructive testing, which requires a great deal of effort, that the effects of an incorrect setting become apparent. However, if the digital position indicators ensure that the same settings are used throughout the production process, there is no need for downstream quality control. This is a significant added value of monitored changeovers.
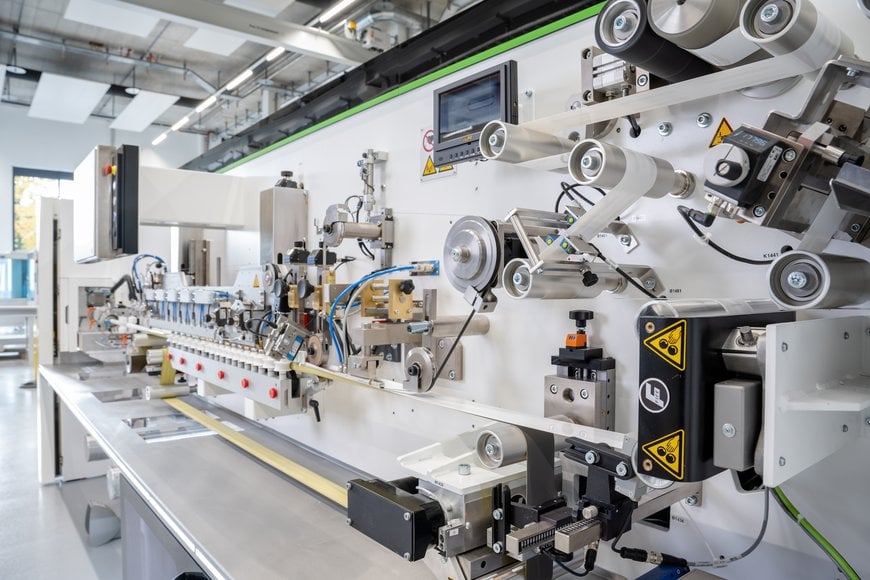
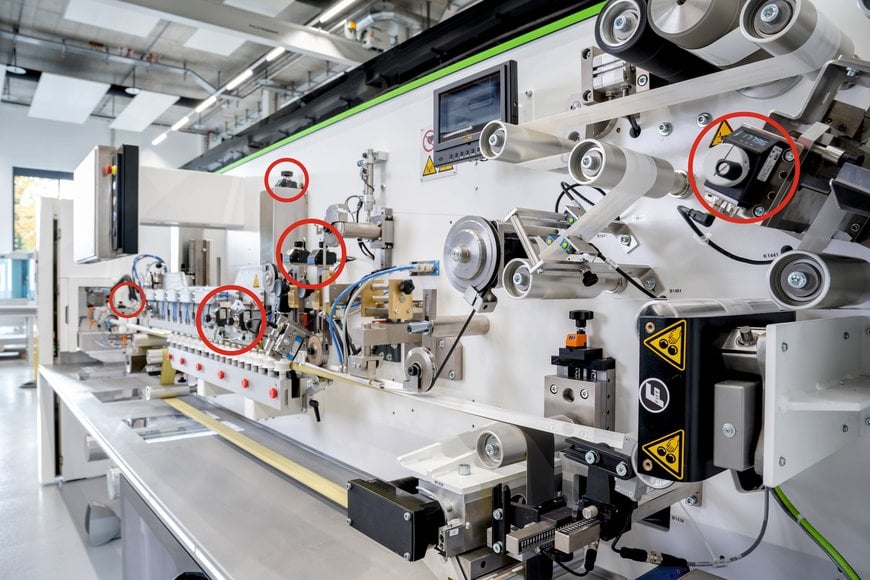
Images 2) and 3) From the plastic laminate to the finished tube: The FlexSeamer is easy to operate and reliable thanks to monitored changeovers from SIKO (markings). Images: © PackSys Global
“Magic Fingers” Are Becoming More Rare
Increasingly, digitized solutions are providing support even in times of skilled labor shortages, says Aitor Henao: “Years ago, there was one skilled worker, who had been with the company for 20 or 30 years, that knew exactly where to make adjustments based on experience, and had ‘magic fingers’ when a setting no longer worked perfectly. However, today we have a very flexible labor market where skilled workers are rare. Intuitive operation that enables process-safe settings without in-depth knowledge of the machine helps companies address the shortage of skilled labor.”
