www.industryemea.com
07
'16
Written on Modified on
MORGAN ADVANCED MATERIALS SOLUTION HAS A BEARING ON SUCCESS WITHIN AUTOMOTIVE SECTOR
Morgan Advanced Materials, a global specialist in the development and manufacture of seals and bearings for demanding environments, has delivered a new type of bearing for electric water pump applications in cars which reduces component count, while optimising performance and engine efficiency.
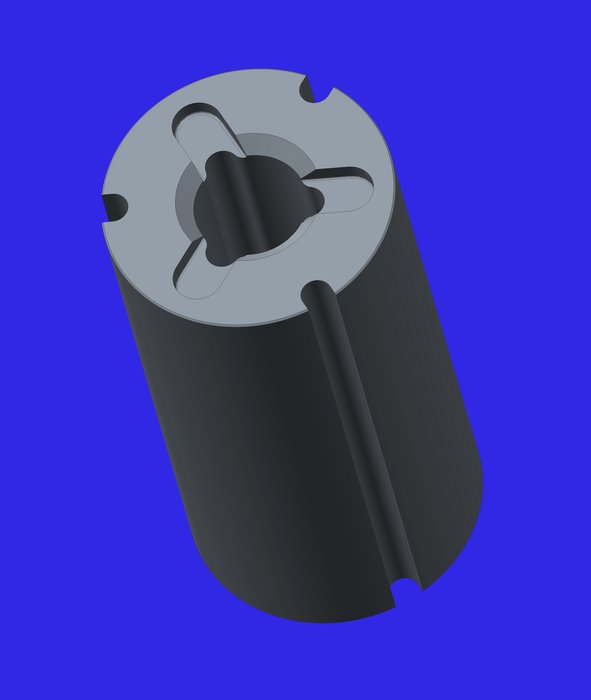
Within the automotive sector, there has been a notable shift from traditional, belt-driven coolant pumps to electrical equivalents, on the basis that these reduce demand on the belt drive, offering a substantial improvement in performance and greater overall efficiency with ‘on-demand’ cooling. The design of these pumps typically feature an impeller shaft which is supported by two bearings. Morgan was approached by a customer with the challenge to provide a less cumbersome bearing solution without compromising overall pump performance and cooling capability.
Drawing on its world-leading expertise in materials science and molding technology, Morgan successfully produced a bearing solution comprised of its P5600H proprietary carbon graphite material with a length-to-diameter ratio of two, which also included numerous face details and inner diameter (ID) and outer diameter (OD) slots. Morgan’s solution was more cost-effective and offered a substantially greater ease of assembly, as well as containing the vital component features which aid lubricaion and prevent slip and anti-rotation.
While engineered plastics can also be used in this kind of application, they are typically not as strong and are more suscepitble to wear and creep. Materials like Morgan’s proprietary carbon are, however, significantly better suited to the demands placed on them. Typically they have longer lifespans due to their impressive tribology, stability at high temperatures and resistance to wear and tear. This is of high importance for bearing components as in the event that one sub-component becomes faulty, the entire unit must be replaced, resulting in additional cost and the disruption associated with increased warranty claims.
Michael Ritter of Morgan Advanced Materials, explained: “Morgan’s proprietary method for producing bearings of this geometry has enabled us to deliver a range of performance advantages otherwise unattainable with conventional molding technologies. Using our unrivalled expertise in the fields of materials science and application engineering, we were able to develop a process that allowed us to provide a superior solution in terms of performance and cost. Our constant focus on innovation and problem-solving is what drives us forward as a business, allowing us to solve our customers’ most pressing engineering problems.”
For further information, please visit: www.morgansealsandbearings.com/water-bearing
Suggested Tweets
.@MorganAdvanced solution has a bearing on success within the motor sector
New bearing @MorganAdvanced reduces component count, while optimising performance and engine efficiency