www.industryemea.com
29
'16
Written on Modified on
NSK replaces spindle bearings on large surface wheel lathe
The Doppelmayr Graventa Group in Wolfurt, Austria, a specialist in the manufacture of surface and aerial ropeways, has benefited from the expertise of NSK in replacing the main spindle roller bearings on an extremely large surface wheel lathe.
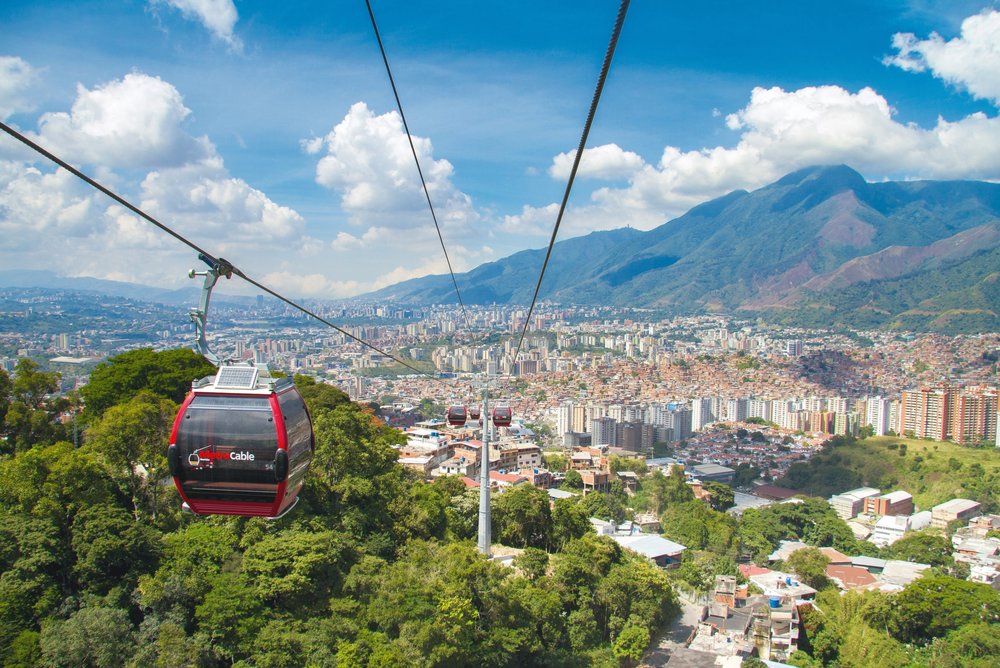
Due to the lathe’s age and the obsolescence of the spindle assembly, the project entailed a significant amount of reverse engineering, supported by the team at NSK, before double row cylindrical roller bearings were specified for the central bearing positions.
Due to the global rise in demand for ropeways, which are seen as an economic and rapid alternative to conventional ground transport in both inaccessible and highly urban landscapes, business at the Doppelmayr/Garaventa Group has seen the manufacture of more than 14,600 ropeway systems for customers in 89 countries to date. The company makes all of the required components for its ropeways in-house, including the large sheaves at the top and bottom stations which guide the main drive cable. The bearing surface of the sheaves must be manufactured with very high precision to ensure smooth operation and secure cable guidance.

The sheaves are machined on a large surface wheel lathe that was rebuilt from an original longitudinal lathe produced many years ago by Zerbt. Although the machine, which has a face plate weighing 30 tonnes, gives good service, Doppelmayr faced a challenge when wear and tear dictated that the main spindle's roller bearings required replacement.
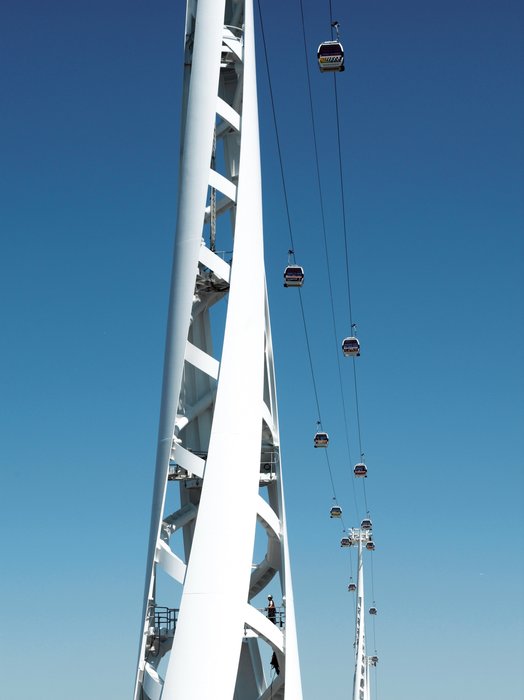
The principal problem in replacing the bearings related to the machine’s age and the fact that the original manufacturer had changed ownership. This meant there was no documentation relating to the main spindle assembly. For this reason, Doppelmayr turned to NSK, which was able to support the company in a reverse engineering project that would help identify the bearing locations and assembly parameters, including the bearing clearance and spacer ring width. NSK also helped develop strategies for replacing the bearings.
