www.industryemea.com
30
'24
Written on Modified on
Emerson’s New Laser Welder Automates Assembly of Small Plastic Parts with Complex Geometries
Branson GLX-1 platform offers automation-friendly solution for clean, vibration-free welding that supports closed-loop product recycling, in small-part applications for the medical market, the electronics, automotive and appliance markets.
www.emerson.com
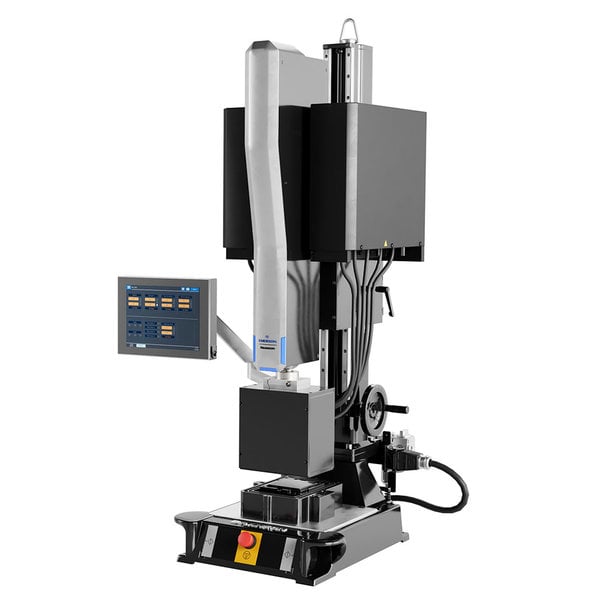
Emerson's Branson™ GLX-1 laser welder revolutionizes the assembly of small plastic parts with intricate designs. This automation-friendly solution ensures clean, vibration-free welding, supporting closed-loop product recycling.
Emerson has announced its new Branson™ GLX-1 Laser Welder, which offers users flexibility to meet the growing demand for joining small, complex or delicate plastic components and assemblies. Its small footprint and modular design make it compatible for use in ISO-8 cleanroom environments, while an integral automation controller simplifies installation and interfaces with production robotics.
The precise, servo-based actuation controls of the GLX-1 welder allow for greater freedom to design and join components with three-dimensional contours in small-part applications for the medical market, such as catheters and wearables with microfluidic parts, as well as sensors in the electronics, automotive and appliance markets. The new welder can join high-performance and blended polymers and components with critical or complex 3D joint geometries or preassembled parts without risk of damage due to heat or vibration. Laser welds are completed without flash or part marking, giving parts a superior aesthetic appearance.
To support device makers’ increased interest in closed-loop product recycling, the GLX-1 can also safely and nondestructively “un-weld” plastics used in common medical devices and wearables. This disassembly capability enables reclamation and reuse of valuable internal components while enhancing sustainability initiatives and reducing waste.
“There is increasing demand for smaller and more intricate high-quality plastic components, often housing sensitive electronic components in a range of important markets,” said Emma Wood, global product manager for non-ultrasonics at Emerson. “Delivering strong, clean joints and advanced connectivity features in an extremely compact package, the new GLX-1 Laser Welder enables manufacturers to design and efficiently produce the highest-quality products.”
The GLX-1 welder relies on Emerson’s Simultaneous Through-Transmission Infrared® (STTlr) laser-welding technology, which delivers unmatched production efficiency, weld strength and aesthetics that typically surpass those that are possible using other plastic welding methods. The GLX-1 delivers weld power using Branson’s high-power laser banks, which offer configurable power levels up to a maximum of 250 watts per bank.
An advanced servo-driven actuator provides precise, repeatable, closed-loop downforce control, from low to high levels. An optional, closed-loop pneumatic control is also available. The results are rapid weld cycle times that support high-volume, high-quality production in a range of applications. Efficient and accurate tool changeover is ensured, thanks to a radio frequency identification (RFID) function that recognizes and matches weld recipes with correct production tooling.
The GLX-1 also provides exceptional connectivity and security, with weld data collection, transfer, and security features simplifying weld-data transfer over internal customer networks. Operational and security features are accessed through the welder’s intuitive, easy-to-use 12-inch touchscreen HMI, which is mounted on a swiveling pendant arm for easy viewing at convenient angles.
The welder ensures maximum security, with 99 levels of customizable password protection. It also connects easily with plant networks to meet industrial Internet of Things (IIoT) or communication requirements, offering Data Interface Gateway (DIG) and Fieldbus interface gateway compatibility, a USB port and an OPC-UA interface.
Find out mor ein this video.
Learn more
www.emerson.com