www.industryemea.com
31
'24
Written on Modified on
YASKAWA: RETROFITTING EXISTING CONTROL SYSTEMS
Older, reliable control systems in automated production are causing concern due to discontinuation, but the retrofit to Yaskawa's 300S+ control system ensures continued functionality.
www.yaskawa.eu.com
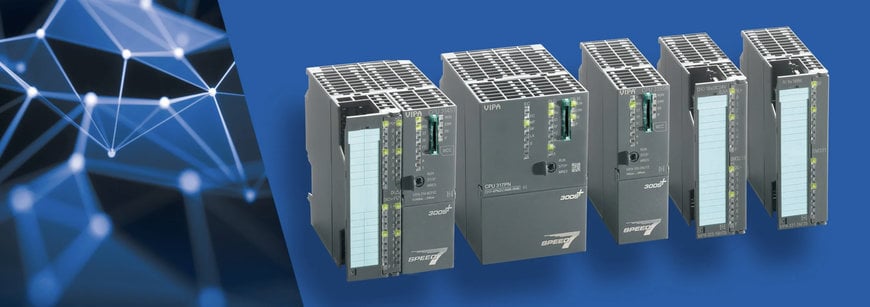
Many of the machines and systems used in automated production rely on older, sometimes analog control system generations, which continue to perform reliably and without any problems. Nevertheless, the discontinuation of a reliable control system in existing machines and systems has caused concern among many users. However, these and the majority of existing control technologies can remain in use. The retrofit and conversion to the 300S+ control system from Yaskawa enables this functionality.
As the control technology in existing machines and systems ages, it no longer meets the required standards for state-of-the-art technology and often fails to meet today's safety standards. In addition, obtaining spare parts is challenging, and in some cases, it is no longer feasible due to product discontinuation. This can lead to unexpected downtimes and high maintenance costs.
However, in order to achieve sustainability within the company, it is essential to utilise existing technology for as long as possible. The prerequisite for this is a retrofit. Replacing old or discontinued hardware components—such as the control system—allows machines to be brought up to the current state of the art. This solution presents a dual advantage in terms of both ecological and economic considerations. The existing systems and production processes are undergoing technical upgrades to ensure that reliability, efficiency, competitiveness, and future-proofing are once again guaranteed.
Control system 300S+
Such a retrofit is possible, for example, with the 300S+ control system from Yaskawa. Since its inception in the 1990s, it has evolved into a dominant system in the market. Over 1.5 million components of the high-speed control system have now been installed in countless machines worldwide. The latest 300S+ model is notable for its speed: it is around ten times faster than comparable systems. The PLC CPUs offer a significantly higher memory size of up to 8 MB (fully retentive) and a range of additional benefits over previous models, all at a competitive price point. Against this background, the 300S+ system with SPEED7 technology is positioned as a reliable and robust controller for even the most demanding applications.
Finally, the system offers not only exceptional processing speeds and capacities, but also a further advantage: The 300S+ series, whether a compact CPU or a fully equipped PLC automation system, is designed to meet a wide range of requirements and applications. It offers particular flexibility, for example, through the inclusion of suitable front connectors for the integrated I/O channels.
Retrofit made easy
This proven technology has a long history of reliable performance and is backed by a substantial inventory of spare parts. This ensures a safe, smooth production process and trouble-free operation. Replacement and commissioning activities are scheduled during a planned shutdown to facilitate a rapid restart of production. The machine's output and performance are enhanced, resulting in increased productivity and quality while also extending its service life. Furthermore, enhanced performance, increased productivity, and superior quality are realized. The machine has been designed with maintenance and user-friendliness in mind, resulting in an extended overall service life. The use of fanless CPUs also contributes to reducing the energy requirements of the control technology.
This flexibility presents an opportunity to explore new solutions that could potentially replace existing ones. In light of the ongoing developments in the automation sector, this represents a suitable option for those seeking to retrofit existing control systems. Many system series from market-leading manufacturers have been successfully in use for many years.