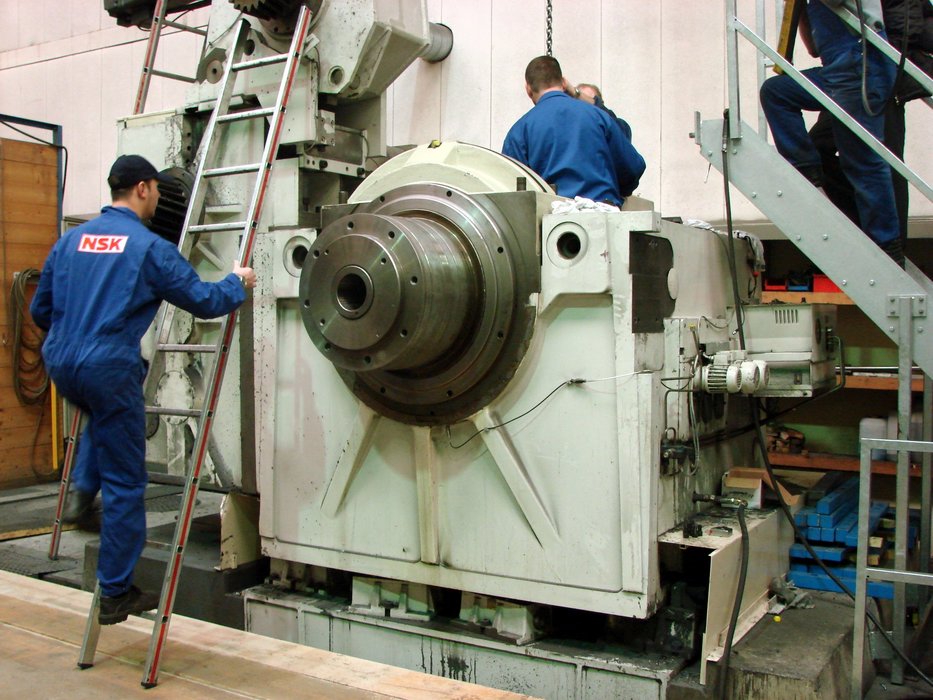
By characterising the installed bearings through reverse engineering, NSK was able to replace them in the central bearing positions with high precision double row cylindrical roller bearings in the correct sizes. The replacement took place during a planned maintenance period so that production schedules were unaffected. For the axial bearings, spacer rings were measured after setting the clearance and new ones manufactured in the required width.
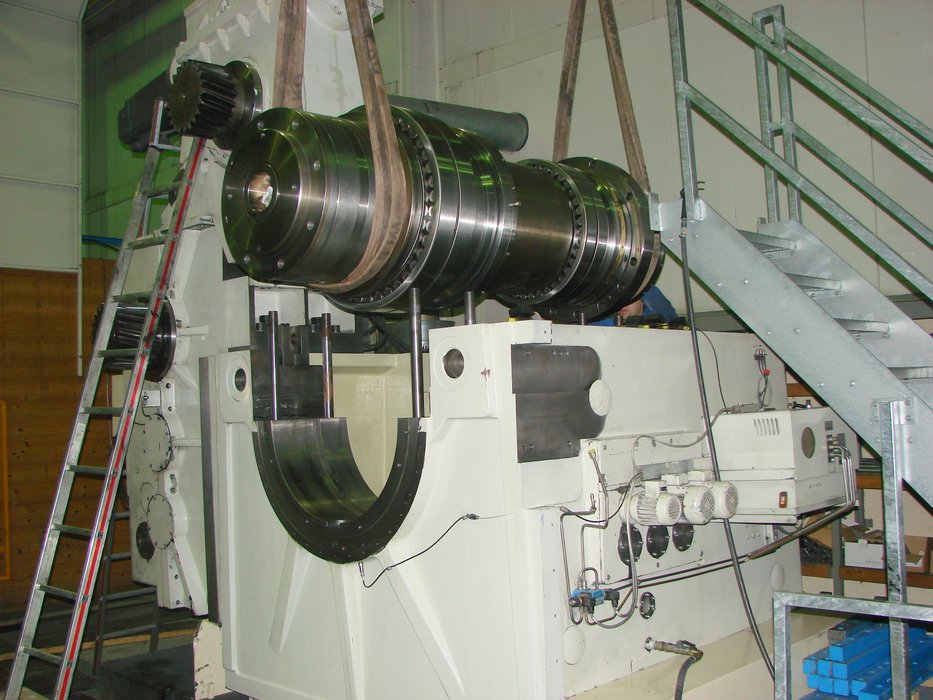
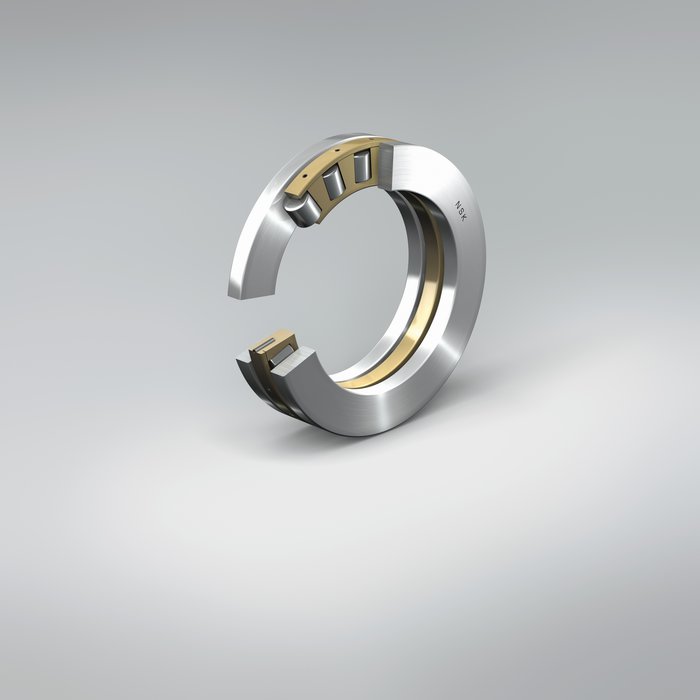