There are many factors to consider when deciding on a monitored changeover. Positions requiring frequent adjustments are ideal for such an investment in digital monitoring. Another argument can be the costly downtime associated with format changeovers. Reducing setup times can be critical. For rare adjustments or situations where incorrect settings are immediately noticeable, PackSys Global continues to use mechanical position indicators from SIKO. These indicators allow for easily controlled position values. Another option from SIKO’s range of solutions are compact, fully automatic positioning drives. These allow size adjustment at the touch of a button. Furthermore, they are also easy to use in hard-to-reach areas of a machine.
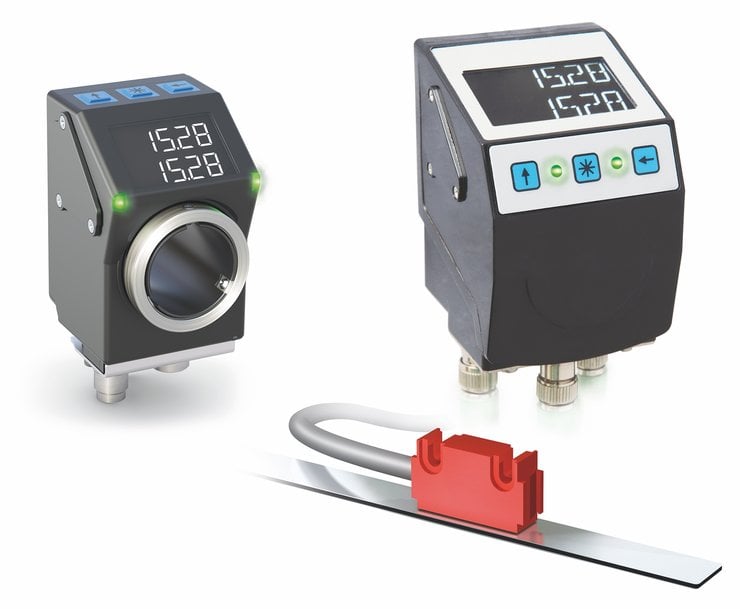
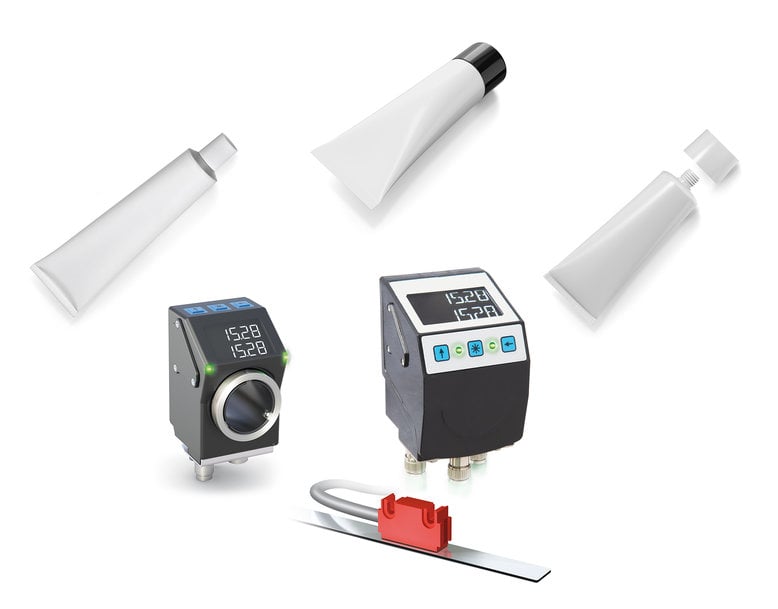
Images 4) and 5) The AP05 (left) and AP10S (right) position indicators always guarantee reliable machine settings for the production of a wide range of tube variants. Image 4: © SIKO GmbH, Image 5: © SIKO GmbH / Istock.com
Example Settings for Print Mark Sensors
The added value of the monitored changeover can be illustrated using an example setting, the print mark sensor: To cut the tube section, the cut must be made in the correct position relative to the print image. This is done by applying printed marks to the laminate, which are detected by sensors. The mark is located in a different place on the circumference of the tube depending on the print image. Therefore, the position of the sensor on the circumference must always be slightly different in order to detect this print mark. The position of the print mark sensor can now be recorded in degrees and stored in the recipe thanks to the AP10S position indicator. This means that the operator does not have to go into the machine to position the sensor relative to the print mark. Instead, the target positioning values are stored for each print image.