It is evident that functionality, availability, practical experience, and spare parts management are not the sole reasons behind the continued use of the system by numerous operators and maintenance personnel. While digitalization at the management level continues to progress rapidly in automated production, older, partially analog generations of control systems are still in use in many machines and systems. From the perspective of many operators and maintenance staff, the advantages of continued use, including functionality, availability, practical experience, spare parts management, and other benefits, make this a compelling option.
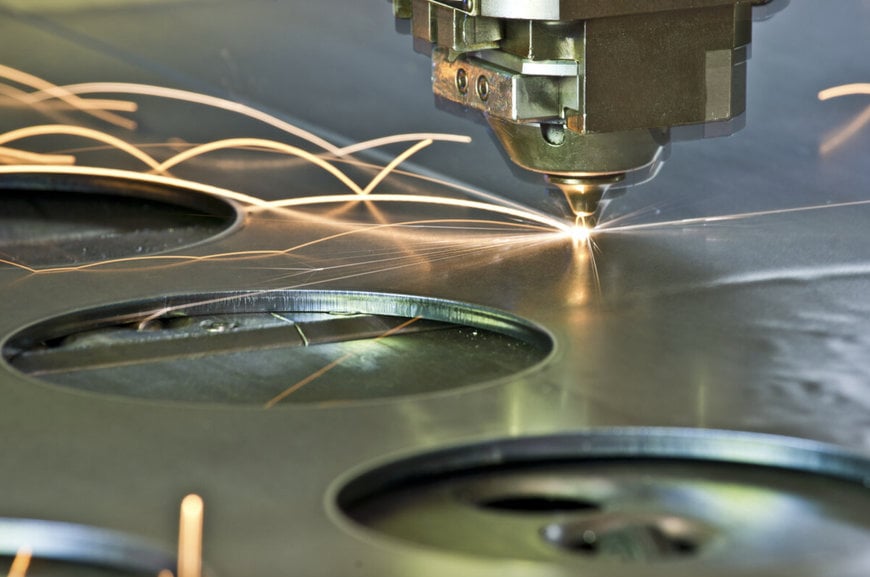
Multiple options
There are multiple general options for retrofitting the existing control system, even in the event that the original manufacturer is phasing out the system or has already discontinued it. Furthermore, the system is designed to meet the highest standards in terms of intelligent memory management, data security, and comprehensive communication capabilities via modern protocols, including an integrated Ethernet connection and a wide range of supported buses. A variety of on-board communication interfaces, including Ethernet, PROFIBUS-DP, and serial RS485, as well as optional extensions, ensure excellent connectivity and integration into existing networks, providing customers with a high level of flexibility and compatibility.
In general, the 300S+ controllers can be programmed via two proven platforms: STEP7 and the TIA Portal from Siemens, or the Yaskawa WinPLC7 software. This provides complete freedom to develop and maintain projects as required. The 300S+ system offers advanced and reliable memory management, including automatic backup functions, with external memory options via MMC/SD cards up to 2 GB and battery-backed RAM.
Furthermore, IOs and accessories from Yaskawa are fully compatible with the previously market-dominating system. All hardware components can be replaced on a one-to-one basis and operated in parallel during mixed operations. Moreover, the CPUs can remain in use with minimal changes to functionality, eliminating the need to replace existing software. Yaskawa offers comprehensive support for the corresponding adaptations in the CPUs, including the "TASK FORCE 300" service, download options, and other useful functions on the Yaskawa website.
Proven system with high speed
A step-by-step retrofit represents a cost-effective alternative to a new purchase. Furthermore, brief periods of production downtime are typically sufficient. Concurrently, the quality of the systems is enhanced, and functionality and performance are optimized. Finally, modernization also offers advantages in the field of occupational health and safety.