Post-installation, NSK technicians checked the clearance to make sure it was correct. This was facilitated by conducting a dynamic lift test, allowing the loading conditions to be simulated with the bearings installed. The process confirmed that the previously measured value of 0.005 mm had been successfully maintained.
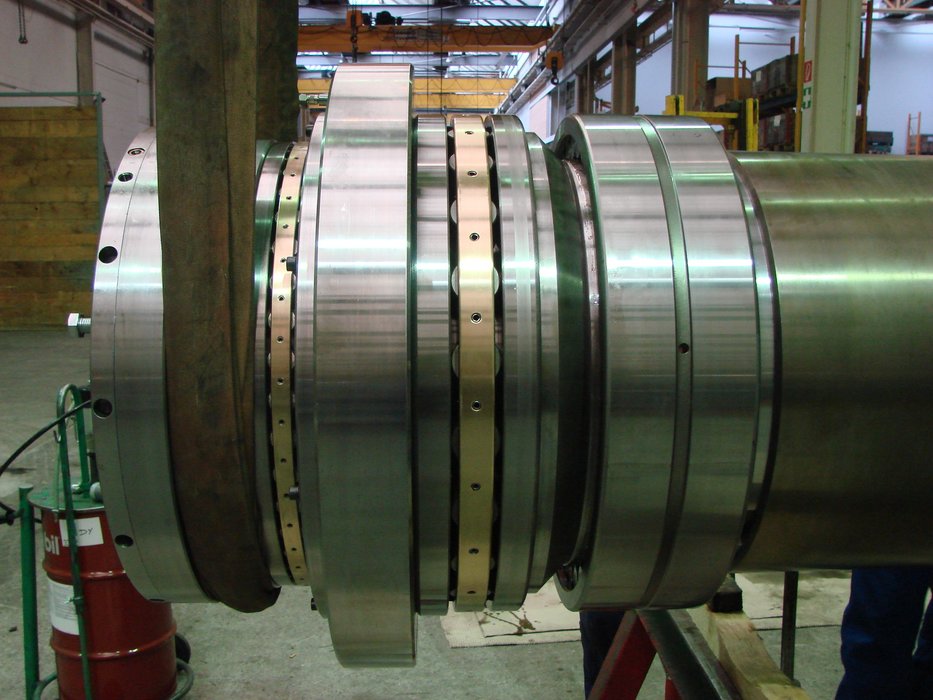
With the project complete and the surface wheel lathe ready to recommence operations, Doppelmayer's maintenance team was given instructions by NSK to monitor the temperature of the bearings during the initial start-up phase. No irregularities were observed and the lathe is now back in full sheave production.