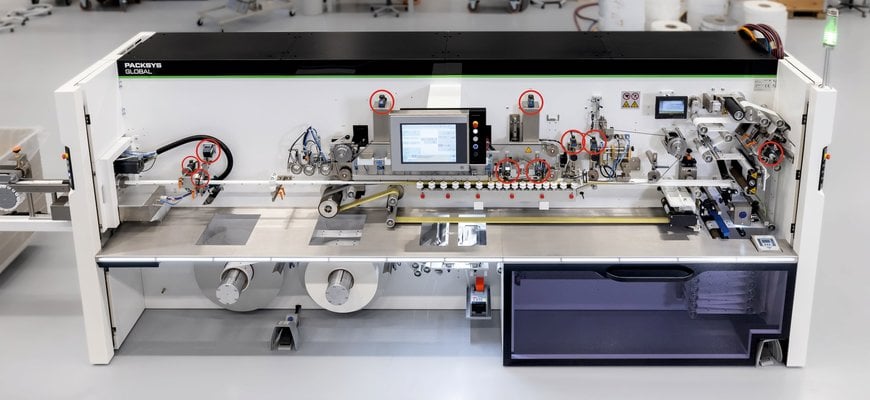
Image 6) The modern FlexSeamer tube welding machine with positioning systems from SIKO for optimized changeovers. Image: © PackSys Global
Integration of the SIKO Position Indicators
For Emanuel Heusser, the universal applicability of the AP05 on both vertical and horizontal axes was a major plus: “The display is angled at 45 degrees and can be configured via the software in regard to how it should be positioned. This also makes it easier for us to stock different products for vertical and horizontal axes. The actual integration proved to be straightforward, both regarding the mechanical design and the electronic integration.” Heusser’s assessment of the cooperation with SIKO is also positive: “There has always been a great deal of goodwill. SIKO aims to make wishes and suggestions a reality. For example the AP05 was specially designed with IO-Link for our FlexSeamer project.”
Looking ahead, Aitor Henao sees a clear trend towards digitization and automation of systems, especially in the area of changeovers: “These small details, such as the LED display, make all the difference. They improve the quality of our machines and services, helping customer companies to focus on their business.”
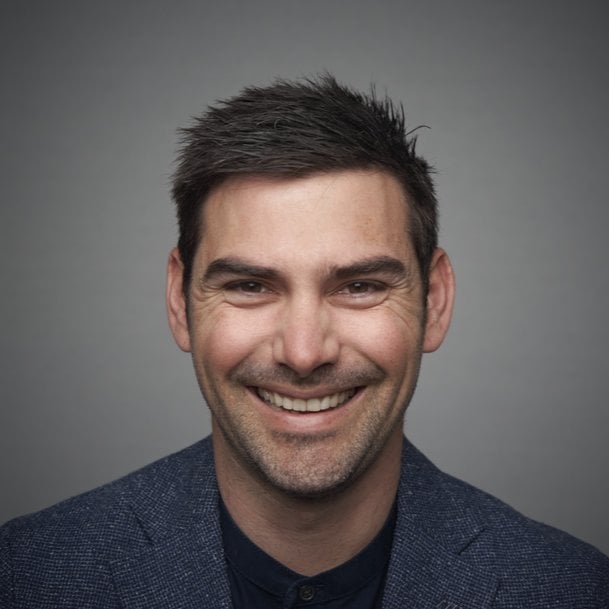
Image 7) Portrait of Aitor Henao, Head of Marketing & Communications at PackSys Global. Image: © PackSys Global
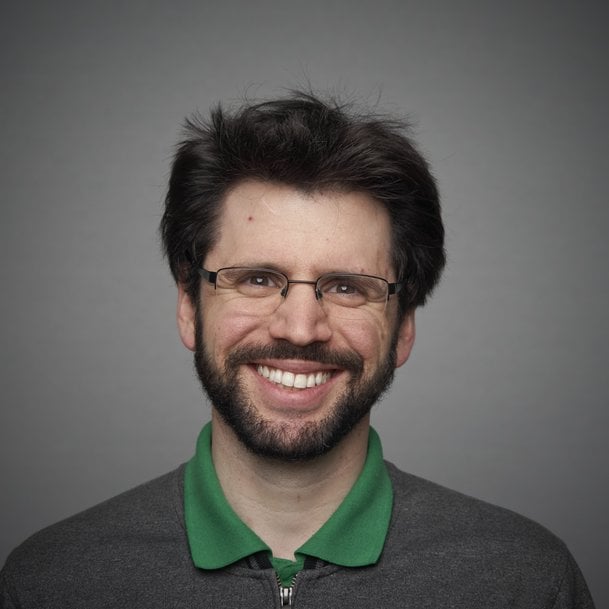
Image 8) Portrait of Emanuel Heusser, Group Leader Automation Engineering in R&D at PackSys Global. Image: © PackSys Global
Author: Michaela Wassenberg, Freelance Journalist
www.siko-global.com