The 300S+ control system offers users, machine builders, and maintenance engineers a dual benefit: greater safety in the entire working environment and long-term investment security. While other suppliers are discontinuing their product lines, Yaskawa is committed to ensuring the long-term availability of the 300S+ control systems.
The 300S+ system offers the flexibility to expand the integrated memory as your applications evolve, ensuring a future-proof solution that can adapt to your changing needs. Yaskawa offers a 36-month warranty on the entire upgraded control system, not just the new components. And yet another benefit is that every single component can be supplied directly from stock and will be available until 2030, at the least. This exceptional supply capability is also attributable to the fact that the integrated microchips are based on Yaskawa's proprietary technologies.
Three examples from diverse industries illustrate the distinctive capabilities of the 300S+ control systems:
Building automation in an automotive plant
Yaskawa controllers from multiple generations were implemented in an automotive plant's production line. The decentralized structure was implemented with CPUs, communication processors, and slaves from the VIPA 200V family and communication processors and slaves from the SLIO family, together with the corresponding digital and analog signal modules.
At the time, there were many arguments in favour of the 300S and SLIO families for decentralized stations. The 300S CPU family combines the classic compact 300 design with enormous weight advantages thanks to the integrated SPEED7 technology. Added to this is the usual variety of interfaces, which makes it one of the fastest and most powerful control systems in the world. Thanks to the universal programmability with STEP®7 code and Yaskawa's own programming tools, the system can be used universally and can be retrofitted at any time.
Greater energy efficiency in the cosmetics group
The heating system of a prominent cosmetics company was to be upgraded with the objective of reducing energy consumption. The previous heating system was replaced with a district heating system and a new control system. The company selected PLC technology over other options, such as BACnet, KNX, and LON, which are commonly utilized in building technology. There were several factors that influenced this decision. PLC technology is a ubiquitous feature of industry, with a vast workforce that is intimately acquainted with its intricacies. Spare parts are available on-site and customers are typically able to resolve issues or implement changes without delay. Furthermore, the STEP7 compatibility, the interfaces to PROFIBUS, and the CPU's ability to process and reliably store large amounts of data were additional factors that contributed to Yaskawa's advantage at the time.
The entire energy distribution is now managed by two 315SN-NET CPUs, in conjunction with decentralized SLIO modules. Two 315-4NE12 Ethernet CPUs are in place to ensure the optimal temperature throughout the building. 18 SLIO modules are connected decentrally throughout the plant via 4.5 km of Profibus cable, reinforced by repeaters. They control the energy distribution on site and ensure that the yield per consumption unit does not rise above the desired value - otherwise the quantity is throttled. The success of the modernization project has exceeded all expectations. The company has achieved a notable reduction in heating costs, which is in line with its commitment to sustainability.
Conversion and modernization of bottling plants
A bottler of non-alcoholic beverages used the rebuild and modernization of its bottling plants to equip them with the latest control technology for future requirements. Today, 140 digital I/Os and approx. 15 analogue inputs in the pasteurization and bottling area alone are no problem for the CPU 317SN/NET. The CPU is fully capable of handling the connection to other decentralized signal modules via PROFIBUS and the visualization connection via the integrated Ethernet interface.
The control system takes over the entire control and monitoring of the pumps and valves during pasteurization as well as the regulation of the temperatures, which lie within a narrowly defined tolerance range. Valves, flow meters, conductivity meters, frequency converters, pumps and the visualization are integrated into the control and regulation circuit. The downstream filling machine and packaging are also integrated. A robust data exchange is established between the pasteurizers and the filling machine through the use of an I/O coupling. Once the packages are filled, they are automatically transported to the palletizers, where they are labeled and packaged for safe transport in a film wrapper. This process is also controlled by Yaskawa. Yaskawa controllers demonstrated their ability to meet the additional communication requirements, including extended process data communication and visualization, without any issues.
www.yaskawa.eu.com